Los expertos de Seco responden a sus preguntas sobre taladrado
Elegir la broca adecuada para su aplicación es esencial para un taladrado sostenible y rentable. Para cualquier duda o consulta sobre geometrías y composición de la broca, o si tiene alguna pregunta sobre recubrimientos o refrigerante, los expertos de Seco estarán encantados de atenderle y buscar la solución que necesita para minimizar el coste por agujero.
ÍNDICE
¿De qué tipo de materiales están hechas las brocas y qué pueden mecanizar?
La composición de una broca puede variar dependiendo de su uso. Generalmente, los materiales de las brocas se dividen en tres categorías.
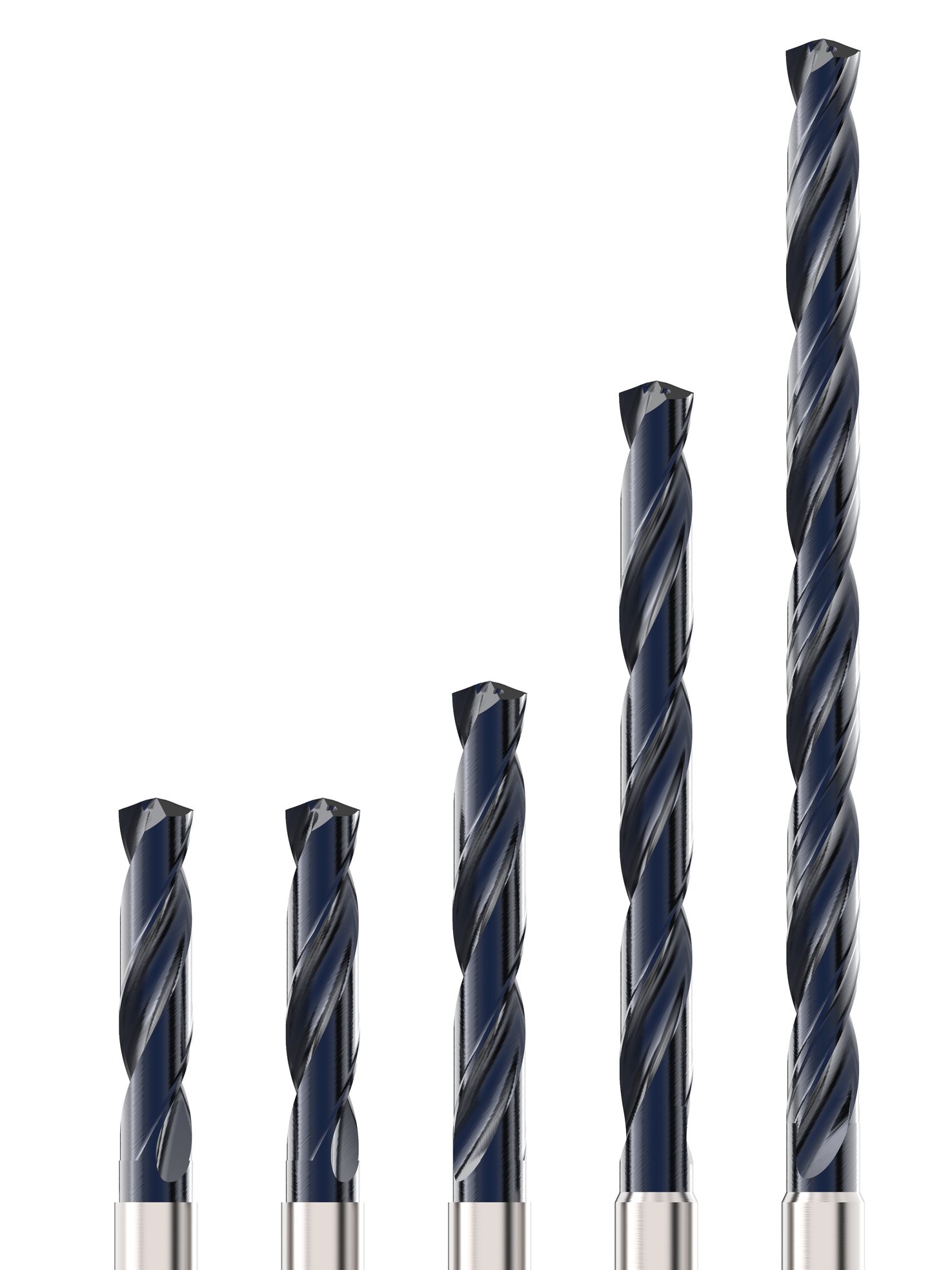
Las brocas HSS son una buena opción para taladrar aceros blandos y plásticos. Son económicos y adaptables para muchas aplicaciones de taladrado.
