Considerare la fisica della lavorazione e la tecnologia degli utensili per ottenere la massima resa
I nuovi sviluppi nella tecnologia della lavorazione offrono il massimo vantaggio economico se il processo di lavorazione viene considerato come un unico modello coerente. È di vitale importanza considerare i diversi possibili scenari di produzione e l'effetto finale di ciascuno sull'economia di produzione complessiva o globale.I nuovi sviluppi nella tecnologia della lavorazione offrono il massimo vantaggio economico se il processo di lavorazione viene considerato come un unico modello coerente. È di vitale importanza considerare i diversi possibili scenari di produzione e l'effetto finale di ciascuno sull'economicità della produzione complessiva o globale. Una definizione pragmatica di economicità della produzione globale è: Garantire la massima sicurezza e prevedibilità del processo di lavorazione, mantenendo al contempo la massima produttività e i costi di produzione più bassi.
Prima di eseguire un'ottimizzazione dettagliata delle singole operazioni, è necessario bilanciare la produttività e l'efficienza dei costi complessivi e valutarli su base completa o macro. Una volta completata una macro valutazione dell'intero processo di produzione, è possibile ottenere ulteriori miglioramenti considerando dove l'ottimizzazione uno-a-uno può essere vantaggiosa.
Tradizionalmente, il raggiungimento di risultati di lavorazione ottimali comportava un micro modello a prospettiva stretta basato sull'ottimizzazione uno-a-uno di un utensile in un'operazione. I macro modelli, d'altro canto, considerano la produzione da una prospettiva più ampia. Con questi macro modelli o modelli globali, il tempo totale necessario per produrre un dato pezzo gioca un ruolo più decisivo.
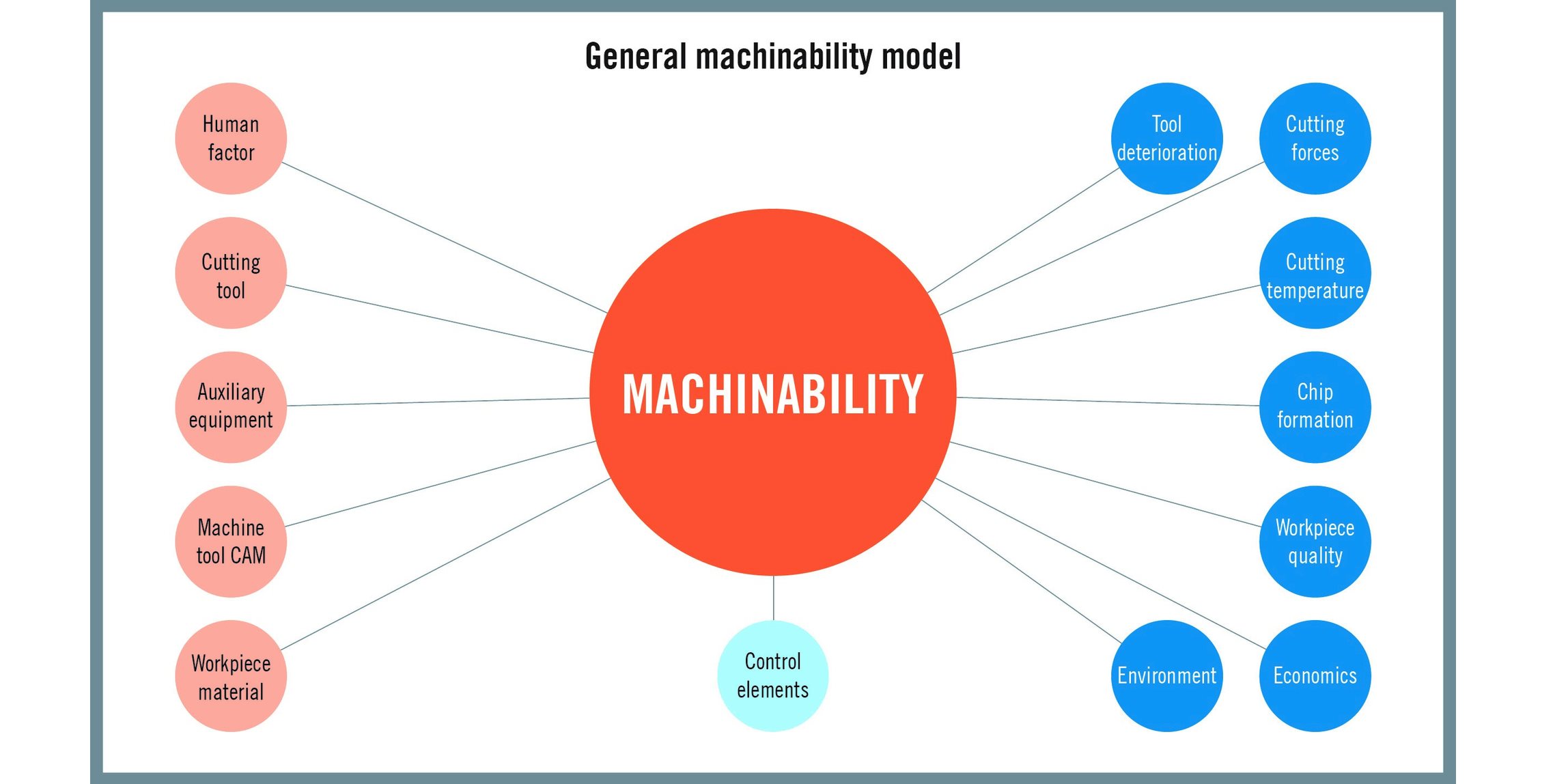
Un esempio semplificato di ottimizzazione globale coinvolge due macchine impiegate in serie per produrre un componente. Non serve ottimizzare i tempi di taglio e aumentare la resa sulla macchina A se non sono possibili miglioramenti simili sulla macchina B. La maggiore resa della macchina A produce solo costi aggiuntivi nell'inventario dei pezzi semilavorati in attesa di essere lavorati sulla macchina B. L'ottimizzazione dei costi di taglio sulla macchina A, che potrebbe limitare la produttività della macchina A ma ridurre i costi complessivi mantenendo la resa, è il modo migliore per affrontare il problema.
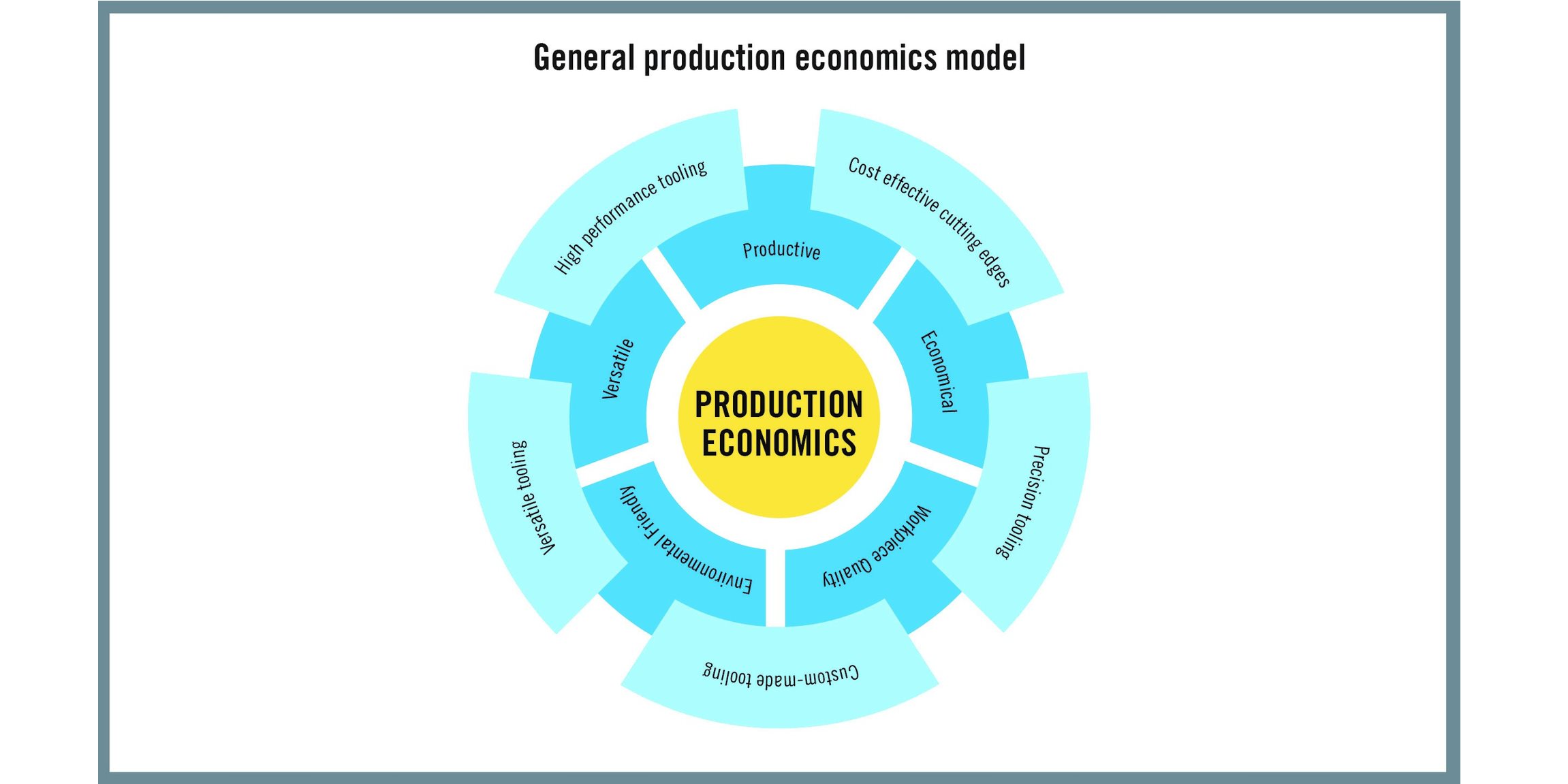
D'altra parte, quando la macchina B è inattiva in attesa di elaborare le parti prodotte dalla macchina A, l'aumento della produzione della macchina A incrementerà la resa totale. Molto dipende dal modo in cui l'officina organizza le sue operazioni di produzione, sia che in linea, a lotti o in parallelo. Non esiste