DYNAMISK FRÄSNING - SNABBARE MED OPTIMERADE VERKTYGSBANOR
CAM-system med optimerade verktygsbanor, har länge varit vanligt förekommande. Under de senaste 10 åren har verkstäder börjat förena metoden med relativt nya bearbetningsstrategier och specialkonstruerade fräsverktyg för att optimera grovbearbetningen. Dynamisk fräsning eller avancerad grovbearbetning är den vanliga beskrivningen av dessa tids- och kostnadseffektiva bearbetningsstrategierna. Dynamisk fräsning är en typ av valsfräsning med konstant ingreppsvinkel och där hela skärkantslängden på verktyget används. Med metoden undviks fullspårsfräsning vilket minskar oönskad värmeutveckling och risken för verktygsbrott. Friktionen minskar och då minskar även värmeutvecklingen mellan skäregg och detalj. Lägre bearbetningstemperatur gör att skärhastigheten kan ökas och cykeltiderna kan förkortas.CAM-system med optimerade verktygsbanor, har länge varit vanligt förekommande. Under de senaste 10 åren har verkstäder börjat förena metoden med relativt nya bearbetningsstrategier och specialkonstruerade fräsverktyg för att optimera grovbearbetningen. Dynamisk fräsning eller avancerad grovbearbetning är den vanliga beskrivningen av dessa tids- och kostnadseffektiva bearbetningsstrategierna.
Dynamisk fräsning är en typ av valsfräsning med konstant ingreppsvinkel och där hela skärkantslängden på verktyget används. Med metoden undviks fullspårsfräsning vilket minskar oönskad värmeutveckling och risken för verktygsbrott. Friktionen minskar och då minskar även värmeutvecklingen mellan skäregg och detalj. Lägre bearbetningstemperatur gör att skärhastigheten kan ökas och cykeltiderna kan förkortas.
READ AND DOWNLOAD OUR DYNAMIC MILLING E-BOOK FOR FREE
Ingreppsvinkeln påverkar den termiska belastningen på verktyget och är nyckeln till optimerade grovbearbetningsoperationer.
Max ingreppsvinkel på ett verktyg är 180 grader (dess diameter). Vid fullt ingrepp är skärdjupet (eller skärbredd) samma som fräsdiametern och utgörs av ae (radiellt skärdjup) = Dc (fräsdiameter).
Med metoden undviks fullspårsfräsning vilket minskar oönskad värmeutveckling under bearbetningen. När det radiella skärdjupet minskar, så minskar även den konstanta ingreppsvinkeln på fräsen. Detta gör att ingreppstiden minskar och då minskar även värmeutvecklingen mellan skäregg och detalj. Det som sker är att skäreggarna hinner svalna innan de går i ingrepp igen. Lägre bearbetningstemperatur gör att skärhastigheten kan ökas och cykeltiderna kan förkortas.
Ett skärverktygs medelspåntjocklek (hm) baseras på materialbelastning och bibehålls genom en kombination av matning per tand och ingreppsvinkel. Eftersom spåntjockleken ständigt ändras under ingrepp används termen medelspåntjocklek (hm).
180-graders ingreppsvinkel kommer att generera de tjockaste spånen i mitten av fräsbredden. En mindre ingreppsvinkel – mindre än 90 grader (ⱷe, ingreppsvinkel) – minskar spåntjockleken och tillåter högre matning per tand (fz).
