Das Wissen um die Risiken des Werkzeugverschleißes und die Verbesserung der Werkzeugstandzeit sind entscheidend für Nachhaltigkeit und Rentabilität. Tatsächlich steht die Art und Weise, wie die Schneide eines Schneidwerkzeugs mit dem Werkstück interagiert, in direktem Zusammenhang mit der Gesamtrentabilität. Während ein gut gewartetes Werkzeug die Leistungsfähigkeit steigern kann, wirkt sich ein Werkzeugverschleiß und/oder Werkzeugversagen im Fertigungsbereich in vielerlei Hinsicht negativ auf das Geschäftsergebnis aus. Das Verständnis für die Ursachen von Werkzeugausfällen sowie für die damit verbundenen Risiken und deren Vermeidung ermöglicht es den Betrieben, die Produktionszeit zu optimieren und ihre Abläufe zu verbessern.
Verschleissbedingtes und nicht verschleissbedingtes Werkzeugversagen stellen dabei zwei unterschiedliche Probleme dar, die Leistung und Lebensdauer von Werkzeugen beeinträchtigen können.
Verschleißbedingtes Werkzeugversagen entsteht, wenn sich Werkzeuge im Laufe der Zeit durch wiederholten Gebrauch und Reibungskräfte allmählich abnutzen. Schneidkanten nutzen sich ab oder werden nach längerem Gebrauch stumpf, was zu einer verminderten Schneidleistung und Präzision führt. Werkzeugverschleiß ist eine natürliche Folge der Werkzeugnutzung und kann durch entsprechende Fortbildungsmaßnahmen, ordnungsgemäße Wartung, Schmierung und regelmäßigen Materialaustausch gemindert werden.
Nicht verschleißbedingtes Werkzeugversagen tritt immer dann auf, wenn Werkzeuge aufgrund von Faktoren, die nicht mit dem normalen Gebrauch zusammenhängen, brechen oder versagen. Ursache hierfür kann eine unzureichende Werkstofffestigkeit oder eine übermäßige Krafteinwirkung oder Temperaturbelastung außerhalb der Werkzeugtoleranz sein. Nicht verschleißbedingte Ausfälle treten oft plötzlich und unerwartet auf und führen zu Werkzeugbruch, Beschädigung oder vollständigem Verlust der Funktionalität.
- Qualitätsprobleme – Werkzeugversagen kann zu mangelnder Präzision, falschen Abmessungen, Oberflächenfehlern oder anderen Qualitätsproblemen bei den produzierten Bauteilen führen. Inkonsistente Bauteile entsprechen möglicherweise nicht den Kundenanforderungen. Beschädigte Bauteile erfordern oft Nacharbeit bzw. Korrekturen, wodurch sich letztlich der Ausschuss erhöht.
- Stillstandszeit – Werkzeugausfälle führen häufig zu ungeplanten Stillstandszeiten, was das Projekt zeitlich und finanziell belastet. Produktionsunterbrechungen können auch zu fehlerhaften oder unvollständigen Bauteilen sowie zu Abweichungen bei der Materialversorgung oder anderen Parametern führen. Die gleichen Abweichungen können zu fehlerhaften Bauteilen führen, was zu höherem Ausschuss und wiederum zu längeren Vorlaufzeiten führt.
- Nachbearbeitung und Ausschuss – Bei einem Werkzeugfehler während eines Produktionslaufs kann es zu einer Beschädigung des zu bearbeitenden Werkstücks oder Werkstoffs kommen. Dadurch kann es zu einer vollständigen Ausmusterung der betroffenen Bauteile kommen, was auch zu einem Anstieg des Ausschusses führt. Darüber hinaus tragen alle Nacharbeits- oder Korrekturmaßnahmen defekter Bauteile zur Erhöhung des Ausschusses und des Energieverbrauchs bei.
- Ressourcenverschwendung – Werkzeugausfälle führen nicht nur zur Entstehung von Ausschuss, sondern auch zur Verschwendung anderer Ressourcen wie Rohstoffen, Energie und Arbeitskräften. Abgenutzte oder unsachgemäß gewartete Werkzeuge neigen zu zusätzlicher Reibung und erfordern zur Erzielung des gewünschten Ergebnisses einen höheren Energieeinsatz. Ineffiziente Werkzeuge können während des Betriebs übermäßige Hitze, Vibrationen und Widerstand verursachen, was zu einem erhöhten Energieverbrauch führt.
- Erhöhter Lagerbestand – Wenn Werkzeugversagen zu Stillstandzeiten führt, steigt auch der Bestand an nicht fertig gestellten Waren, was Betriebskapital bindet und die Kosten erhöht.