una risposta universale. Ma questi esempi indicano la necessità di una visione più ampia dell'intero processo di produzione e illustrano che l'ottimizzazione dei micro-modelli deve essere eseguita con molta attenzione.
Una visione più ampia si applica anche alle macchine utensili. Una situazione tipica potrebbe comportare la decisione di un'officina di sostituire una fresatrice a pieno carico che funziona 40 ore alla settimana con una macchina ad alta velocità. Tuttavia, quando la nuova macchina è in funzione, trascorre metà del tempo inattiva. L'officina ora si trova di fronte alla sfida e alle spese di trovare più lavoro per mantenere la nuova macchina occupata e giustificare l'investimento in essa. Il percorso migliore sarebbe stato quello di esaminare prima il quadro più ampio e di anticipare ciò che sarebbe derivato dalla maggiore resa della nuova macchina.
Un'ottimizzazione one-to-one si concentra su un'applicazione e un utensile da taglio ed è progettata per creare asportazione elevata al costo più basso possibile. Il processo consiste nella selezione di utensili più adatti per lavorare il pezzo e impiegare la massima profondità di taglio al massimo avanzamento possibile. Naturalmente, le profondità di taglio e gli avanzamenti massini sono soggetti a vincoli di potenza e coppia della macchina disponibili, stabilità del pezzo e sicurezza del serraggio dell'utensile.
