Eine sichere Investition: Bohrprozesse auf dem Prüfstand
Diese Erfolgsgeschichte zeigt die Zusammenarbeit mit IMS Gear SE & Co. KGaA in Deutschland.Die IMS Gear SE & Co. KGaA mit Hauptsitz in Donaueschingen am östlichen Rand des Schwarzwalds ist mit rund 3.400 Mitarbeitern weltweit einer der führenden Hersteller im Bereich der Zahnrad- und Getriebetechnik. An drei deutschen Standorten und in Werken in China, Mexiko und den USA fertigt IMS Gear Getriebe, Baugruppen und Komponenten überwiegend für den Automotive-Bereich. So leisten heute in nahezu jedem Auto die Getriebe und Antriebe von IMS Gear als Lenkunterstützung, elektrische Sitzverstellung, Lordose-Stütze, elektronische Parkbremse oder automatische Heckklappenöffnung ihren Dienst. Mit dem Trend zu immer mehr Komfort im Automobil und dem damit wachsenden Bedarf an Getriebelösungen hat sich das ursprünglich in der Uhrenindustrie beheimatete Unternehmen vom reinen Teilelieferanten zum Engineering- und Lösungsanbieter in der Automobilbranche entwickelt.
Reinhold Gnädinger, Manufacturing Manager bei IMS Gear: „Die Kernkompetenz unserer Business Unit ist ganz klar die Fertigung von präzisen, langlebigen Getriebekomponenten aus 2-3K Metall- und Kunststoffkomponenten.“ Durch das Umspritzen der metallischen Naben und Wellen mit einsatzoptimierten Kunststoffmaterialien können die jeweils spezifischen Werkstoffeigenschaften optimal genutzt werden, um auch hohe Drehmomente dauerhaft sicher und geräuscharm zu übertragen.
Apropos „geräuscharm“: Die Nabe des aus drei Komponenten bestehenden Schneckenrads für Lenkgetriebe wird parallel auf vier Sechsspindlern von der Stange, einem mikrolegierten AFP-Edelstahl mit einer Festigkeit von etwa 900 N/mm2, gefertigt. Im ersten Bearbeitungsschritt wird dabei der Innendurchmesser von 23,5 mm gebohrt, was bei einer Schnittgeschwindigkeit
von 130 m/min und hohem Materialabtrag bei sehr kurzer Eingriffszeit ein sehr unangenehmes, hochfrequentes Dauergeräusch mit sich bringt.
Der hohe Lärmpegel in der Halle wurde längst auch vom zuständigen Sicherheitsbeauftragten moniert, erzählt Burhan Kaya, Manufacturing Engineer bei IMS Gear, und fügt hinzu: „Das unglaublich große Spanvolumen beim Bohren führt zu einer extrem hohen Beanspruchung des Bohrerkörpers. Durch die hohe Festigkeit und den Spänedruck kam es durch Abrasion zu Auswaschungen in den Spankammern der damals eingesetzten Perfomax-Wendeplattenbohrer. In derFolge wurden die Bohrerkörper zunehmend instabiler, vibrierten und mussten häufig schon vorzeitig getauscht werden. Der Prozess war für uns nicht mehr zuverlässig planbar, die Kosten für die Ersatz-Körper zu hoch.“
Eine Rückkehr zu den früher eingesetzten Kronenbohrern stand jedoch schon aus Kostengründen nicht zur Debatte. Grundsätzlich waren die Leistungsdaten der Perfomax-Bohrer von Seco Tools mit einem Standweg von etwa 48 m und einer Standzeit von über 1.500 Teilen pro Schneide ja auch mehr als überzeugend. Die fortlaufende Optimierung bestehender Prozesse sei eine wesentliche Anforderung, die sich in der Automobilbranche stellt, erklärt Reinhold Gnädinger von IMS Gear. Als Teil der Produktentwicklung sorgt bei IMS Gear der Bereich „Industrial Engineering“ dafür, dass die Produktionsanlagen und Prozesse bei Neuanläufen komplett an die Produktionsbereiche übergeben werden. Im laufenden Großserienbetrieb müssen dann Prozessingenieure wie Burhan Kaya für die nötigen Verbesserungen sorgen. „Die bekannten Probleme Geräuschentwicklung und Standzeit der Bohrerkörper galt es zu lösen, also haben wir den gesamten Bohrprozess neu evaluiert. Die Werkzeugtechnik entwickelt sich schließlich stetig weiter, wir wollten sehen was
geht.“, begründet Burhan Kaya. Er initiierte, leitete und dokumentierte den Verbesserungsprozess und sprach fünf Werkzeughersteller dazu an.
Nun waren die Kritikpunkte von IMS Gear an dem eingesetzten Perfomax-Bohrerkörper von den betreuenden Außendienstmitarbeitern und Anwendungstechnikern längst an die Produktentwicklung in der Konzernzentrale in Schweden weitergegeben worden. Für diese ist ein anspruchsvoller User-Case ebenso wichtig und wertvoll wie das direkte Feedback von der Front. Denn wenngleich es sich im Labor herrlich bequem testen lässt, und hier unterscheidet sich Seco nach Firmenangaben klar von vielen anderen Werkzeugherstellern, gehen neue Produkte nur nach aussagekräftigen Praxistests in den Markt. Perfekt war, dass zu Beginn des neuen Benchmarks bei IMS Gear das Seco-Team bereits an der Neuentwicklung der seit vielen Jahren erfolgreichen und mehrfach weiterentwickelten Perfomax-
Serie arbeitete. Für das anspruchsvolle Design der neuen, sehr stabilen Perfomax-Bohrer wurde in Schweden damals gerade eine zusätzliche Fertigungslinie aufgebaut. Auf drei hintereinandergeschalteten Bearbeitungszentren werden die jetzt aus fertig-vergütetem Material bestehenden Bohrerkörper an den Spanräumen und am Außendurchmesser mit einer wellenartigen Oberflächenstruktur versehen. Der Kontaktbereich des Spans in der Spankammer wird nachfolgend auf 65 HRC lasergehärtet. Ebenfalls überarbeitet wurde das Design des Plattensitzes, der jetzt eine größere Kontaktfläche zur Wendeplatte gewährleistet.