Gracias al 5-8 % de cobalto añadido, las brocas HCSCO proporcionan propiedades mejoradas de dureza y desgaste, y son adecuadas para taladrar acero, fundición, titanio y otros materiales duros.
Las brocas de metal duro mantienen la arista viva más que cualquier otro material de taladrado y son mejores para los materiales más duros, incluyendo cerámica, composites, acero inoxidable y fundiciones. Por un lado, las brocas de metal duro superan a todos los demás materiales de taladrado, pero por otro son frágiles y más caras.
Las brocas se pueden personalizar prácticamente para cualquier tamaño, dependiendo de la aplicación. Sin embargo, los estándares de la industria han definido los tamaños de brocas que los fabricantes producen con mayor frecuencia.
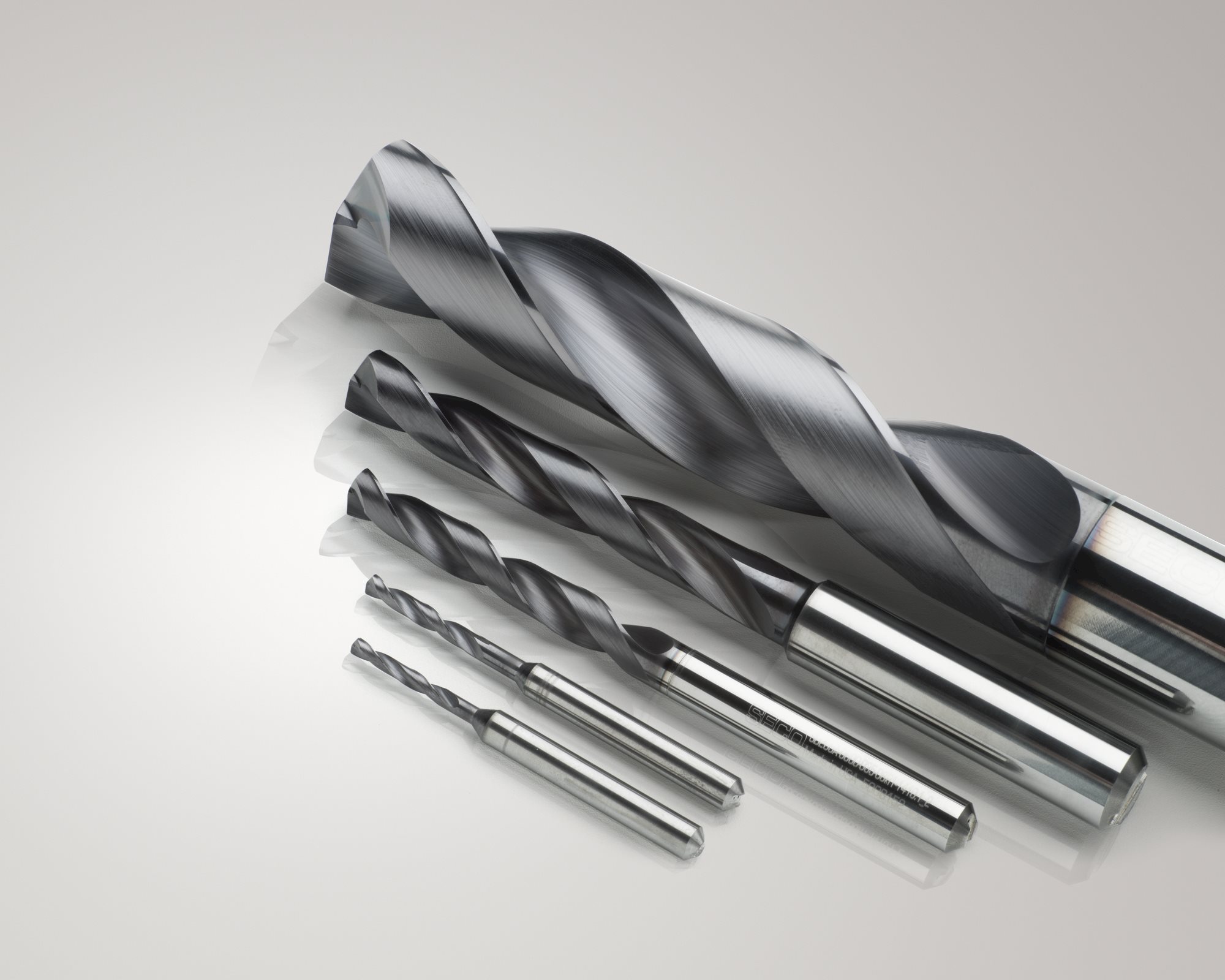
Las longitudes de taladrado también son variables, aunque existen una serie de tipos establecidos:
- Longitud de Jobber: El tipo más común de taladro de uso general realizado para una amplia variedad de trabajos, combinando resistencia y precisión.
- Longitud mecánica: Estas brocas tienen conductos de evacuación de viruta más cortos que las longitudes de Jobber, lo que proporciona una mayor resistencia y rigidez.
- Longitud de la máquina de tornillo: Se trata de las brocas más cortas de entre las brocas estándar, con una mayor rigidez que reduce la deflexión.
- Longitud extendida: Diseñadas para taladrar agujeros profundos, las brocas de longitud extendida incorporan mangos y conductos de evacuación de viruta más largos.
- Longitud cónica: Estas brocas están entre los modelos Jobber y las de longitud extendida en términos de dimensiones.