La fase finale dell'ottimizzazione one-to-one consiste nel selezionare il criterio appropriato in termini di costo minimo o produttività massima e nell'utilizzare la velocità di taglio per perfezionare il raggiungimento di tale criterio. In questa analisi, è importante ricordare il modello Taylor per la determinazione della durata dell'utensile. Il modello Taylor dimostra che per una data combinazione di profondità di taglio e avanzamento, esiste una certa finestra per le velocità di taglio in cui il deterioramento dell'utensile è sicuro, prevedibile e controllabile. Quando si lavora all'interno di tale finestra, è possibile qualificare e quantificare il rapporto tra velocità di taglio, usura dell'utensile e durata dell'utensile.
Inizialmente, il tempo di lavorazione diminuisce e la produttività aumenta con l'aumento delle velocità di taglio. Tuttavia, al di sopra di una certa velocità di taglio, la durata dell'utensile diventa così breve che i taglienti richiedono frequenti sostituzioni. Nel quadro generale, il costo del tempo di lavorazione ridotto ha un effetto minore rispetto al costo dell'utensile in rapido aumento. L'obiettivo è quello di determinare una velocità di taglio in cui la somma dei due costi si equilibra per ottenere un costo totale minimo.
Nella ricerca della produttività, le officine dovrebbero concentrarsi sul quadro generale della produzione: tempo totale floor-to-floor necessario per produrre il pezzo ed evitare di pensare eccessivamente ai dettagli minuscoli.
Gli standard odierni per l'alta qualità dei pezzi sono molto più rigorosi di quelli del passato. Tuttavia, la ricerca della perfezione può essere costosa. L'obiettivo è l'alta qualità, ma la qualità eccessivamente alta è uno spreco di denaro. Le officine dovrebbero considerare come possono produrre il pezzo peggiore possibile che sia ancora accettabile dal punto di vista funzionale. Il rispetto dei requisiti minimi può ridurre drasticamente i costi e aumentare notevolmente la produttività.
Analogamente, quando si concentra interamente su tempi di ciclo più bassi per la massima produttività, l'affidabilità di un processo di lavorazione dei metalli può deteriorarsi. Quando un processo viene eseguito costantemente ai limiti dei suoi parametri e oltre, il prezzo viene rifiutato o i pezzi in lavorazione vengono scartati e viene perso tempo.
L'efficienza produttiva comporta tre fattori: qualità, tempo di produzione e costo. Devono essere presi in considerazione anche fattori ambientali quali il consumo di energia, lo smaltimento o il riciclo degli utensili usurati, gli scarti della lavorazione e la sicurezza e il benessere dei dipendenti.
Molti fattori tecnici individuali influenzano l'efficienza della produzione. Per i processi di lavorazione, non è affatto insolito che uno o più di 50 to70 fattori individuali abbiano un effetto apprezzabile sull'efficienza. I fattori tipici includono utensili/portautensili, configurazione e materiali del pezzo in lavorazione, capacità e dati di processo delle apparecchiature, fattori umani, apparecchiature periferiche e problemi di manutenzione.
Uno dei fattori più influenti sull'efficienza della produzione è il risultato dell'interazione tra utensile e pezzo in lavorazione. La comprensione delle modalità di usura e dei problemi dell'utensile è essenziale per il controllo del processo di lavorazione. I fenomeni legati all'usura sono generalmente graduali e prevedibili, mentre altri problemi, come la rottura dell'utensile, mancano della prevedibilità necessaria per mantenere un processo di taglio affidabile.
L'equilibrio tra produttività, affidabilità e costi degli utensili richiede utensili che offrono versatilità e flessibilità in un'ampia finestra di applicazione. Gli utensili versatili o universali (vedere la barra laterale di seguito) rappresentano una soluzione alla chiara tendenza della produzione verso lotti più piccoli. Il passaggio a lotti di lavorazione più piccoli è il risultato di un maggiore utilizzo delle strategie di produzione just-in-time e della crescita dell'esternalizzazione.
