다이나믹 밀링 - 최적화된 툴 패스로 더 빠른 가공
CAM 을 통한 공구 경로를 최적화는 일반적인 추세가 되었습니다. 지난 10년 간 공장들은 새로운 가공 전략과 특별히 설계된 밀링 공구로 황삭 가공을 최적화 하기 시작하였습니다. 이렇게 시간과 비용을 절약하는 가공 전략을 다이나믹 밀링(또는 어드밴스드 러핑)이라고 부릅니다. 다이나믹 밀링(또는 CAM 기반 황삭) 전략은 절삭 공구의 접촉 호(arc)와 평균 칩 부하가 중심이 되는 전략입니다. CAM 에서 생성한 툴 패스를 통해 공구의 접촉 호를 조정하여 황삭 속도를 높이고, 공정 온도를 효과적으로 제어하며, 날 당 이송을 더 키우고, 절삭 깊이도 늘려 전체 부품 가공 사이클 타임을 대폭 단축하면서도 공작기계의 스핀들(축)에 추가적인 부담을 주지도 않습니다.CAM 을 통한 공구 경로를 최적화는 일반적인 추세가 되었습니다. 지난 10년 간 공장들은 새로운 가공 전략과 특별히 설계된 밀링 공구로 황삭 가공을 최적화 하기 시작하였습니다. 이렇게 시간과 비용을 절약하는 가공 전략을 다이나믹 밀링(또는 어드밴스드 러핑)이라고 부릅니다.
다이나믹 밀링(또는 CAM 기반 황삭) 전략은 절삭 공구의 접촉 호(arc)와 평균 칩 부하가 중심이 되는 전략입니다. CAM 에서 생성한 툴 패스를 통해 공구의 접촉 호를 조정하여 황삭 속도를 높이고, 공정 온도를 효과적으로 제어하며, 날 당 이송을 더 키우고, 절삭 깊이도 늘려 전체 부품 가공 사이클 타임을 대폭 단축하면서도 공작기계의 스핀들(축)에 추가적인 부담을 주지도 않습니다.
다이나믹 밀링 E-Book 읽기
절삭 공구의 접촉 호(arc of contact)는 공구의 열 부하에 영향을 미치는 독립 변수이며 다이나믹 밀링(최적화된 황삭) 작업의 핵심입니다.
모든 공구에서 접촉 호의 최대 크기는 180도(직경)입니다. 다시 말해, 공구의 호가 공작물에 최대로 접촉할 때, 반경 방향 절삭 깊이 (또는 절삭 폭)은 커터의 직경과 동일합니다. (Ae 절삭 폭 = DC 커터 직경)
공장은 접촉 호의 크기를 조정하여, 황삭 작업 중에 발생하는 열의 양을 줄일 수 있습니다. 반경 방향 절삭 깊이(Ae)를 줄이면 커터의 접촉 호(arc)의 크기도 줄어듭니다. 접촉량이 작아질 수록 접촉 시간도 줄어들어 공작물과 절삭 인선간에 열도 적게 발생합니다. 그와 동시에 공구의 절삭 인선이 공작물에서 빠져나오면서 냉각하는 시간은 더 많아집니다. 이렇게 가공 온도가 낮아질수록, 절삭 속도는 높일 수 있고 사이클 타임은 더 줄일 수 있게 됩니다.
절삭 공구의 평균 칩 두께(hm)는 물리적 부하에 기반하며 날 당 이송(fz)과 접촉 호의 조합으로 구성됩니다. 칩 두께는 절삭 중에 계속 변화하기 때문에, 절삭 가공 업계에서는 평균 칩 두께(hm)라는 용어를 사용합니다.
커터의 직경 전체를 공작물과 접촉시킬 때 접점은 180도의 호(arc)를 이루며 커터 폭의 가운데 지점에서 가장 두꺼운 칩이 생성됩니다. 따라서 접촉각(ⱷe, 진입 각도)이 90도 보다 작은 경우, 즉 절삭 폭이 커터 직경의 절반에 미치지 못하는 경우 칩 두께는 얇아지고 그 대신 날 당 이송(fz)을 보정하여 높일 수 있습니다.