La geometría de la broca es la compleja relación entre los diversos ángulos y aspectos de la misma. La longitud y el diámetro de la broca, junto con la configuración de sus filos de corte, la geometría de los conductos y el ángulo de la punta, tienen un impacto sobre el rendimiento, la precisión y la vida útil de la herramienta.
Optimizar estas relaciones con la aplicación, los objetivos de producción y la pieza de trabajo es esencial para un proceso de taladrado eficiente y rentable.
Los componentes de la geometría de taladrado a tener en cuenta son:
- Ángulo de la punta: Situado en la zona frontal de la broca, el ángulo de la puntadetermina la desviación, la facilidad de centrado, la conducción de calor y el flujo de viruta.
- Filos de corte principales: Conectados por el borde del cincel, los filosde corte realizan el proceso de cortereal.
- Borde del cincel: Situado en el centro de la punta de la broca. La longitud del borde del cincel determina la cómo de afilada es la broca.
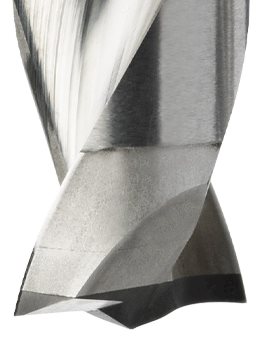
- Perfil de los conductos de evacuación de viruta : Facilita la extracción de virutas y el flujo de refrigerante.
- Guías de contacto: Guía a la broca a medida que avanza por el agujero.
El ángulo de desprendimiento o de hélice es el ángulo entre el filo de ataque de la broca y su eje. Los ángulos de desprendimiento son generalmente disponibles entre 18 y 45 grados, con 30 grados como valor típico. Los ángulos de desprendimiento mayores forman virutas bien enrolladas. Los ángulos de desprendimiento menores tienden a formar virutas que se enrollan más libremente. Los ángulos de desprendimiento también afectan a la temperatura de corte y a la vida útil de la herramienta.
