TALAŞ OLUŞUMU HAKKINDA BILMENIZ GEREKEN ŞEYLER
İşleme sırasında en önemli nokta, kesme işleminin bozulmaması ve tezgah takımı, kesici takım ve iş parçası üzerinde herhangi bir hasar olmaması için bu tür bir talaş oluşumu ve tahliyedir. Ayrıca, tezgah takımı operatörünün güvenliği de korunmalıdır.Düzgün talaş oluşumu ve tahliyesi, kesme işleminin bozulmadan devam etmesini, operatörün güvenliğini ve tezgah takımı, kesici takımı ve malzemeye zarar vermemesini sağlar. Talaş oluşumu, işleme teknolojisindeki diğer konulardan daha fazla bilimsel ilgi çekmiştir, ancak bilimsel sonuçların pratik, kullanılabilir modellere dönüştürülmesinin zor olduğu kanıtlanmıştır. Burada talaş oluşumuna bu kadar pratik bir perspektiften yaklaşıyoruz.
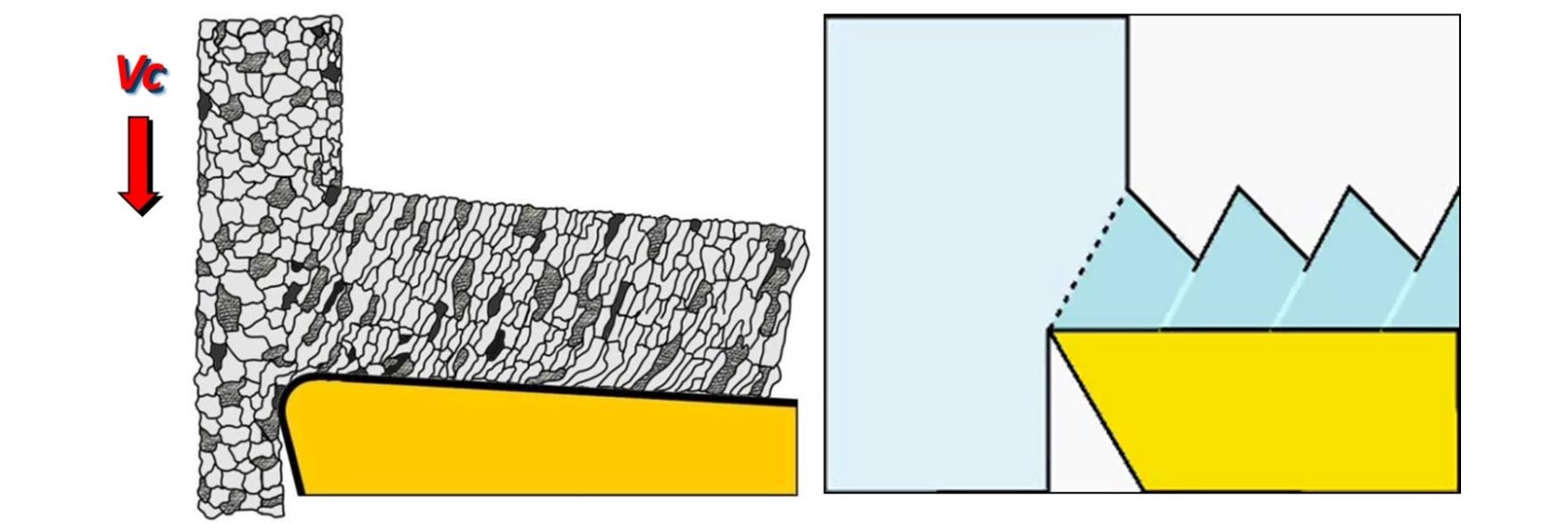
Tezgah ile işleme sırasında çıkarılan malzeme plastik deformasyon ve kesme düzleminde kesilme ile iş parçasına bağlı olarak uzun veya kısa talaş şeklinde çıkar. Tezgah ile işleme, bu kesme bölgesinde enerjinin çoğunu tüketir.
