Škoda Auto社とSeco Tools社が協力して生産のボトルネックを解消
チェコのŠkoda Auto社の生産工場のように近代的なオペレーションであっても、改善の機会は存在します。複雑なギアボックス部品をより効率的に加工するために、Škoda社とSeco Tools社は共同で複合切削工具の開発と評価を行いました。Secoの技術者は、3Dプリントされたモデルと革新的なツールデザインを使用して、従来とは異なるソリューションを迅速に作成し、生産を合理化、短縮しました。1
1864年に設立されたチェコ共和国のVrchlabíにあるŠkoda Autoの生産工場は、長い間、優れた製造の伝統を誇っています。Škodaは、1946年以来、1203、105、120、そして最近ではFavorit、Octavia、Roomsterなどの自動車を生産しています。2012年には、この工場を最新の自動車部品メーカーに生まれ変わらせました。同社は、シュコダ車や、シュコダの親会社であるフォルクスワーゲン・グループの他のブランドに使用されるダイレクトシフト・オートマチック・ギアボックスを生産しています。
約1,000人の従業員が1日2交代制で勤務し、高度なDSGダイレクトシフトシステム技術を採用した2クラッチ7速DQ200オートマチックギアボックスを最大2,300台生産しています。Vrchlabí生産工場は、この地域で最も重要な産業雇用主の一つであり、VWグループの中で最も先進的な施設の一つです。生産工程では、協働ロボット、自律走行システム、製造設計・文書化のためのデジタルツインアプローチなど、インダストリー4.0を支える最先端の技術が採用されています。
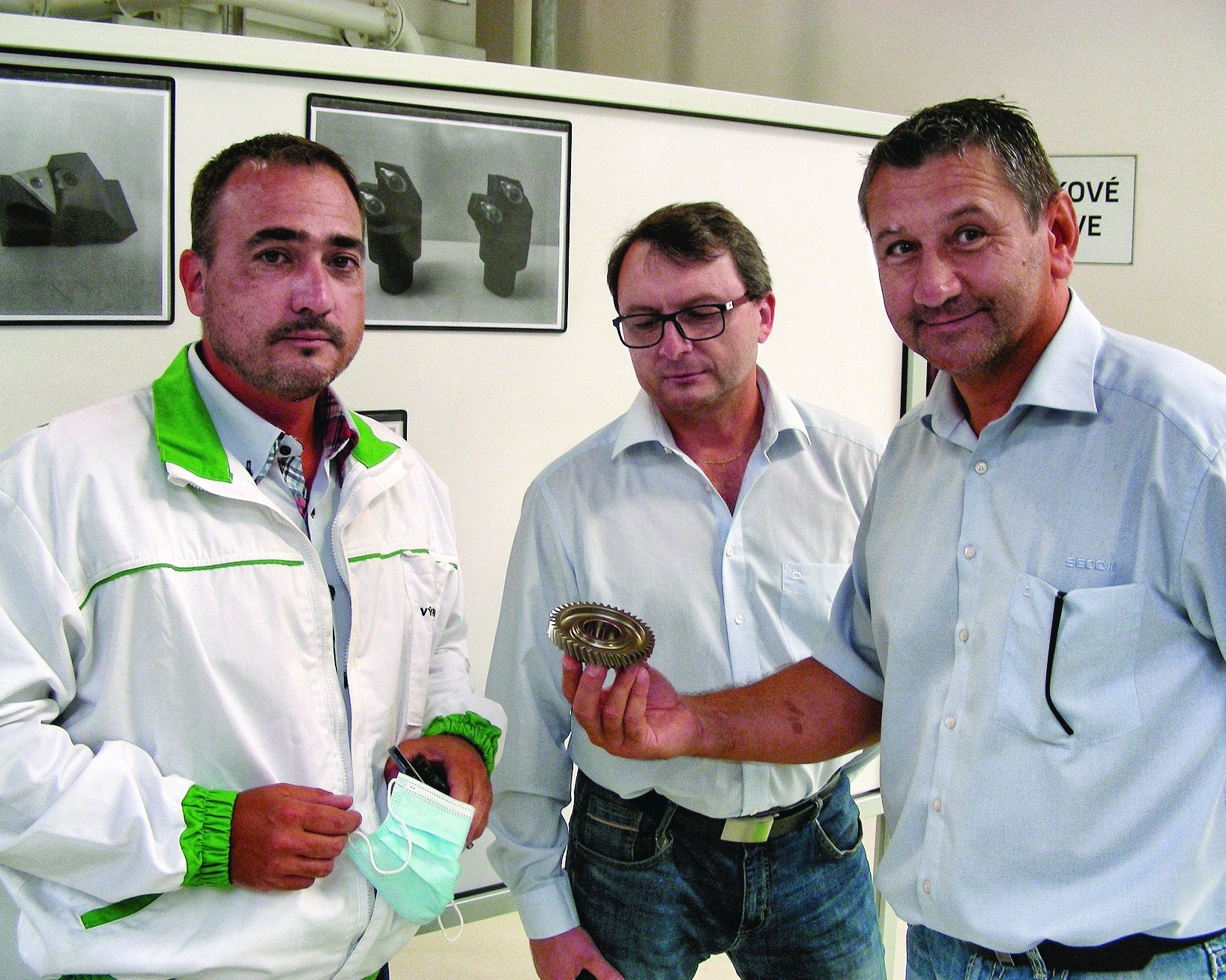
Seco and Skoda partnership
