Che cos'è il power skiving?
Il power skiving migliora la flessibilità e produttività nella lavorazione di dentature ingranaggi o scanalatiLo Skiving è una tecnica di lavorazione per la produzione degli ingranaggi, che con una soluzione dedicata è applicabile sia su dentatura interne che esterne. Lo skiving consente la finitura del profilo del dente degli ingranaggi, e oggi è eseguibile non solo con dentatrici a CNC di ultima generazione ma anche con macchine multi-task o centri di lavoro moderni.
Non si può dire che il Power Skiving sia un metodo costruttivo nuovo, dato che il primo brevetto sullo skiving venne depositato in Germania nel 1910. Per quasi un secolo questo metodo non si è diffuso a causa dei limiti tecnologici sia in termini di software che di hardware, che non consentivano affidabilità, precisione e velocità tali da renderlo conveniente e produttivo.
Per farsi un’idea approssimativa del principio di funzionamento dello skiving, si può immaginare di combinare la dentatura con creatore alla stozzatura con coltello circolare. Si può associare la dentatura skiving a una lavorazione con un creatore a più principi, estremizzando il numero di principi del creatore, così che a ogni principio corrisponda un dente di taglio, si otterrà un utensile di skiving.
Diversamente dalla lavorazione con creatore, la lavorazione con skiving crea una distribuzione irregolare dei trucioli con un angolo di spoglia negativo all’uscita della punta dell’utensile. Per questo motivo nello skiving è necessario un approccio a più passate.
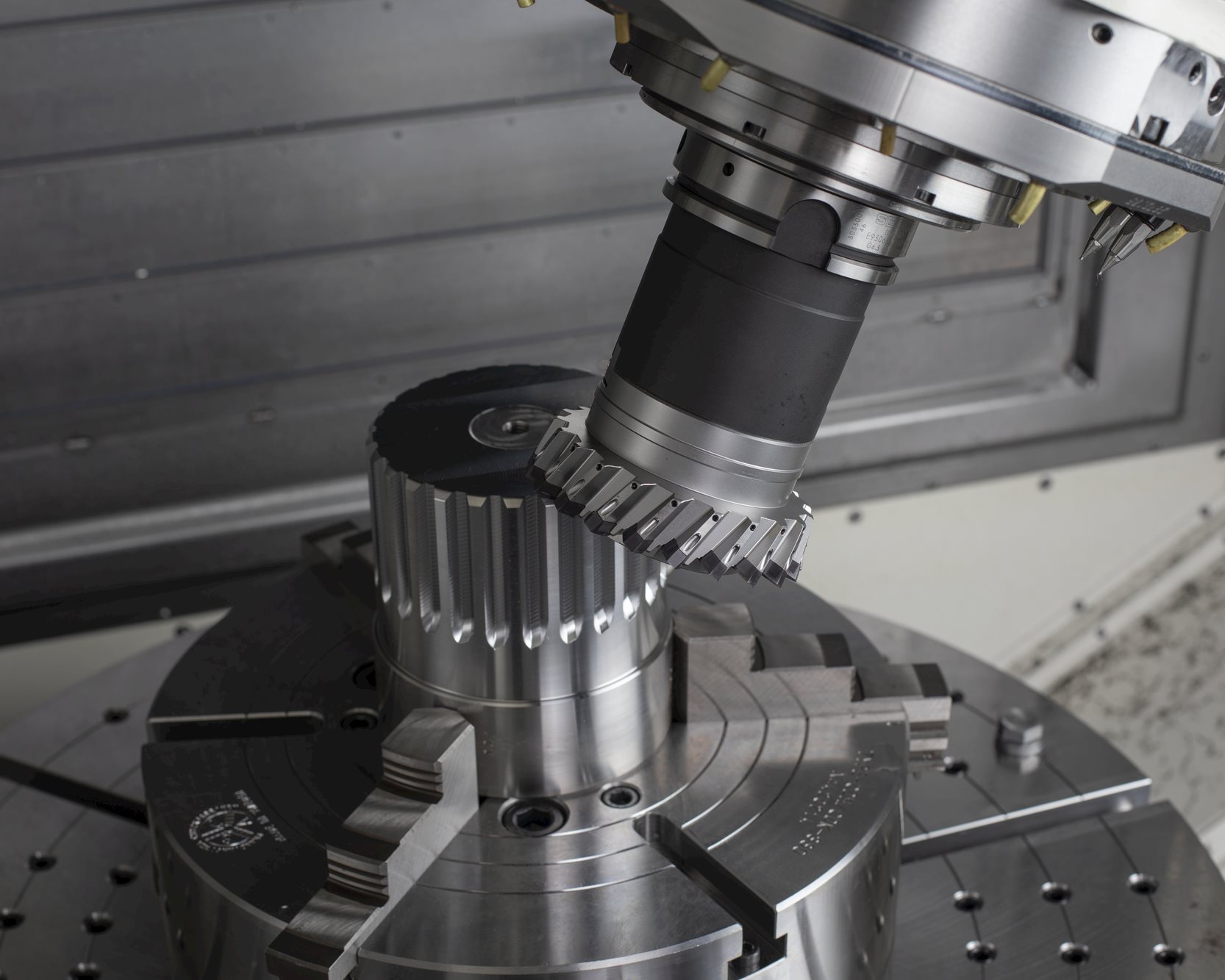
Grazie alla recente evoluzione tecnologica delle macchine utensili, dei software e della stessa utensileria, oggi lo skiving è un’opzione rapida, efficiente e flessibile per la produzione di ingranaggi.
Questa tecnologia consente di lavorare l'ingranaggio in tutte le sue fasi su un'unica macchina multi-task o centro di lavoro con un solo piazzamento. Elimina quindi la necessità di dotarsi di più macchine dedicate, evitando gli errori di setup derivanti dal passaggio tra una macchina e la successiva, azzerando quasi completamente gli errori di run-out radiale.