Sıkıştırılamaz malzemeyi tezgah ile, kesme düzleminde malzeme deformasyonu hacimde bir değişiklik olmadan gerçekleşir. Deformasyonun basit kesilme olarak gerçekleştiğini ve her katman makas düzlemine paralel olacak şekilde yongaların oluşturulacak malzemeye bir malzeme katmanı yığını yerleştirildiğini varsayalım. Daha sonra talaş oluşumu, malzeme katmanlarının kesilme işlemi olarak örnek olarak kabul edebilir.
Tornalamada talaş kontrolü ve takım aşınması hakkındaki Talaşlı İmalat posterimizi ücretsiz indirin
Özellikle iş parçası dahil olmak üzere talaş oluşumunu birçok faktör etkiler. Metal kesme işlemi, daha sonra kesilecek olan iş parçası malzemesinin plastik deformasyonunu içerir. Elastik ve plastik malzeme davranışı bu süreçte belirleyici bir rol oynar.
Farklı iş parçası malzemeleri, farklı kesme mukavemeti ve süneklik kombinasyonları sergiler. Bir iş parçası malzemesinin sünekliği, kesilene kadar deforme olabilme derecesidir (bkz. Şekil 2). İş parçası malzemesinin sünekliği ne kadar yüksek olursa, talaşlar o kadar uzun olur. Genel bir kural olarak, malzeme sünekliği yaklaşık %25'i aştığında, talaşlar uzundan çok uzuna değişir.
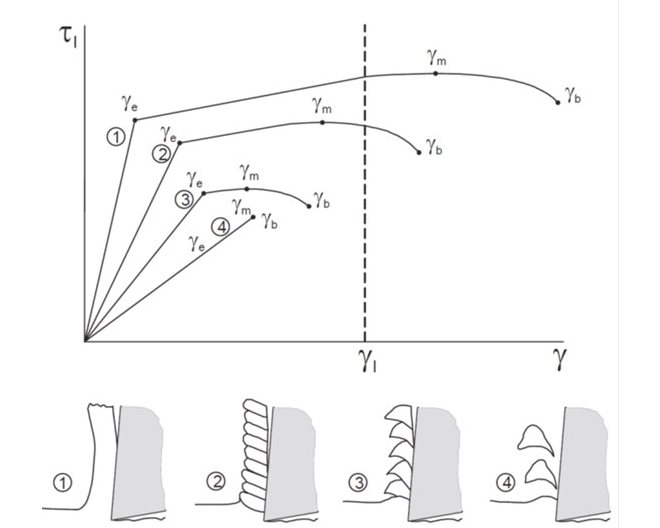
Bu yaklaşım aynı zamanda farklı iş parçası malzemelerini sınıflandırmak için ISO sisteminde de kullanılır. Her ISO grubu (P, M, K, N, S ve H) öngörülebilir talaşlar ürettiğinden, takım ve kesme koşulu seçimi malzeme davranışına uygun olmalıdır.
- ISO grubu P (çelik), oldukça yüksek sünekliğe ve uzun talaş eğilimine sahip malzemeleri içerir. Bu, talaşları kabul edilebilir bir form ve uzunlukta tutmak için uygun önlemleri gerektirir.
- ISO grupları K (dökme malzemeler) ve H (sert çelikler), kısa talaşlar üreten düşük sünekliğe sahip malzemeleri içerir. Bu, talaş kontrolünü kolaylaştırır.
- ISO grupları M (paslanmaz çelik), S (süper alaşımlar) ve N (demir dışı malzemeler), nispeten düşük sünekliğe sahip ancak aynı zamanda gözle görülür şekilde yapışkan bir yapıya sahip malzemeleri içerir. Bu malzemeler, "yapılandırılmış kenar" olarak adlandırılan talaşları oluşturur.