Škoda社は、どんなに先進的な設備であっても、さらなる最適化プロジェクトの機会があることを認識しています。そのようなプロジェクトの一つに、ユニークなギアボックス部品の生産におけるボトルネックの解消がありました。旋削加工では、3種類のISO切削工具を使用し、サイクルタイムに約51秒を費やしていました。CNCターニングセンターの2番目のスピンドルは未使用状態で、3つの工具が部品を加工している間、生産時間を無駄にしていました。
Škoda社は、ターニングセンターでの加工時間を短縮し、生産能力を向上させようとした。様々な切削工具メーカーがインサートや切削速度の変更を提案したが、期待した効率は得られなかった。これらの提案は、機械加工時間の短縮を最小限に抑え、切削工具のコストを増加させるものでした。
そこでŠkoda社は、Seco Toolsが提案した革新的なアプローチを採用することにした。Secoは、ギアボックス部品を正確かつ効率的に加工するための複合切削工具を開発・評価するプロジェクトを立ち上げた。Secoの技術者は、わずか4日間で従来とは異なるソリューションを開発し、3Dプリンタで作成した2つの新しいツールのプラスチックモデルを発表した。Secoの最初の提案の詳細を検討した結果、1つの多目的切削工具で必要なすべての加工を行うことができるという、ユニークなソリューションが見つかりました。さらに2週間後には、その工具を使った生産テストが行われ、全体的な機能性と要求される部品パラメータを満たす能力が証明された。そして、プロジェクト開始から約8週間後には、この工具を使った生産が開始されたのである。
3本の工具を1本にしたことで、Škoda社は作業中の工具交換がなくなり、生産時間を短縮することができました。また、作業順序を分析することで、技術者はツールパスをさらに最適化し、より多くの時間を節約することができました。