Neben einem stabilen Bohrerkörper ist die hohe Qualität des Schneidstoffes ausschlaggebend für sichere Spankontrolle und hohe Standzeiten. Die für die Aufgabenstellung bei IMS Gear passende DP3000 Wendeplatte für die Zentrums- und Peripherieschneide verfügt über eine patentierte Duratomic-Beschichtung. Diese zeichnet sich durch geordnete Kristallstrukturen und eine damit glatte Oberfläche aus: Besonders hohe Wärmebeständigkeit und Kantenstabilität sind das Ergebnis. Bei IMS Gear in Donaueschingen traten nacheinander vier Wettbewerber an. Burhan Kaya blickt zurück: „Wir haben dabei strengstens darauf geachtet, dass jeder Werkzeughersteller exakt die gleichen Grundvoraussetzungen bekommt.“ Über einen Zeitraum Index MS 42C mit den Haltern und Wendeschneidplatten der jeweiligen Anbieter bestückt, die erzielten Standzeiten, der Verschleiß der Bohrerkörper und die Geräuschentwicklung sauber dokumentiert.
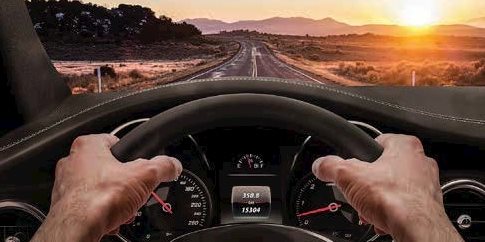
„Mit einem geplanten Ausstoß von über 120.000 Stück pro Woche bietet die Schneckenradnabe natürlich eine optimale Datenbasis für eine absolut faire Bewertung der einzelnen Bohrwerkzeuge“, berichtet Burhan Kaya. Die Testergebnisse hätten eine klare Sprache gesprochen: Bei den Kandidaten, die mit niedrigem Bearbeitungsgeräusch glänzten, seien die Standzeiten mit fünf- bis sechshundert Teilen pro Schneide weit hinter den geforderten 1.500 Stück gelegen. Die anderen Werkzeuganbieter kamen beinahe an die Standzeit heran, fielen jedoch beim Geräuschpegel oder der Lebensdauer der Bohrerkörper durch. Besonders geschätzt hat man bei IMS Gear die sehr offene und partnerschaftliche Zusammenarbeit mit Seco Tools und den Ergebnissen der neuen Perfomax-Generation, für die die Entwickler von Seco Tools aus Schweden anreisten. Nach ersten Testresultaten mit vier Prototypen wurde die Position des lasergehärteten Kontaktpunkts in den Spankammern des neuen Perfomax nach hinten verschoben. Der Aufwand, so Burhan Kaya, habe sich für beide Seiten mehr als gelohnt. Mit dem neuen Material und Design des Perfomax-Grundkörpers, der wellenförmigen Oberfläche der Spankammern und der lasergehärteten Span-Kontaktfläche hätten sich die Kritikpunkte an der Vorgängerversion ebenso in Luft aufgelöst wie der Lärm in der Fertigungshalle. Die hinzugewonnene Stabilität des Perfomax reduziert Vibrationen und sorgt dadurch für ein deutliches Plus an Laufruhe. Seit bei IMS Gear die neue, optimierte Perfomax-Generation eingesetzt wird, konnte der Verbrauch an Wendeplattenträgern
denn auch mehr als halbiert werden. Die erwartete Lebensdauer von 100.000 Bohrungen pro Träger werde übertroffen, bestätigt Burhan Kaya und Manufacturing Manager Reinhold Gnädinger ergänzt: „Die Sicherheit im Bearbeitungsprozess ist wieder vollauf gegeben, der Faktor Werkzeugkosten passt und die Kapazität ist zuverlässig planbar.“ Die Zusammenarbeit mit Seco Tools bewerten die Fertigungsexperten von IMS Gear dabei äußerst positiv.
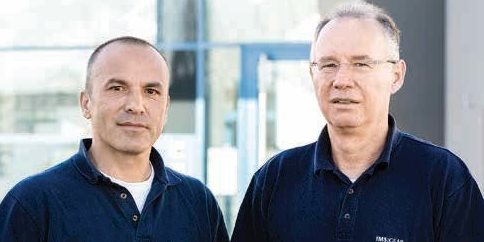
Und Gnädinger weiß auch: „Genau wie IMS Gear als Partner der Automotive-Branche muss ein Werkzeughersteller wie Seco Tools stetig optimieren und seine Produkte weiterentwickeln. Der aktuelle Benchmark zeigt, wie vorteilhaft eine Zusammenarbeit auf Augenhöhe für beide Seiten sein kann.“ IMS Gear profitiert dabei nicht nur von den Vorteilen der neuen Perfomax-Bohrerserie. Bei diesem Verbesserungsprozess wurde nebenbei auch gemeinsam der Prozess des Einstichs an der Nabe des Schneckenrades optimiert, der IMS Gear und Seco aufgefallen war. Durch den Einsatz des X4 Stechsystems kombiniert mit der neuen Wendeplattensorte TGH von Seco Tools konnte die Standmenge im Vergleich zum Wettbewerbswerkzeug verdoppelt und die Prozesssicherheit bei dem eng tolerierten Einstich wesentlich verbessert werden.