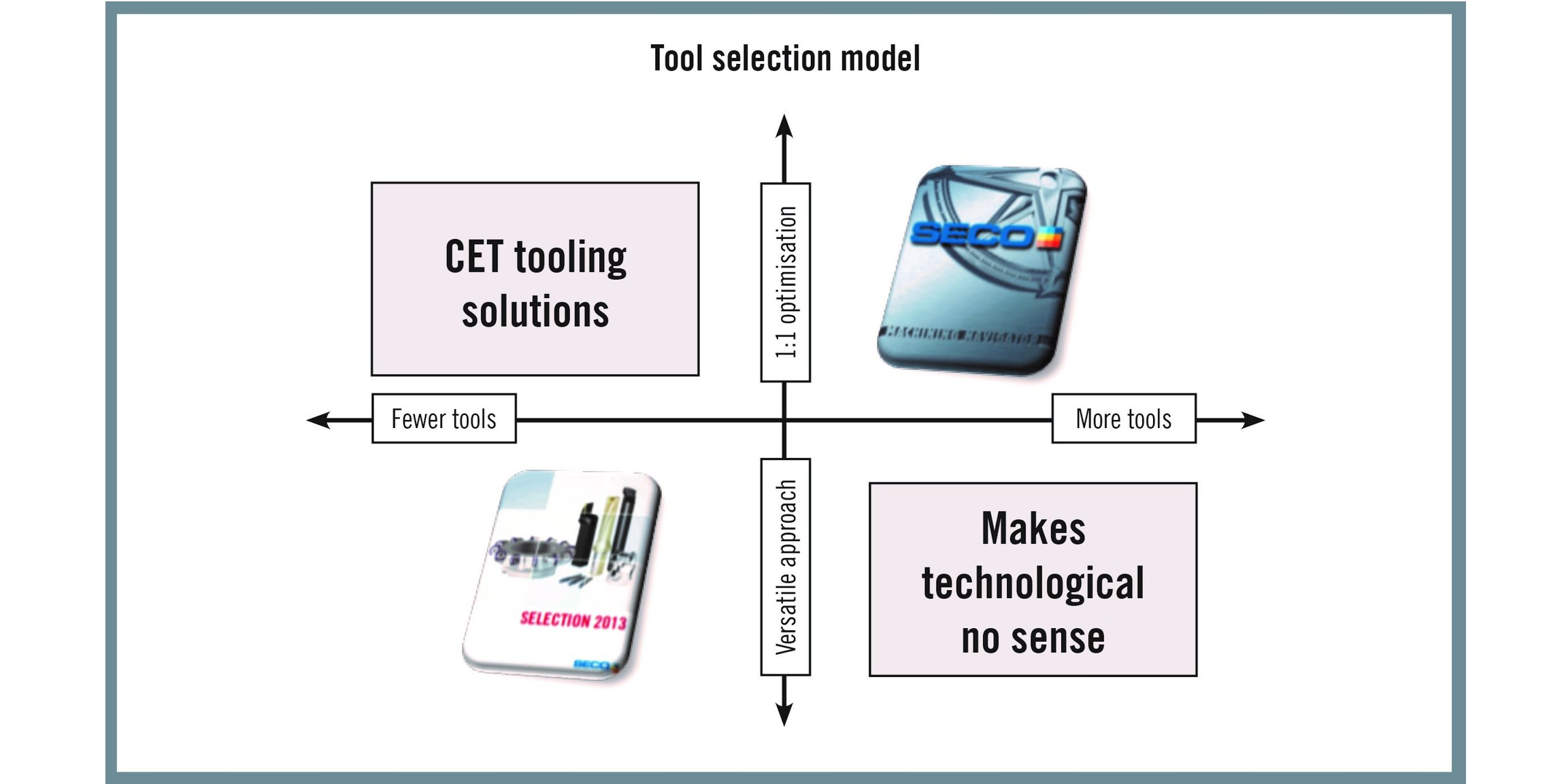
I subappaltatori devono affrontare lotti di dimensioni inferiori che devono essere prodotti regolarmente ma non continuamente. In passato, i magazzini utensili hanno contribuito a ridurre i tempi di fermo macchina per il cambio utensili e l'uso dei magazzini utensili su pallet ha ridotto i tempi di fermo macchina dovuti alle movimentazione dei pezzi in lavorazione. Gli utensili universali riducono i tempi di i tempi di fermo macchina riducendo al minimo il tempo necessario per il passaggio a un nuovo utensile al cambio del pezzo in lavorazione, eliminando la necessità di configurare e testare un nuovo utensile. La riduzione al minimo del numero di utensili diversi in officina riduce i tempi di movimentazione degli utensili e aumenta il tempo disponibile per le operazioni di lavorazione.