革新的なSecoの工具によって、最終的な加工時間は40.2秒に短縮され、10.7秒、つまり元の作業のサイクルタイムの20%以上を節約することができました。この優れた結果により、Škoda社は1年間で10,000ユーロ以上の工具コストを削減しました。
アプリケーションエンジニアのMilan Kudrnáč氏とキーアカウントマネージャーのPetr Zeman氏は、Secoを代表してサプライヤー側からこのŠkoda社のプロジェクトに参加しました。アディティブ・マニュファクチャリングは、彼らの努力をサポートし、迅速かつ低コストで金型モデルの作成を可能にしました。このモデルは、新しいソリューションを迅速かつ容易に検証し、潜在的な生産上の問題を発見するのに役立ちました。また、このモデルは、製造パートナーにソリューションを提示するための完璧な手段となりました。
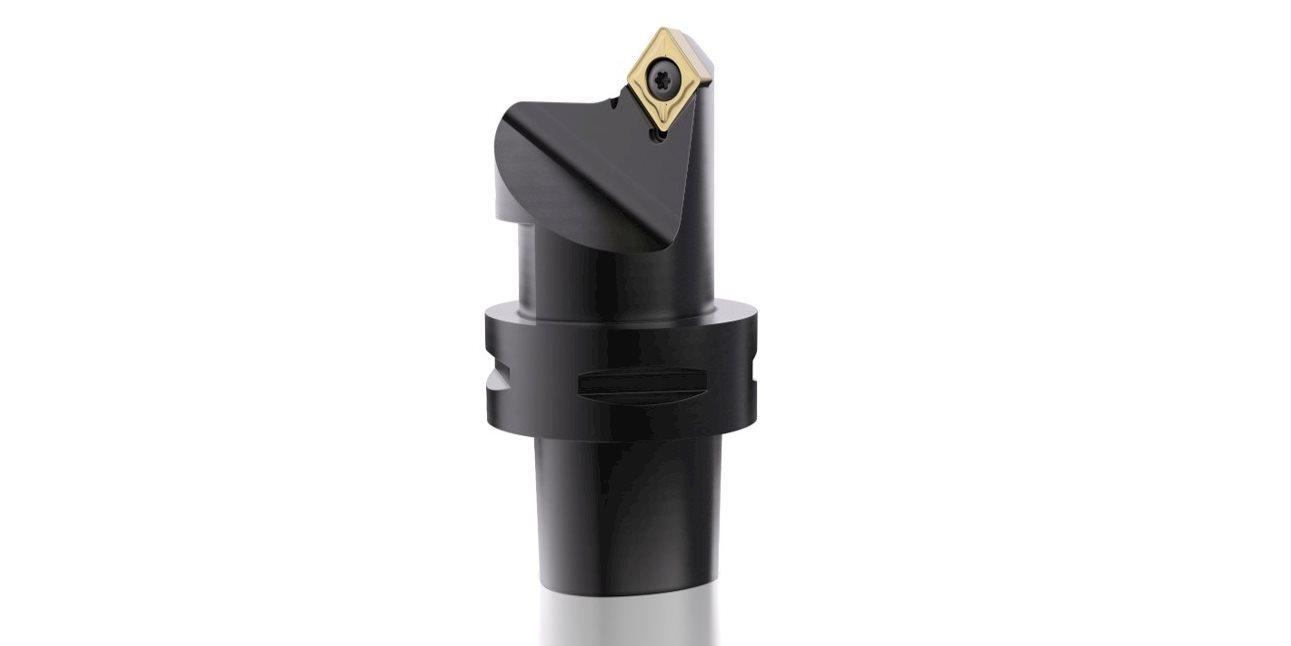
カスタム ツール
Škoda社とSecoは密接に協力してこのプロジェクトをサポートしました。Secoの従業員は、プロジェクトへのŠkoda社の積極的なアプローチ、自動車メーカーの開発プロセスへの関心、そしてワークショップで直接協力する機会を高く評価しました。コミュニケーションの良さが、このコラボレーションの成功の鍵となりました。
Škoda Auto Vrchlabí工場の機械加工のスペシャリストであるVladimir Flandera氏は、このプロジェクトへの参加を管理した。彼はまた、Secoの積極的なアプローチ、スピードと柔軟性、そして継続的かつ完全なコミュニケーションの重要性を評価しています。
