Pylon lotniczy
Pylony skrzydeł podnoszą złożoność na nowe wyżyny, z kutym tytanem, złożoną geometrią i surowymi standardami. Sprostaj tym wyzwaniom dzięki zwiększonej produktywności.Rosnące znaczenie zrównoważonego rozwoju popchnęło produkcję lotniczą do tworzenia nowych projektów samolotów z bardziej wydajnymi materiałami, zużyciem paliwa i śladem węglowym. Jednocześnie klienci wywierają presję na producentów komponentów lotniczych, aby zwiększyli swoją wydajność i obniżyli koszty. Twardsze, wysoce odporne na ciepło, trudne do obróbki lekkie materiały zwiększają wyzwania produkcyjne.
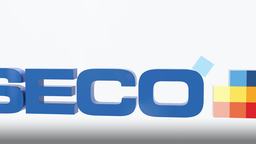
Weźmy na przykład pylony skrzydeł, zaprojektowane w parach, które muszą idealnie sklejać się, aby utworzyć gotowe części, o skomplikowanych kształtach, które komplikują trzymanie i sztywność pracy. Gdy te odkuwki tytanowe są wysyłane do producentów, partie części mogą wyświetlać odchylenia wymiarowe 5-10 mm. Zaprogramowane procesy obróbki opierają się na spójności, co utrudnia finalizowanie sekwencji produkcyjnych, dobór oprzyrządowania, ustawianie maszyn i rozpoczynanie cięcia części.
Obrabiarki muszą w szerokim zakresie wykorzystywać metrologię pokładową, aby dostosować się do zmiennych wymiarów. Pomiary te mogą wydłużyć czas cyklu o 5%-10%, ale bez nich producenci ryzykują wibracje, przeciążenie narzędzi i drogie złomowane części.
Aby sprostać tym kaskadowym wyzwaniom, producenci pylonów skrzydłowych muszą polegać na swoich dostawcach narzędzi w zakresie trwałych, zoptymalizowanych narzędzi skrawających, które wydajnie wytwarzają te części. Dostawca narzędzi z dużym doświadczeniem branżowym i wiedzą na temat części może współpracować z producentami, aby zaoferować solidne porady, które pomagają zoptymalizować obróbkę i zwiększyć wydajność.
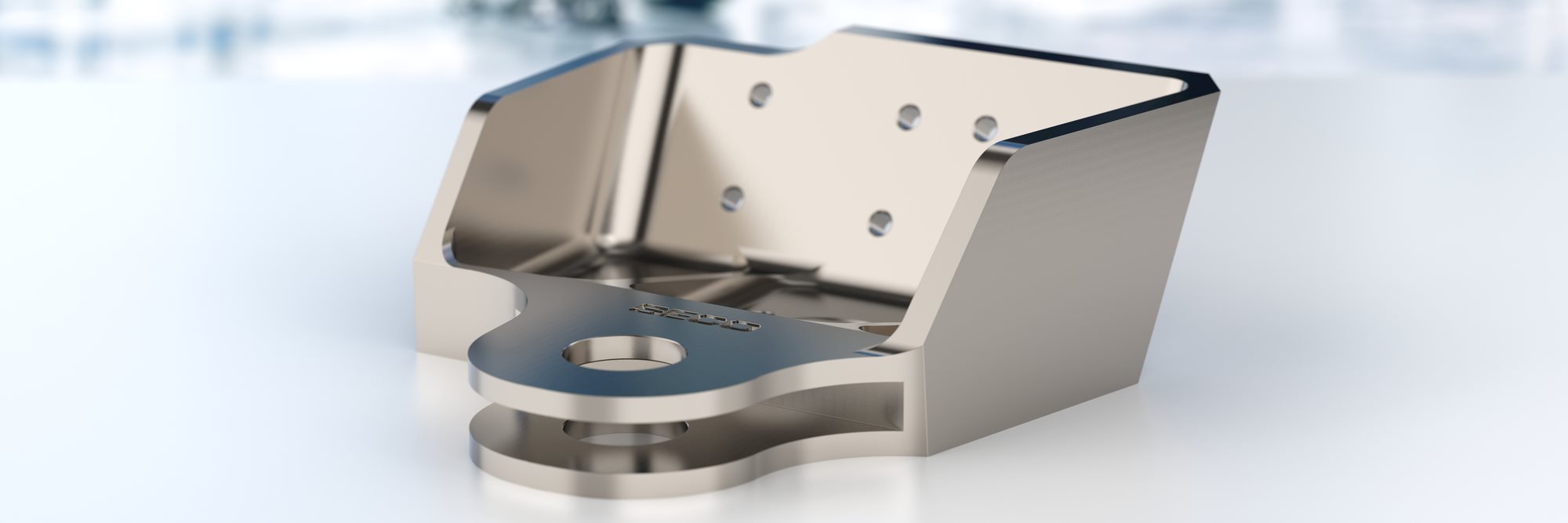
Tak jak osie, hamulce, lusterka wsteczne i zamki drzwi różnią się w zależności od modelu pojazdu i producenta, tak samo pylony skrzydeł od jednego producenta płatowca i samolotu do drugiego. Części te pochodzą z odkuwek tytanowych i chociaż każdy dostawca konkretnego pylonu używa tego samego modelu części 3D, każda matryca jest inna. Wymiary gotowej kucia mogą się różnić o 5-10 mm od jednego