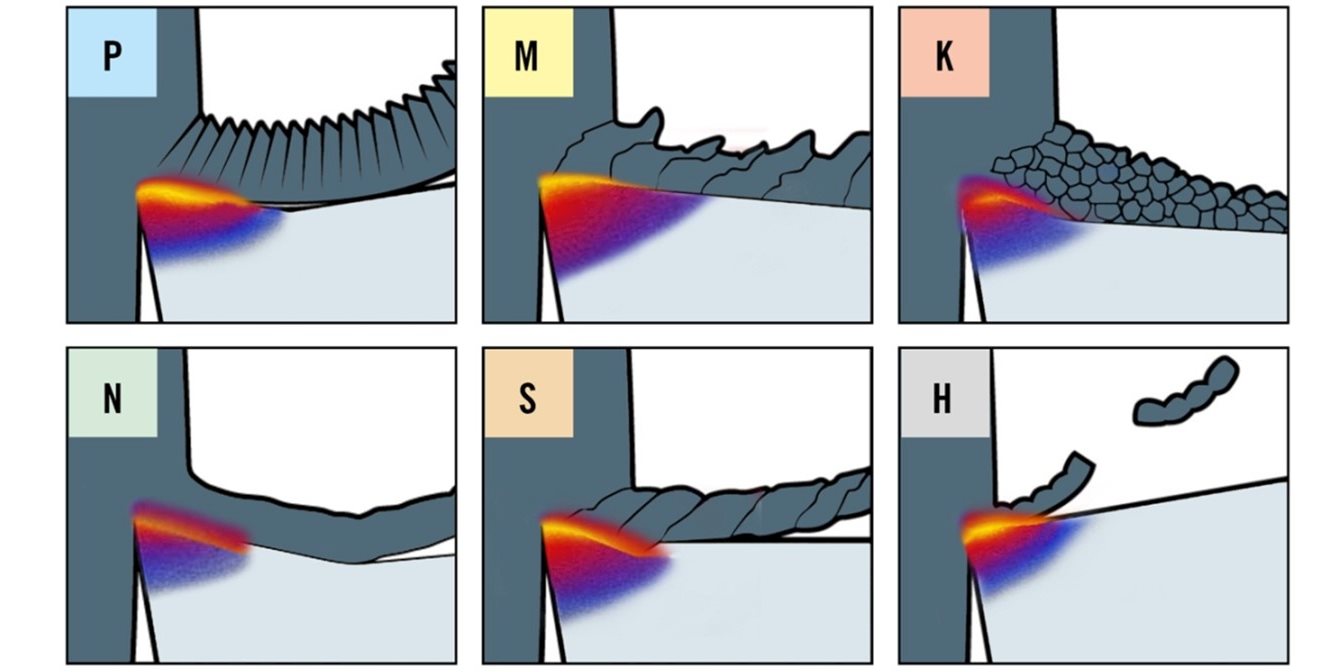
Talaşlar çok uzun boylardan çok kısa boylara kadar sınıflandırılabilir ve ideal talaşlar her iki uç noktadan da kaçınmalıdır. Çok kısa talaşlar işlemeyi kesintili hale getirir, bu da kesici kenarda erken mikro kırılmaya (talaşlanma) ve çok kısa takım ömrüne yol açar. Takım ömrü açısından, uzun talaşlar tercih edilir. Uzun, düzgün şekillendirilmiş talaşlar ayrıca işleme sırasında daha az mikro titreşim üretir ve bu da niteliksel olarak daha iyi işlenmiş yüzeylere yol açar. Ancak kesme işleminin kendisi için uzun talaşlar daha az idealdir. Bunlar takım tezgahına, iş parçasına ve kesici takıma zarar verebilir ve operatör için güvenli olmayan koşullara neden olabilirler. Ayrıca talaş konveyöründe üretim durmalarını artıran tahliye sorunları yaratabilirler.