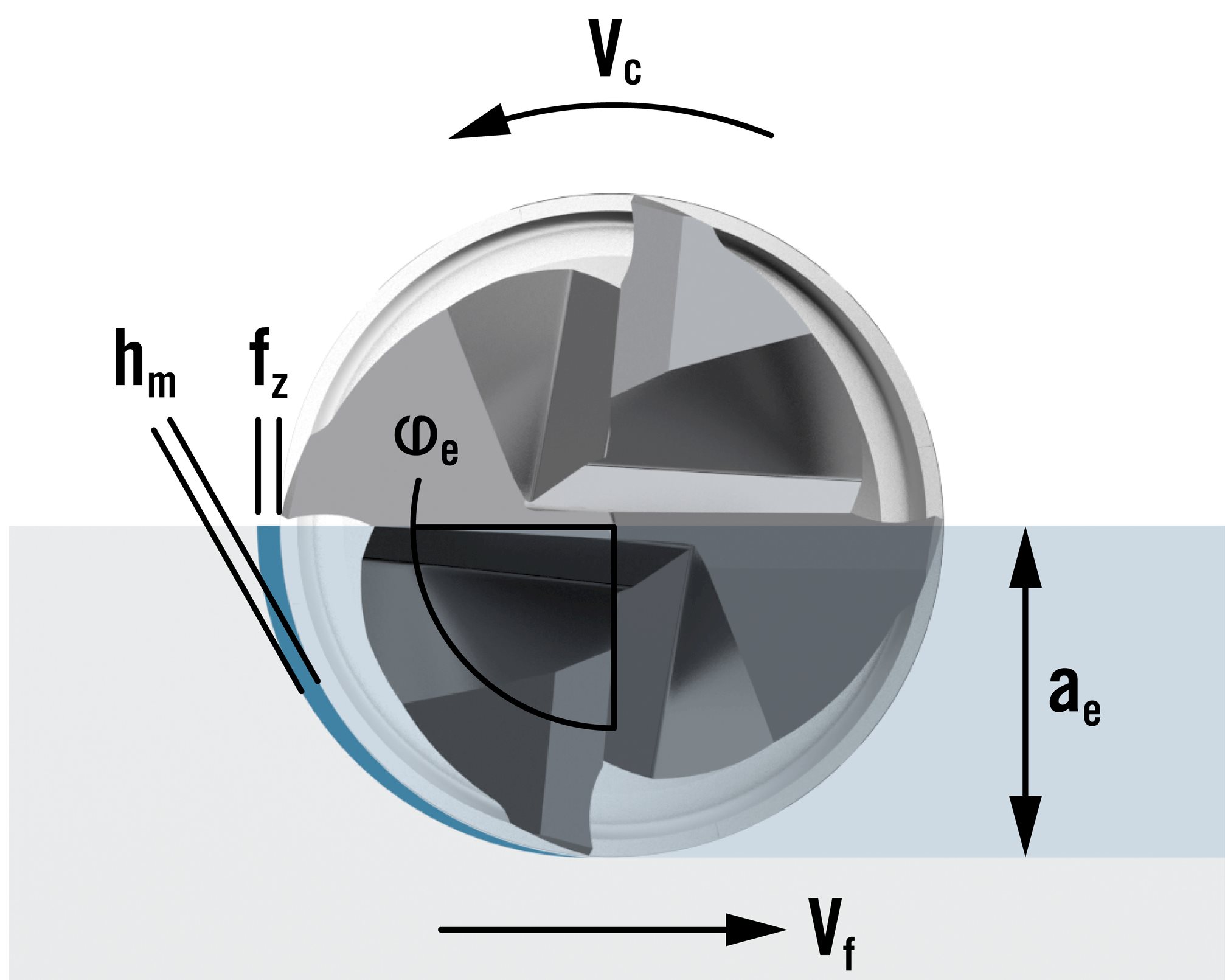
Φ10mm 엔드밀의 전체 폭을 활용하여 가공하는 슬롯 밀링(홈 가공)을 예로 들면, 커터 폭의 가운데인 5mm 지점에서 커터가 생성하는 칩 두께와 물리적 부하는 최대가 됩니다.