Questo approccio permette di ridurre notevolmente il tempo di produzione totale rispetto a quei processi che includono operazioni di brocciatura, profilatura o dentatura a creatore, assicurando una lavorazione affidabile e ripetibile degli ingranaggi.
La precisione nella sincronizzazione tra mandrino-pezzo e mandrino-utensile oggi possibile anche a elevate velocità di taglio garantisce elevate prestazioni mantenendo la qualità.
Nel power skiving ogni tagliente dell’utensile lavorerà un dente dell'ingranaggio e in un processo di taglio continuo, rappresentando così un’alternativa molto efficiente rispetto alla dentatura a coltello circolare, persino anche rispetto alla brocciatura.
La produttività e versatilità di questo metodo lo rendono adatto alla produzione sia di pezzi singoli sia di lotti di media grandezza.
Lo skiving è imprescindibile soprattutto quando si affrontano dentature di piccole dimensioni o con ingombri che impedirebbero l’impiego di mole di rettifica. In questi casi, lo spazio di uscita utensile risulterebbe eccessivo, e ciò andrebbe ad intaccare spallamenti o parti che a disegno non devono essere toccate. Al contrario, grazie al ridotto ingombro degli utensili skiving si evitano molti dei comuni inconvenienti presenti in altri processi di lavorazione.
La soluzione innovativa a inserti in metallo duro eliminerà la necessità di riaffilare gli utensili, cosa che invece è indispensabile quando si usano utensili tradizionali integrali. Questo significa che l’officina non sarà più costretta a tenere a stock utensili gemelli, ottimizzando il magazzino utensili.
La novità della soluzione con testine intercambiabili in metallo duro dello skiving, consente oltre alla possibilità di riaffilarle fino a quattro volte, di conservare il codolo e cambiare solo la testina a fine vita.