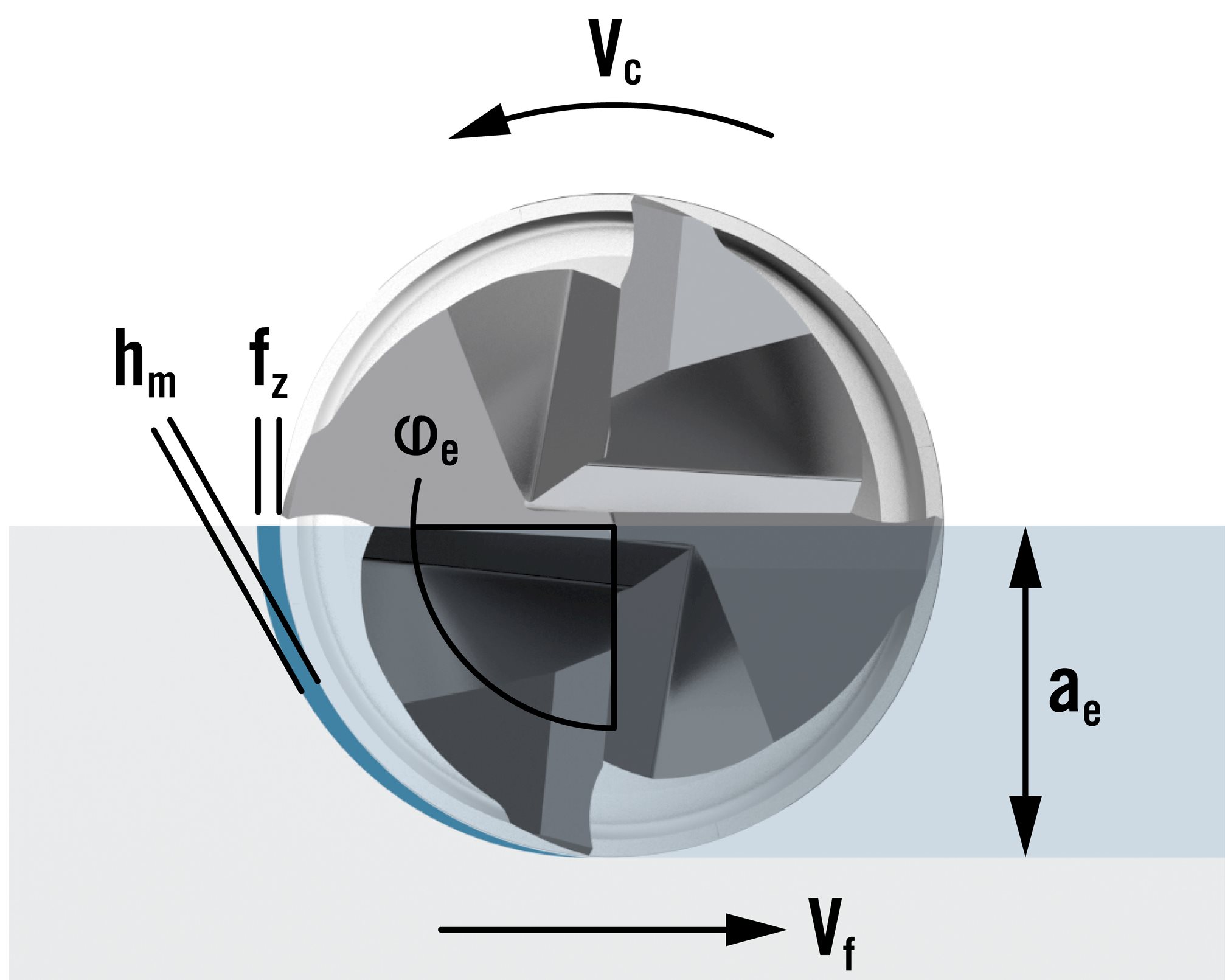
Till exempel, med en 10 mm diameter spårfräs (full ingreppsvinkel), vid 50% ingrepp (5 mm), genererar fräsen den största medelspåntjockleken och den högsta materialbelastningen.
De första 90 graderna används medfräsning tills den maximala spåntjockleken (fz) uppnås och fortsätter med motfräsning de andra 90 graderna där spåntjockleken minskar igen till 0.