앞의 90도 구간에서 커터는 최대 칩 두께(=날 당 이송fz)에 도달할 때까지 상향 밀링(업밀링)을 하고, 그 뒤의 90도 구간에서는 칩 두께가 다시 0으로 감소하며 하향 밀링(다운밀링)을 하게 됩니다.
절삭 폭(ae, 또는 접촉 폭)이 직경DC의 50% 미만으로 작아지면, 예를 들어 Φ10 mm 엔드밀에서 1mm 만 접촉 시키는 경우, 평균 칩 두께는 작아지며, 그에 따라 날 당 이송(fz)을 높일 수 있어 황삭 가공을 더 빠르게 할 수 있습니다. 커터가 한 번에 제거하는 소재량은 적어지지만, 더 빠르게 가공할 수 있습니다.
또한 반경 방향 절삭 깊이가 큰 경우보다 공구와 공작 기계 스핀들에 가해지는 부담이 적습니다. 다이나믹 밀링에서 절삭 폭Ae 이 작아질수록 최대 절삭 가능 깊이APMX가 커지기 때문에 더 빠른 소재 제거가 가능해집니다.
대부분의 절삭 공구 제조사는 세코 툴스처럼 각 소재에 맞는 각각의 공구를 제공하지만 다이나믹 밀링용 형상도 개발합니다. CAM 기반 황삭(다이나믹 밀링)의 툴링에서는 공구의 플루트 및 길이에 대한 요구 사항과 함께 칩 제어 문제를 해결하는 것이 핵심[JG1] 입니다.
세코의 Jabro® HPM (고성능 가공) 엔드밀 시리즈는 황삭 가공에서 최대한 많은 양을 한 번에 가공할 수 있도록 엔드밀의 폭 전체를 접촉시키고 절삭 깊이 가능한 깊게 적용할 수 있게 설계되었습니다. 이 HPM 엔드밀 시리즈는 높은 성능을 낼 수 있는 특수 형상이 특징입니다.
다양한 공작물 소재를 커버하기 위하여 세코는 Jabro®-Solid² 500 엔드밀 시리즈를 개발하였고, JSE560 엔드밀 시리즈는 모든 소재에서 다이나믹 밀링을 적용할 수 있도록 개발되었습니다. JS560 엔드밀 시리즈는 안정성을 더욱 보강하고 공구의 휨을 줄였습니다.
깊은 포켓과 3D 형상의 다이나믹 밀링에서, 공구 인선(날)의 길이는 일반적으로 직경의 3~4배 입니다. 특히 스테인리스 강, 티타늄 합금 등 난삭재의 수요가 증가하고 있기 때문에, 세코 툴스는 다이나믹 밀링용 멀티 플루트(다날) 엔드밀 시리즈인 JS720을 개발하였습니다. JS720 엔드밀 시리즈는 CAM 을 최대한 활용하며 공작기계의 잠재력을 활용하는 동시에 안전한 다이나믹 밀링 공적을 보장하는 훌륭한 선택입니다.