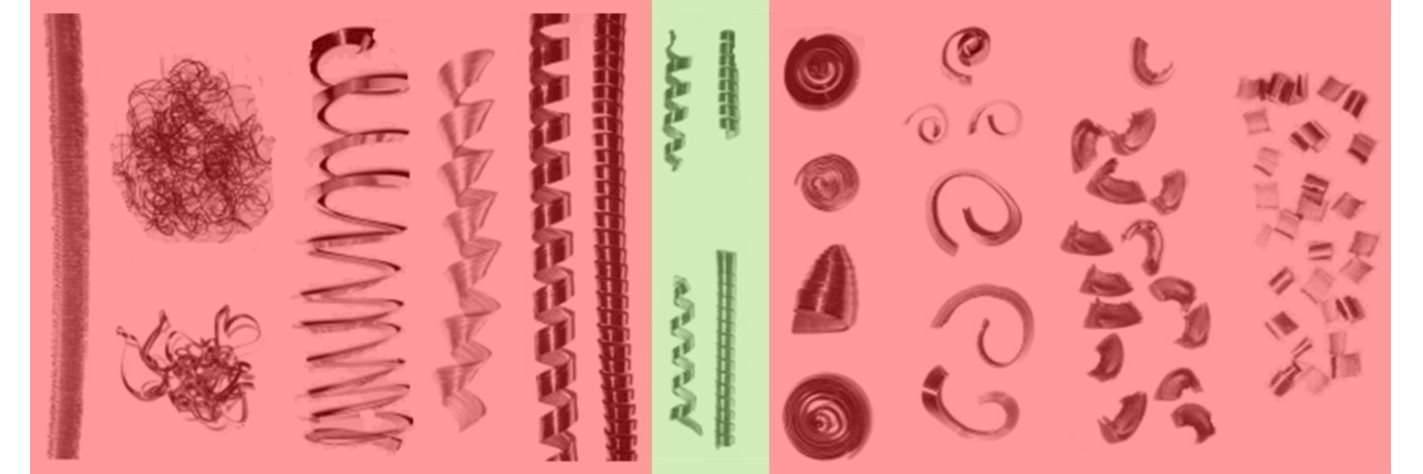
Tahliye sorunları kısa talaşlarla ortadan kalkar, ancak çok kısa takım ömrü (talaşlı kesme kenarlarından) ve işlenmiş yüzeylerin kalitesini düşüren mikro titreşimler riskine yol açan aralıklı kesmeye işaret ederler.
Spiral şekilli talaşlar - ne çok uzun ne de çok kısa - ideali temsil eder ve talaşlar söz konusu olduğunda en iyi kesme işlemi için en iyi şansa sahiptir.
Kısa, spiral talaşlar tercih edilir 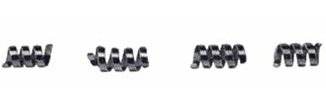 | - Daha az güç gerekir
- Kesici kenarlarda daha az gerilim
- Daha küçük kesme kuvvetleri
- Tahliye edilmesi daha kolaydır
|
Çok kısa, sıkı talaşlardan kaçının 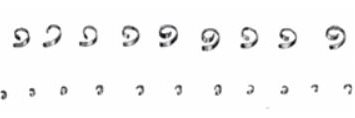 | - Daha yüksek güç gerekir
- Kesici kenarlarda daha yüksek gerilim
- Olası takım veya malzeme sapması ve titreşim
|
Uzun, telli çaplardan kaçının 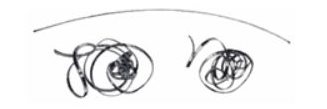 | - Tahliye edilmesi çok zor
- Operatör için tehlikeli
- İş parçasını veya takımı yeniden kesebilir ve zarar verebilir
|
Şekil 5 Farklı talaş formları ve sonuçları.
TALAŞ ZORLUKLARININ NASIL AŞILACAĞI HAKKINDA DAHA FAZLA BİLGİ ALMAK İSTER MİSİNİZ?
Inline Content - Survey
Current code - 5fce8e61489f3034e74adc64