przedmiotu obrabianego do drugiego i od jednej partii części do drugiej, nawet jeśli matryca działa idealnie. Ze względu na nieprzewidywalne wymiary tych części i ich powierzchni, producenci potrzebują metrologii pokładowej, aby dopasować się do wymagających specyfikacji. Różnice te utrudniają również wybór narzędzi i sfinalizowanie programów obróbki.
Kuty tytan tworzy trudną do obróbki powłokę zewnętrzną. Dodatkowo materiał może samotwardzać się podczas procesu obróbki, zwiększając ryzyko pęknięcia narzędzia, co sprawia, że konieczne jest dobranie i utrzymanie odpowiedniego płynu chłodzącego. Wraz z samym materiałem i jego właściwościami obróbkowymi, kieszenie zaangażowane w projektowanie tej części wymagają użycia długich narzędzi, które mogą być trudne do wyboru, nie mówiąc już o stabilizacji. Głębokość cięcia i nierówne lub przerywane cięcia dodatkowo komplikują poszukiwanie idealnych rezultatów.
Długotrwały proces produkcji pylonu skrzydłowego obejmuje do pięciu konfiguracji, z których każda ma powiązane mocowanie, aby pomieścić szczeliny i głębokość kieszeni projektu. Ta złożona sekwencja obróbki stawia przed producentami części lotniczych wyzwanie utrzymania dokładności i powtarzalności. Geometria części utrudnia trzymanie pracy, szczególnie na obrabiarkach 5-osiowych zwykle używanych do produkcji pylonów skrzydeł. Biorąc pod uwagę precyzję wymaganą dla tych części oraz fakt, że każdy pylon składa się z pary połówek, które muszą się idealnie skręcić, producenci części lotniczych potrzebują maszyn wyposażonych w metrologię pokładową, aby zapewnić spójność w całej produkcji.
Kiedy firmy produkujące części lotnicze mogą produkować więcej części przy użyciu mniejszej liczby maszyn, zmniejszają koszty na część i zwiększają wielkość produkcji w celu zwiększenia rentowności. Aby osiągnąć znaczącą wydajność, potrzebują niezawodnego procesu, który wytwarza niezmiennie wysokiej jakości części. Te duże, wartościowe części wymagają setek dolarów oprzyrządowania i 20-30 godzin obróbki, co sprawia, że złom jest kosztownym odpadem. W rezultacie, gdy producenci szukają automatyzacji w celu zwiększenia produkcji, muszą uwzględnić wzrost czasu cyklu dla metrologii o 5%-10% z powodu wariancji części.