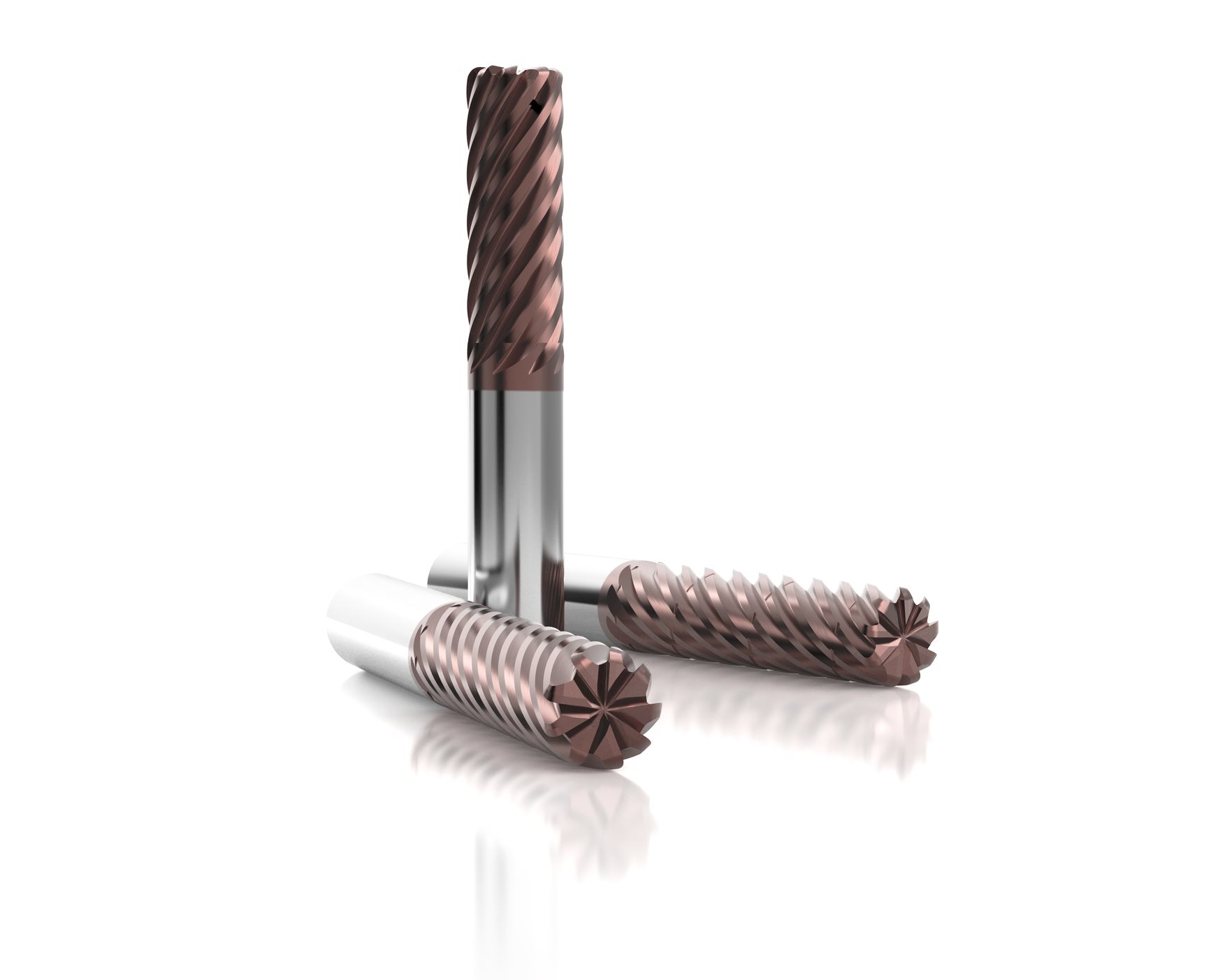
솔리드 초경 엔드밀
접촉 호(arc)를 일관성 있게 유지하면, 엔드밀은 일반적으로 각 날에 마모를 고르게 분산시킵니다. 결과적으로 공구의 수명이 일관적이기 때문에 예측이 가능해집니다. 하지만 엔드밀이 길어질 수록 칩 또한 길어지기 때문에 절삭 지점과 장비에서 칩을 배출하기 어려워집니다.