- Lavorazione di un componente completo in un unico piazzamento
- Riduzione delle fasi di lavorazione
- Diminuzione dei fermi
- Riduzione del tempo di produzione
- Aumento delle prestazioni e di produttività
- Migliore qualità e prevedibilità
- Riduzione dei costi
- Durata e convenienza
- Eliminazione delle riaffilature con la soluzione a inserti
- Possibilità di lavorare in presenza di spallamenti
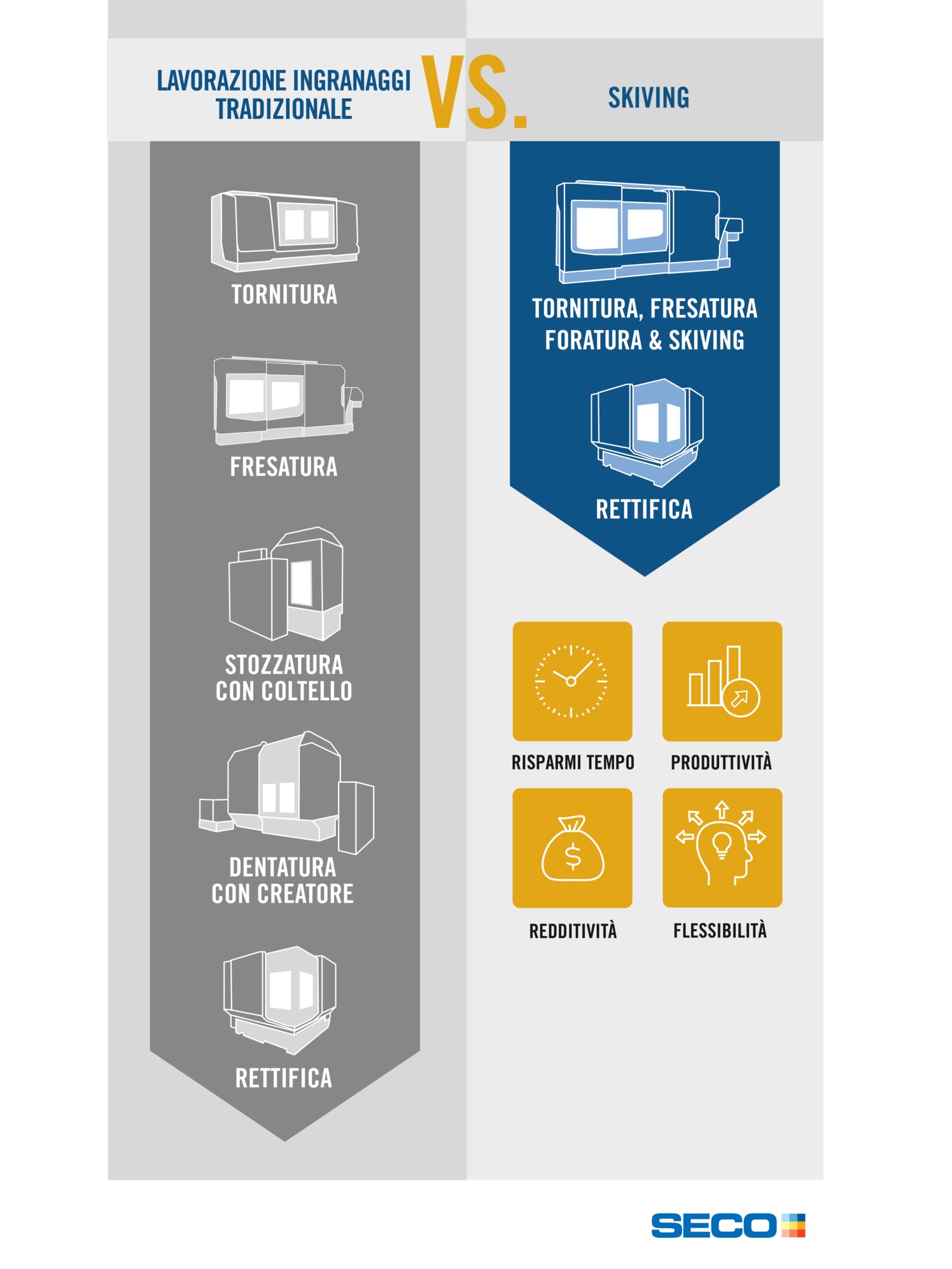