Om ae minskar (ae)< 0,5xDc) to, for example, 1 mm (10 percent), then average chip thickness will become smaller, allowing for faster roughing by applying increased feed per tooth (fz). While the cutter removes less material, it does so at a much faster pace.
Dessutom blir belastningen på verktyg och spindel mindre jämfört med större radiella ingrepp vid lägre matningshastigheter. Vid dynamiska grovfräsning tillåter ett lägre AEMX (radiellt skärdjup) också ett större APMX (axiellt skärdjup) för ännu snabbare materialavverkning.
Medan de flesta leverantörer av skärande verktyg erbjuder verktyg utformade för specifika material, utvecklar Seco Tools och andra också verktygsgeometrier för avancerade bearbetningsmetoder. När det gäller CAM-baserade grovbearbetningsstrategier finns verktyg för spånkontroll och krav på spirallängder.
Jabro®-HPM (High performance machining) fräsar är speciellt utformade för grovbearbetning med full ingreppsvinkel och för stora skärdjup och hög materialavverkning. Fräsarna har speciella geometrier för hög prestanda i specifika material.
För att täcka ett bredare område av arbetsmaterial har Seco utvecklat geometrierna på Jabro®-Solid² 500-programmet, och JSE560-programmet har utvecklats specifikt för att optimera grovbearbetning, men fräsarna kan även användas i normala arbetsmaterial. JS560-fräsarna är extra stabila vilket gör att verktygsutböjningen minskar, samtidigt som säker materialavverkning garanteras.
För avancerad grovbearbetning/dynamisk fräsning av djupa kaviteter och 3D är verktygslängderna vanligtvis mellan tre och fyra gånger diametern. Eftersom efterfrågan blir allt större, speciellt i mer svårbearbetade material som rostfritt stål och titanlegeringar, har Seco även utvecklat JS720 för avancerad grovbearbetning. Detta verktyg är lämpligt för att utnyttja hela CAM- och bearbetningspotentialen samtidigt som det garanterar en säker bearbetningsprocess.