Los ángulos grandes del desprendimiento se emplean generalmente al taladrar materiales más blandos, mientras que los ángulos más pequeños se utilizan para taladrar materiales duros que generavirutas más pequeñas y más cortas.
El DIN 1836 aborda los ángulos de hélice con tres grupos:
- Tipo N : Hélice normal para materiales con dureza normal, como meteriales no férricos y fundiciones. Las hélices de tipo N no son adecuadas para materiales más blandos.
- Tipo H : Hélices más largas para materiales frágiles como acero, plásticos duros y laminados.
- Tipo W: Hélice en espiral que genera virutas largas y onduladas en plásticos blandos y metales.
Los filos de corte de una broca están conectados por el filo del cincel y son responsables del proceso de taladrado real. Los filos de corte largos proporcionan un mejor rendimiento en el proceso de taladrado.
Encuentre la broca adecuada con nuestra guía El objetivo de las aplicaciones de mecanizado, incluida la de mecanizado de agujeros, es mantener bajos costes operativos y de herramientas y un alto rendimiento. Si bien muchos fabricantes consideran cuidadosamente las herramientas que utilizan para fresar y tornear, es posible que no traten la selección de herramientas de mecanizado de agujeros como una decisión igualmente crítica. Consejos y trucos son siempre bienvenidos. Más información aquí |
¿Qué recubrimientos de broca están disponibles y cuáles son los mejores para una aplicación determinada?
Hay una variedad de recubrimientos disponibles para brocas, cada uno de ellos con ventajas específicas y más apropiado que otro para aplicaciones específicas. En la mayoría de preguntas sobre selección de herramientas, predominan respuestas teniendo en cuenta primero la operación y las piezas de trabajo. Los recubrimientos de brocas también prolongan la vida útil de la herramienta, reduciendo así el coste total por agujero.
Los recubrimientos generalmente se aplican a los filos de corte de taladrado a través de un proceso llamado Deposición Física de Vapor (PVD). PVD utiliza un proceso físico como el calentamiento o la pulverización para producir un vapor de material que luego se deposita en el objeto a recubrir.
Los recubrimientos de taladrado más comunes son:
- TiN, o nitruro de titanio, compuesto de titanio y nitrógeno que se ha demostrado que duplicar e incluso cuadruplicar la vida útil de la herramienta para un taladrado de uso general.
- TiAIN, o nitruro de aluminio de titanio, que puede extender la vida útil de la herramienta hasta 10 veces y ofrece una excelente resistencia al calor y a la oxidación. Adecuado para aceros aleados e inoxidables a velocidades de corte medias a altas.
- TiCN, o carbonitruro de titanio, proporciona muy alta dureza y resistencia al desgaste y puede extender la vida útil de la herramienta hasta cinco veces más que las herramientas sin recubrimiento. Funciona mejor en aleaciones de bronce y cobre, así como en aleaciones de bronce y níquel de aluminio.
- AltIn, o nitruro de titanio de aluminio ofrece una dureza superior para aplicaciones de alta temperatura al taladrar piezas muy duras o abrasivas.
Sin embargo, la principal desventaja de las brocas recubiertas es que a veces no se pueden reafilar.
¿Qué tipo de refrigerantes están disponibles y cómo debo utilizarlos?
El refrigerante y la lubricación durante el proceso de taladrado mejoran significativamente la vida útil de la herramienta, la evacuación de virutas y la calidad del agujero, especialmente en piezas difíciles como aceros aleados o inoxidables. La reducción del calor es aún más importante en las operaciones de taladrado porque la mayor parte de la energía se transforma en calor. En brocas con múltiples guias de contacto tienen más contacto entre la superficie del agujero y la herramienta, lo que hace que el control del calor resulte aún más importante.
Hay varios tipos diferentes de refrigerante disponibles y la selección depende de la aplicación. Entre ellos se encuentran:
- Aceites de corte puros: También conocidos como aceites limpios, los aceites de corte son 100 % petróleo o aceite mineral utilizado en brochado, roscado y taladrado de agujeros profundos. Son especialmente adecuados para el taladrado de súper aleaciones y acero inoxidable.