Etap obróbki zgrubnej pylonu skrzydła samolotu wiąże się z wieloma wyzwaniami, w tym kompromisami produkcyjnymi w celu osiągnięcia wysokich wskaźników usuwania materiału (MRR) bez niepotrzebnego obciążania metalu. Kieszeń zawiera wiele funkcji, które wymagają długich narzędzi, aby dotrzeć. Narzędzia te mogą powodować wibracje, co z kolei zmniejsza jakość części i trwałość narzędzia. Ze względu na różnicę między przedmiotem obrabianym kutych części producenci mogą napotkać niekorzystne warunki skrawania, które mogą powodować złomowanie części i uszkodzenie narzędzi.
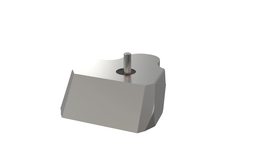
Rozwiązania Seco:
Seria frezów walcowo-czołowych JS720 zapewnia stabilne frezowanie i optymalny MRR podczas złożonego procesu obróbki zgrubnej kieszeni. Ta seria narzędzi stanowi doskonały wybór do frezowania dynamicznego. Aby stworzyć wiele otworów montażowych i współpracujących z częściami w kieszeni, wymienne wiertła do płytek Performax® zapewniają optymalny wybór.
Aby usunąć dużą ilość materiału na osi promieniowej i osiągnąć precyzyjne wymiary szczeliny dzięki wyjątkowemu wykończeniu powierzchni, unikalna konstrukcja regulowanej frezu tarczowego 335.25 wykorzystuje płytki z maksymalnie czterema krawędziami tnącymi, różnymi promieniami narożników i gatunkami płytek. Aby zapewnić elastyczność, ta seria frezów tarczowych jest dostępna w różnych średnicach. Nawet podczas cięcia tytanu płytki z węglika spiekanego XNHQ osiągają optymalną trwałość narzędzia.
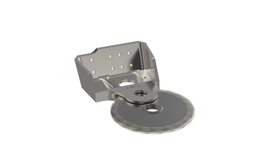
Rozwiązanie Seco:
Sukces w operacjach frezowania walcowego wymaga doskonałej geometrii części i jakości powierzchni, w połączeniu z szybkim cięciem nawet w niespójnych warunkach skrawania złożonych kutych części. Frezy walcowo-walcowe TURBO mogą osiągać wysokie posuwy, duże głębokości cięcia i wysoki MRR. Aby osiągnąć te wyniki dzięki długiej żywotności narzędzia, doskonałej precyzji i stabilnej pracy, konstrukcja narzędzia tworzy optymalny kontakt między korpusem narzędzia a płytką. Jednostronne płytki R220.69 z pojedynczą krawędzią tnącą wykorzystują mocną środkową wyrównaną z siłami skrawania i zawierają płaską wycieraczkę do optymalizacji powierzchni. Wkładki XOEX1204 oferują dodatkową opcję.
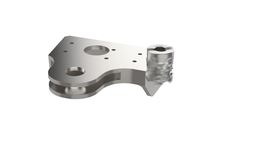
Rozwiązanie Seco:
Wysokowydajne frezy z pełnym węglikiem spiekanym zapewniają wysoką wydajność przez całą długą żywotność narzędzia. Wyjątkowy stosunek ceny do wydajności uniwersalnej frezarki walcowo-wiórowej JS522 zapewnia elastyczną obróbkę dużych partii części, dzięki czemu producenci mogą optymalizować procesy i skracać czas cykli. Ta ulepszona konstrukcja frezu walcowo-czołowego dokładnie odpowiada wyzwaniom związanym z obróbką kutego tytanu.
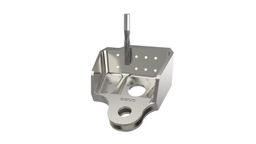
Rozwiązanie Seco:
Dostawca narzędzi z wieloletnim doświadczeniem i głębokim zrozumieniem przemysłu lotniczego może poprowadzić producentów w kierunku lepszych wyników dzięki głębokiej wiedzy i doskonałym narzędziom. Poza samymi procesami obróbki, dostawca może zaoferować dodatkowe usługi, które pomagają producentom poprawić ich wydajność i produktywność, w tym wiedzę konsultingową, profesjonalne szkolenia, recykling narzędzi i wiele innych.