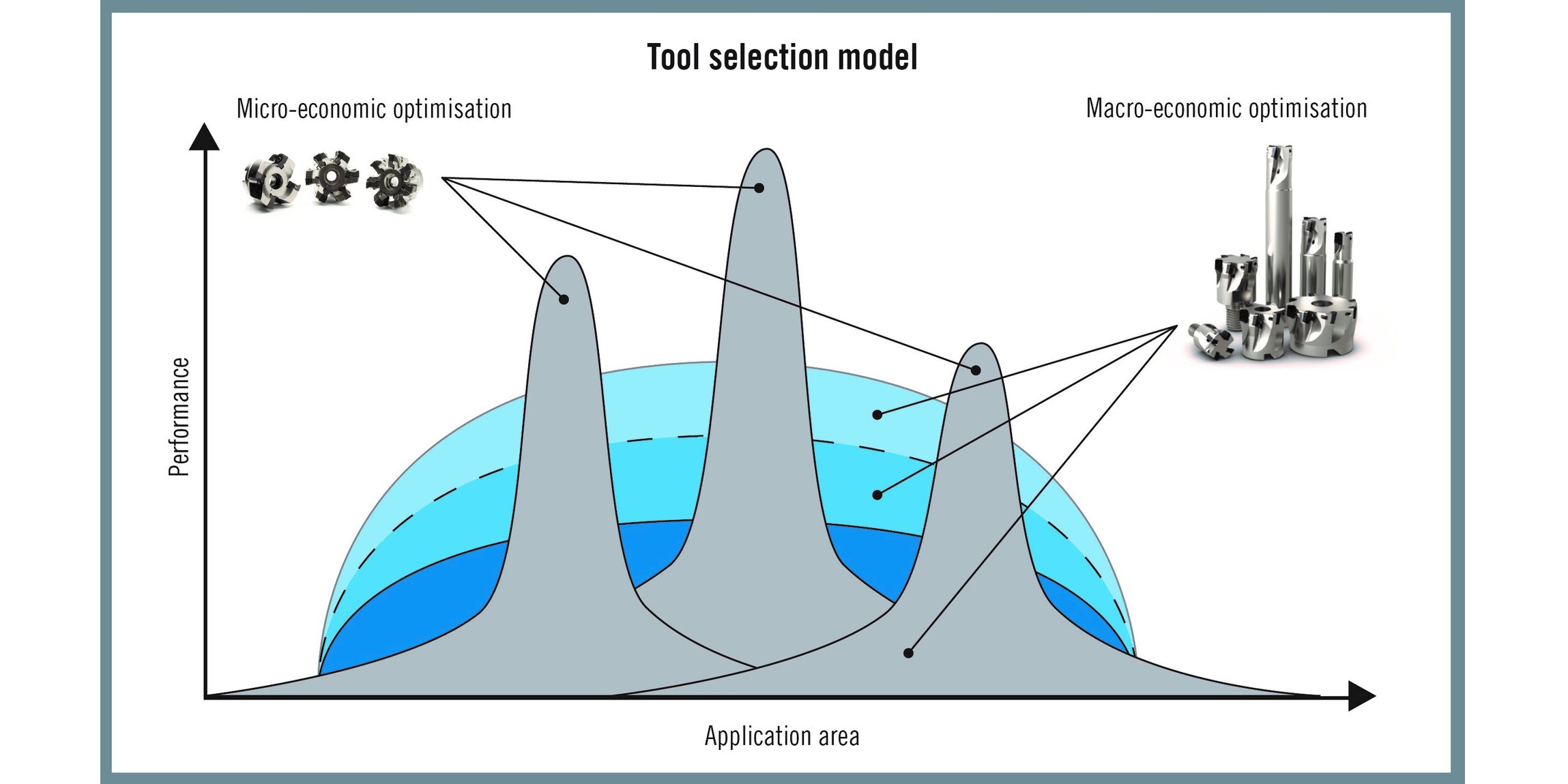
Il pensiero di scelta dell'utensile tradizionale tende ad essere orientato all'applicazione, cercando un utensile specifico per acciaio, acciaio inossidabile o per sgrossatura o fresatura, ad esempio. La cosa più importante della scelta degli utensili per una singola operazione è pensare a come tale operazione si inserisce nel quadro complessivo della produzione. La scelta dovrebbe essere orientata verso ciò che si desidera in termini di produttività, ottimizzazione dei costi o affidabilità e ciò che meglio si adatta a una visione ampia del processo di produzione.
La visione generale dell'ottimizzazione dei processi non deve necessariamente essere complessa; può implicare analisi e azioni molto semplici e basilari. L'esame degli utensili