칩을 더 작고 관리하기 쉽게 생성할 수 있도록, 세코의 범용 다이나믹 밀링 엔드밀인 JS564 와 ISO M&S 스테인리스 강, 티타늄 및 초합금용 다이나믹 밀링 엔드밀인 JS720 시리즈는 칩을 작게 부수는 칩 스플리터 기능이 있습니다. 칩 스플리터는 엔드밀의 절삭인선(절삭날)에 1 x DC (엔드밀 직경)간격으로 나 있는 홈입니다. 따라서 날장 40mm 길이의 Φ10mm 엔드밀은 절삭 지점에서 길이 10mm 이하의 짧은 칩을 생성하고 공작기계 칩 컨베이어 벨트에 끼일 위험성을 해소합니다.
접촉 호의 크기가 작고 날 수(플루트)가 더 많을 수록 분 당 이송Vf(테이블 이송)을 더 많이 줄 수 있고 생산성이 높아집니다. 분 당 이송Vf(테이블 이송) = 날 수(ZEFP 또는 z) x 날 당 이송(Fz) x RPM 입니다. 시중의 황삭 엔드밀은 일반적으로 4날이지만, 세코 툴스의 엔드밀은 4날, 5날 및 그 이상의 다날 형상으로 구성됩니다. 공정이 잘 제어되고 반경 방향 절입 폭(Ae)을 작게 적용하면, 날 수가 많은 다날(멀티플루트) 엔드밀이 효율을 엄청나게 향상시킵니다.
직선 가공 경로(사이드 밀링)에서는 접촉 호(arc) 크기가 변경되지 않고 일정하게 유지됩니다. 그러나 내측 R 및 외측 R 등 복잡한 형상을 가공하는 경우, 접촉 호의 크기가 일관적이지 않게 됩니다.
커터가 직선 절삭을 완료하고 내부의 R, 또는 모서리에 진입하면 접촉 호의 크기가 증가하기 때문에 실제 절삭 조건이 더 이상 현재 접촉 호와 일치하지 않게 됩니다. 이러한 상황에 맞게 툴패스를 조정하지 않으면 채터링, 진동 및 커터 파손이 발생합니다.
오늘날의 CAM 패키지는 기존의 공구 경로에서 접촉 호 크기의 변경을 유발하는 내/외부 R 형상을 위한 툴패스 기능을 제공합니다. CAM 프로그램 패키지는 접촉 호를 제어하고 칩 부하를 일관되게 유지하도록 자동으로 이송을 조정합니다. 접촉 호를 일정하게 유지할 수 있도록 CAM 프로그램이 반경(R)이나 더 좁은 부분을 가공할 때 트로코이드 밀링이나 필 밀링 기법을 적용합니다. 툴패스를 구성한 이후, CAM 프로그램 패키지는 L 이동을 대폭 줄여 사이클 타임을 단축시킵니다.
다이나믹 밀링 툴 패스를 사용하고 접촉 호의 크기를 일관되게 유지한다면, 내부 반경(R) 가공시 커터의 과부하, 당김, 과삭 등의 위험을 없앨 수 있습니다. 이 기능으로 공장은 황삭 가공 공정에서 더 많은 양을 가공하여 정삭 툴 패스가 가공해야 할 양을 줄여주므로 이 또한 사이클 타임 단축에 일조합니다.
다이나믹 밀링 전략은 다양한 소재에 적용할 수 있습니다. 세코 툴스는 강, 스테인레스 강, 주철, 티타늄, 알루미늄 및 최대 HRc 48 의 경화강에 광범위한 테스트를 수행하였습니다. 세코 툴스는 세코 소재 분류(SMG) 기준 P1, P2, P3, P4, M2, K2 (S25C, S45C, SUS316, 컴팩트 흑연 주철)에 해당하는 일반적인 소재에서는 일반적으로 공구 직경의 10~15% 를 최대 절삭 폭(AEMX)으로 권장합니다.