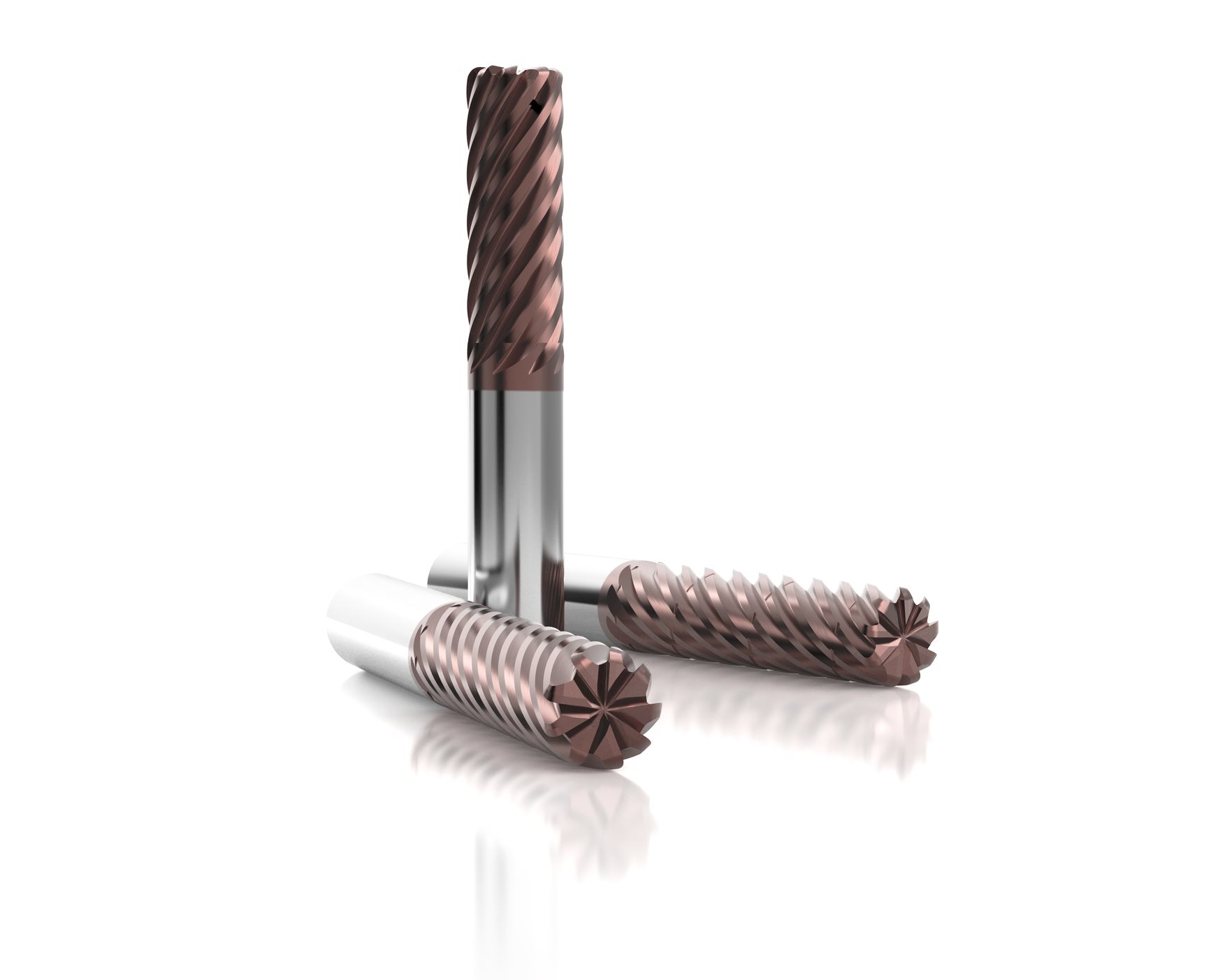
När konstant ingreppsvinkel bibehålls, ger det en jämnare förslitning på spiralerna. Det resulterar i en mer förutsägbar verktygslivslängd. Långa pinnfräsar ger lika långa spån som kan vara svåra att evakuera från skärzonen och verktyget.
För att generera spån som är mindre och mer hanterbara, har både Secos JS564 för dynamisk fräsning och JS720 för ISO M&S material konstruerats med spåndelare. De har små spår på skäreggen och släppningen. Spåren har ett avstånd lika med 1 X DC (skärdiameter). En 40 mm lång pinnfräs med 10 mm diameter, ger således spån som inte är längre än 10 mm, de evakueras snabbt från skärzonen och minskar risken för spåntrassel.
Liten ingreppsvinkel och fler antal spiraler gör att matningen och produktiviteten kan ökas. Matningshastighet = antal spiraler x matning per tand x spindelhastighet. Även om pinnfräsar för grovfräsning vanligtvis har fyra spiraler, kan Seco erbjuda 4-, 5- och flerskäriga geometrier. När processen är kontrollerad och bearbetningen tillåter relativt små radiella skärdjup, kan flerskäriga pinnfräsar öka effektiviteten avsevärt.
Vid raka verktygsbanor (sidofräsning), blir den inställda ingreppsvinkeln oförändrad. Men med mer komplexa former, till exempel invändiga och utvändiga radier, uppstår inkonsekvenser vad gäller den inställda ingreppsvinkeln.
När verktyget kommer in i ett invändigt hörn där omslutningen på verktyget ökar så kompenserar Camsystemet det med att ta ett mindre radiellt ingrepp för att bibehålla ingreppsvinkeln så att ett konstant skärtryck bibehålls. Om verktygsbanorna inte kan anpassas kommer resultatet att bli slag, vibrationer och i värsta fall verktygsbrott.