impiegati è un esempio fondamentale. La corretta interpretazione di ciò che utensili mostrano offre una prospettiva eccellente su ciò che accade in officina. Ad esempio, se un'officina utilizza generalmente inserti con taglienti lunghi 12 mm e modelli di usura sugli utensili che raggiungono solo 2 o 2,5 mm, probabilmente quell'officina utilizza inserti troppo grandi per il tipo di operazioni effettuate. Gli utensili con taglienti da 6 mm sarebbero più che sufficienti per il lavoro. Ancora più importante, un utensile con taglienti lunghi 6 mm è notevolmente più economico di un utensile con tagliente da 10 mm e può ridurre i costi dell'utensile del 50% senza perdere produttività.
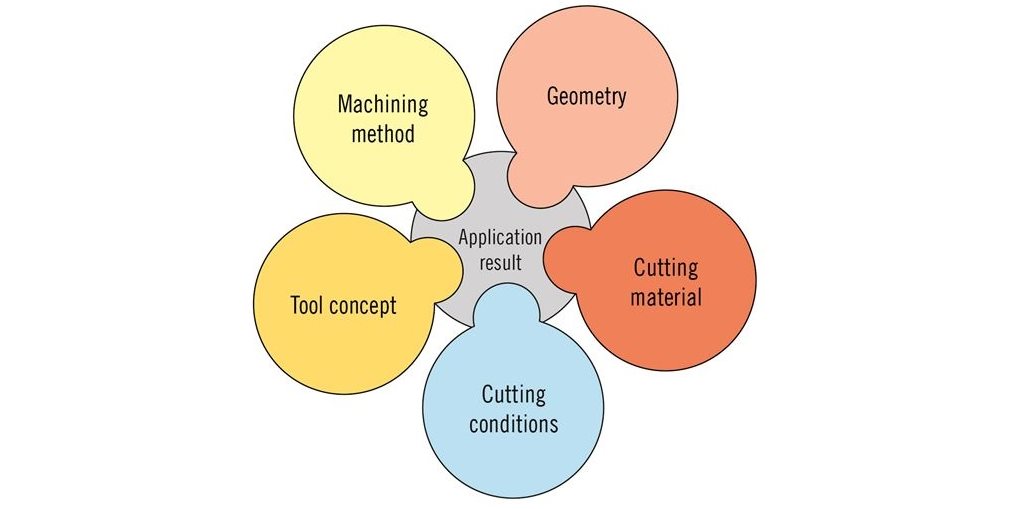
Inline Content - Survey
Current code - 5fce8e61489f3034e74adc64