그리고 세코 소재 분류(SMG) 기준 S2, S12, M4, P12, H7 (스텔라이트, TiAl6V4를 비롯한 중합금 티타늄, SUS329J1 등 고합금 오스테나이트 및 듀플렉스 스테인리스 강, SUS 600 계열, PH 계열, 그리고 HRc 48 이상의 경화강) 을 비롯한 가공하기 다소 어려운 소재에는 공구 직경의 5% 를 최대 절삭 폭(AEMX)으로 권장하며, 세코 툴스 홈페이지인 www.secotools.com 에서 정확한 권장 절삭 조건을 알려드립니다. 현장에서는 권장보다 더 많은 양의 절삭 폭(Ae)을 적용 할 수 있지만, 그에 맞추어 날 당 이송(Fz)나 절삭 속도(Vc)를 줄여야 합니다.
소형 장비에서는 일반적으로 고부하 황삭 가공을 수행하기 어렵기 때문에, 접촉 호의 크기를 줄이고 트로코이드 밀링 툴 패스를 적용합니다. 이렇게 함으로서 절삭 부하를 줄이고 낮은 동력으로도 가공하면서도, 절삭 깊이를 크게 적용하여 높은 생산성을 유지할 수 있습니다. 이렇게 하면 대규모의 투자 비용을 잠재적으로 절약할 수 있으며 기존의 장비로 황삭 가공을 할 수 있습니다.
스테인레스 강 및 티타늄을 비롯한 난삭재에서 황삭 전략을 사용할 때는 절삭유를 고르게 분사하여 공구 날(인선)의 상단, 중단, 하단에 모두 닿도록 해야 합니다. 절삭 인선을 완벽하게 냉각하는 것이 중요합니다. 강과 주철을 밀링 가공 할 때는, 칩을 날려 버릴 수 있도록 최대 압력으로 압축 공기를 분사하는 것이 좋습니다.
다이나믹 밀링의 툴패스는 장비 밖에서 생성되고 머신 컨트롤러 안에서 작성하는 것은 거의 불가능합니다. 종종 CAM 프로그램 업체는 추가 기능이나 모듈로 공구 경로 최적화 기능을 제공합니다. 장비에서 프로그래밍할 때 세코가 권장하는 접촉 호 크기를 수동 프로그래밍으로 적용시킬 수 있지만, 그것은 단순한 직선 가공이나 수정 트로코이드 사이클 정도의 수준만 가능합니다.
자동차 산업의 고객들은 자동차 부품 가공에서 다이나믹 밀링 전략과 툴패스의 이점을 경험했습니다. 전체 부품 사이클 타임을 8.5분에서 1.1분으로 단축했을 뿐만 아니라 공구 수명이 엔드밀 한 개당 부품 80개에서 250개로 늘어났습니다.
접촉 호(arc) 및 평균 칩 두께는 다이나믹 밀링의 핵심 요소입니다. 오늘날의 제조사들은 툴 패스 최적화와 다이나믹 밀링을 위한 CAM 소프트웨어 패키지를 활용하여 절삭 공구의 접촉 호의 크기를 제어하며, 부하를 일정하게 유지합니다. 이를 통해 공정의 온도를 효과적으로 제어하고, 높은 절삭 속도와 날 당 이송을 적용하며, 더 깊은 절삭 깊이로 전체 부품 가공 사이클 타임을 대폭 단축합니다.
그러나 제조업체는 다이나믹 밀링 프로그래밍에 적합한 CAM 소프트웨어 패키지가 필요하다는 점을 명심해야 합니다. 대부분의 절삭 공구 제조사는 각 소재에 맞는 공구를 제공하기는 하지만 특정한 고급 가공 방법과 툴 패스에 대한 공구 형상을 제공하는 경우는 드뭅니다. 올바른 커터와 다이나믹 밀링 사이클을 통해 제조업체는 금속 제거 속도(생산 속도)를 전통적인 가공 방법 대비 500% 까지 높일 수 있습니다.
다이나믹 밀링 E-Book 읽기