Profitieren Sie noch heute von diesen Tipps:
- Das richtige Werkzeug verwenden
Mit dem besten Werkzeug für Ihre Anwendung verringern Sie den Verschleiß, vermeiden Ausschuss und erzielen bessere Ergebnisse. Bei jeder Anwendung sind Werkzeuglänge, Hartmetallsorte, Schneidengeometrie, Spanfläche und Beschichtung zu berücksichtigen. Wenn Sie Ihre Anwendung kennen, aber auf der Suche nach dem richtigen Werkzeug sind, nutzen Sie den Online-Service Suggest. - Die richtigen Schnittparameter verwenden
Die richtige Schnitttiefe, Spindeldrehzahl, Vorschubgeschwindigkeit und Bearbeitungsmethode (Verhältnis Schnittzeit/Zeit außerhalb des Schnitts) müssen aufeinander abgestimmt sein, um Ausschuss und Verschleiß zu vermeiden. Beginnen Sie mit den sicheren Schnittdaten die mit jedem Werkzeug geliefert werden, und nehmen Sie dann die Feineinstellung der Parameter vor. - Hochwertige Werkzeuge verwenden
Hochwertige, leistungsstarke Werkzeuge haben eine längere Lebensdauer und sorgen für höhere Produktivität, mehr Genauigkeit und bessere Oberflächengüte. - Werkzeuge richtig aufbewahren
Unsachgemäße Lagerung kann die Schneiden beschädigen. Werkzeuge sollten sauber und ordentlich aufbewahrt werden. Weitere Informationen finden Sie im Dokument Präventive Werkzeugpflege von Seco Tools. - Werkzeugverschleiß überwachen
Durch das Erkennen und Verfolgen von Werkzeugverschleißmustern lassen sich Grundlinien und durchschnittlich zu erwartende Werkzeugstandzeiten für die jeweiligen Anwendungen ermitteln. Veränderungen des Geräuschpegels, der Oberflächenrauheit, übermäßiges Rattern/Vibrieren und erhöhter Stromverbrauch sind ebenfalls Indikatoren für Werkzeugverschleiß. - Lagerverwaltungssystem einführen
Lagerverwaltungssysteme überwachen Lagerort, Verwendung und Verfügbarkeit von Werkzeugen. Werkstattleiter können so nicht nur sicherstellen, dass das richtige Werkzeug für eine Anwendung zur Verfügung steht, sondern auch die Nutzung und den Verbrauch überwachen, um Ausfälle zu vermeiden. - Mitarbeiter schulen
Werkzeuge, Systeme und Verfahren sind nur so gut wie die Menschen, die sie benutzen. Die Weiterbildung des Personals ist für die Optimierung der Werkzeugstandzeit unerlässlich. Das Erkennen und Beseitigen von Verschleißmustern erfordert Erfahrung und eine entsprechende Fachkenntnis.
Wie bereits in Tipp Nr. 7 erwähnt, spielt die Qualifizierung der Arbeitskräfte eine wichtige Rolle beim Erkennen und Verhindern von Werkzeugverschleiß. Glücklicherweise gibt es immer mehr und immer leichter zugängliche Ressourcen zur Mitarbeiterschulung. Seco verfügt über einen umfangreichen Katalog an Online-Kursen,einschließlich eines umfassenden Überblicks über Werkzeugverschleiß und -abnutzung für Werkstattleiter und Bediener , der den Fertigungsbetrieben hilft, ihre Verschleißdaten zu verstehen.
Um Fertigungsbetrieben bei der Diagnose von Werkzeugverschleißproblemen zu helfen, bietet die Funktion Werkzeugoptimierung der Seco Assistant App eine schnelle und einfache Informationsquelle. Die App ermöglicht dem Nutzer, verschiedene Ursachen für Werkzeugverschleiß zu erkennen und diese zu beseitigen, bevor sie zu Problemen führen.
Das Wichtigste:
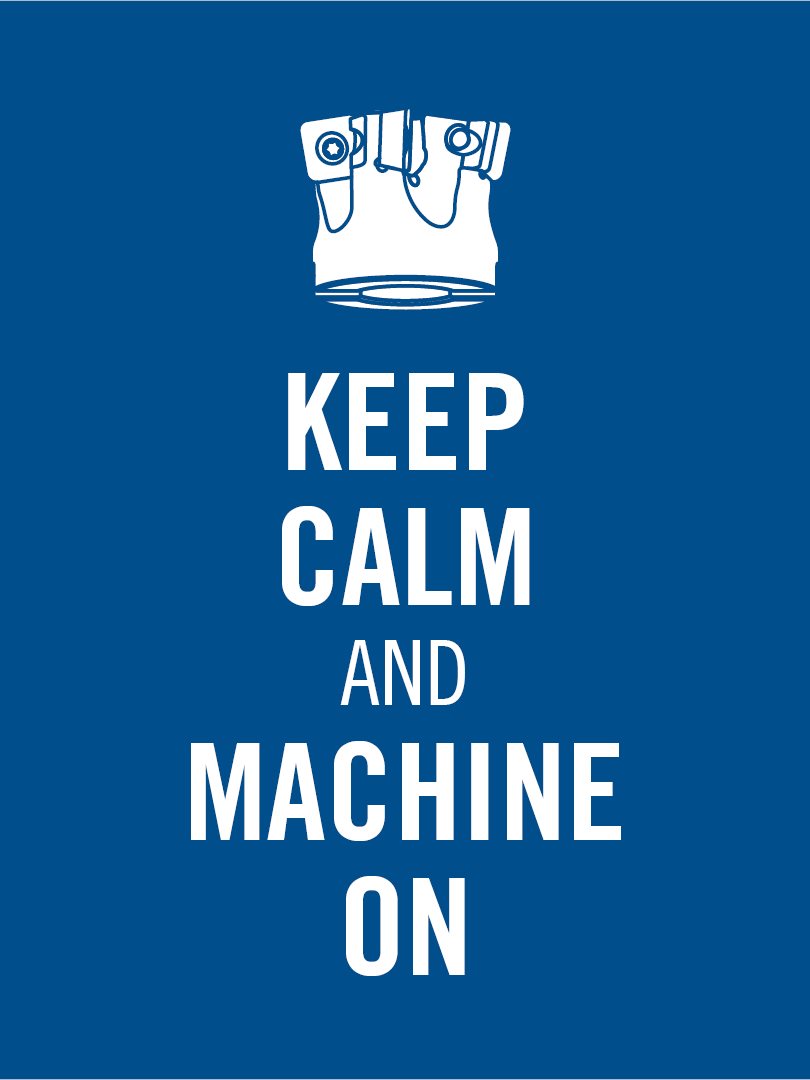