Att lägga ut korrekta verktygsbanor med CAM-system är grunden för en lyckad dynamisk fräsning. Ett CAM-system ger automatiskt olika matningar för att hålla spånflödet konstant. För att behålla konstant ingreppsvinkel vid dynamisk fräsning måste CAM-systemet använda trochoidmetoden och peel milling teknik i början på radien. Utöver verktygsbanorna reducerar ofta CAM-systemen L-rörelsen avsevärt för att ytterligare minska cykeltiderna.
Med en optimerad verktygsbana och konstant skärvinkel, kan radien på fräsen anpassas till den invändiga radien utan risk för att fräsen överbelastas, hugger eller skär för mycket. Den egenskapen gör att fräsarna kan bearbeta djupa spår i ett pass, således minskar mängden material vid finbearbetningen - cykeltiden minskar.
Optimerade grovbearbetningsstrategier gäller även för specifika arbetsmaterial. Seco har genomfört omfattande tester med stål, rostfritt stål, gjutjärn, titan, aluminium och stål med hårdhet upp till 48 HRc. Seco rekommenderar i första hand 10 till 15% AEMX för standard materialgrupper (P1,2,3,4,M2, K2).
Och 5% skärdjup (AEMX) för de mer tuffa arbetsmaterialen (S2, S12, M4, P12, H7). Seco har en optimerad skärhastighet och matning för dessa specifika ingreppsvinklar, dessa skärdata kan erhållas med SUGGEST som finns på www.secotools.com. Skärdjup (ae) kan ökas än vad som rekommenderas, men då bör skärhastighet och matning per tand minskas gradvis.
Effektsvagare maskiner, som normalt inte klarar grovbearbetning, kan helt enkelt minska ingreppsvinkeln och använda trochoidfräsning. Då minskar skärkrafterna och behovet av högre maskineffekt minskar, men det ger ändå hög produktivitet tack vare stora skärdjup. Det minskar ev. stora investeringskostnader då grovbearbetning kan utföras i befintliga maskiner.
När grovbearbetning tillämpas i svårbearbetade material som t.ex. rostfritt stål och titan, bör kylvätska appliceras under hela bearbetningen. Det är viktigt att kyla ner hela skäreggen. Vid bearbetning i stål och gjutjärn bör tryckluft användas för att avlägsna spån.
Notera att de flesta program för avancerad grovbearbetning/dynamisk fräsning måste genereras externt, ej via maskinens styrning. De flesta CAM-leverantörer idag erbjuder optimering av verktygsbanor. Vid programmering i maskin kan operatören manuellt ange ingreppsvinkel enligt Secos rekommendation, men endast för enklare grovbearbetning eller fasta cykler med trochoidfräsning.
En fordonstillverkare såg fördelarna med optimerad grovbearbetning och verktygsbanor för en fordonskomponent. Verkstaden minskade inte bara den totala cykeltiden på detaljen, från 8,5 minuter till endast 1,1 minut, den ökade också produktiviteten från 80 delar till 250 delar per fräs.
Konstant ingreppsvinkel och medelspåntjocklek är nyckeln till optimerad grovbearbetning. Med CAM-program specifikt för optimering av verktygsbanor och dynamisk fräsning, kan dagens tillverkare kontrollera verktygets ingreppsvinkel och bibehålla konsekvent belastning. Då kan även temperaturen kontrolleras, högre skärhastighet och matning per tand kan tillämpas, samt större skärdjup för att minska den totala cykeltiden.
Vid optmerad grovbearbetning erfordras rätt CAM-program för extern programmering. Medan de flesta leverantörer av skärande verktyg erbjuder verktyg för specifika material, är det få som utvecklar verktygsgeometrier för avancerad bearbetning och verktygsbanor som krävs. Med rätt verktyg och dynamisk fräsning kan tillverkare öka avverkningshastigheten med så mycket som 500% jämfört med traditionella bearbetningsmetoder.
READ AND DOWNLOAD OUR DYNAMIC MILLING E-BOOK FOR FREE