このプロジェクトの主な目標を達成したことで、Škodaは年間の直接工具費だけで10,650ユーロを節約しました。さらに、専用の切削工具を1つ使用することで、置き換えた3つのISO工具よりも低コストで済みました。しかし、最大の効果は、生産上のボトルネックがなくなったことにあります。特別に設計された工具により、ワークフロー全体がスムーズになり、CNCターニングセンターの第2スピンドルがワークピースに次の作業を行うまでの時間が大幅に短縮されました。また、加工時間が短縮されたことで、切削部の冷却や切粉除去のための圧縮空気の使用量も減少しました。
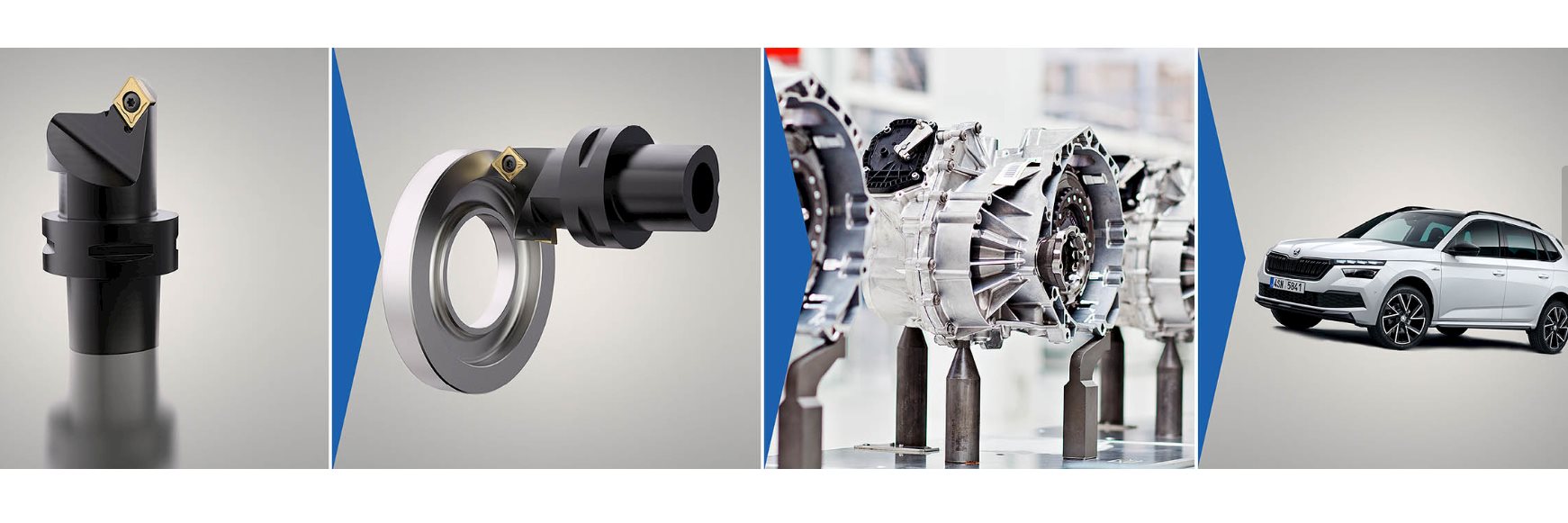
Škoda社は、3Dプリンティング技術を用いて、ツーリング・コンセプトの実物モデルを開発しました。この取り組みの優れた経験に基づき、同社は他のプロジェクトでもこの手法を採用しました。この成功は、Škoda社内のイノベーションコンテストで評価され、Vrchlabí工場では、このソリューションを他のVW生産工場でグローバルに使用しています。
Škoda Auto社Vrchlabí工場のManaging DirectorであるDipl.Ing.Ivan Slimák博士は、このツール開発プロジェクトを非常に高く評価しており、Škoda社とSeco Tools社の効果的なコラボレーションに注目していますが、それはコスト削減だけではありません。彼の目には、経験を共有する機会が得られたこと、そして関係者の専門的かつ個人的な成長が得られたことが、最大のメリットとして映った。「チェコの産業が、最新の技術によって世界の変化に対応でき、さらにそれをリードできるスキルを持った人材がいることを示すことは、非常に重要なことです」と語った。
私たちのソリューションや、お客様のプロジェクトをサポートする方法については、お問い合わせください。
お 問い合わせ