- Aceite de corte soluble en agua: Aunque carece de la lubricidad de los aceites puros, el aceite soluble es más versátil y se puede utilizar en una amplia variedad de aplicaciones de acabado a semi acabado..
- Fluidos sintéticos y semisintéticos: Proporcionan refrigeración y lubricación para el taladrado de alta velocidad en aplicaciones semi desbaste a desbaste.
Siempre se recomienda refrigerante interno para procesos de taladrado y es la mejor opción para materiales de trabajo duros, como aleaciones superaleadas y acero inoxidable. Para una refrigeración interna eficaz, las herramientas de refrigeración directa cuentan con conductos de refrigeración que dirigen el refrigerante directamente a la zona de corte.
Si se utiliza refrigerante externo, es importante asegurarse de que el flujo de refrigerante sea dirigido lo más paralelo posible a la broca a medida que llega a la zona de corte. Para una evacuación aceptable de la viruta, la profundidad máxima recomendada de taladrado con refrigerante externo no debe ser de más del triple de diámetro y reducir la velocidad de corte en un 20% en comparación con las operaciones con refrigerante interno.
¿Cuáles son los problemas y soluciones más comunes en materia de taladrado?
Aunque puedan surgir cualquier tipo de problemas, de largo el más preocupante es la rotura de la broca. Obviamente, las herramientas rotas tienen que ser reemplazadas implicando un gasto de tiempo y costes, a la vez que aumentan el riesgo de piezas rechazadas y residuos.
Algunas causas de rotura de la broca son:
- Velocidad incorrecta: Las brocas de gran diámetro funcionan a velocidades más bajas que las brocas de pequeño diámetro. Un taladrado demasiado rápido o demasiado lento puede provocar que las brocas se atasquen y se rompan. La dureza de la pieza de trabajo también determina la velocidad de taladrado. Consulte las tablas del fabricante para saber la velocidad correcta.
- Presión excesiva en la parte inferior de un agujero ciego: la acumulación de virutas en la parte inferior de un agujero ciego debido a una evacuación insuficiente puede causar la rotura de la broca. Reduzca la presión a medida que se acerque al fondo.
- Conductos obstruidos: Cuando los conductos de evacuación de virutas se obstruyen con virutas y éstas no son evacuadas correctamente, la broca puede atascarse en el agujero y romperse. Opte por una broca con conductos más anchos y/o retire la broca a intervalos regulares.
- Geometría de la punta taladrado inadecuada para la aplicación: se requieren ángulos de punta diferentes dependiendo de la dureza de la pieza de trabajo. Consulte las tablas de fabricación para conocer el ángulo de punta correcto para su aplicación.
- Avance excesivo: si se superan los avances recomendados, se rompen los filos de corte y la punta de la broca, lo que provoca la fragmentación o incluso la rotura de la ésta. Reduzca el avance para aliviar la presión de taladrado.
Un taladrado eficiente requiere minimizar el coste por agujero. Las brocas con un desgaste demasiado rápido provoca tiempos muertos para cambiar las herramientas, lo que aumenta el coste por agujero. Para evitar cambiar las herramientas con demasiada frecuencia:
- Revise el refrigerante para asegurarse de que está llegando al punto de corte.
- Revise los parámetros de velocidad y avance.
- Utilice la herramienta adecuada para su operación: la broca y la geometría de la punta adecuados para su aplicación específica pueden marcar la diferencia.
Los filos astillados no generan agujeros de calidad. Las virutas en el filo pueden deberse a:
- Salto excesivo/amarre débil.
- Velocidades y avances excesivos/incorrectos.
- No utilizar o utilizar de forma inadecuada el refrigerante.
Las virutas que no se rompen se vuelven más largas y con hebras, lo que implica interrupciones de trabajo para desenrollarlas de la herramienta. Para un control efectivo de la viruta:
- Incrementar el avance.
- Examinar la broca comprobando que no este desgastada.
- Considere la posibilidad de cambiar a una geometría de punta diferente.
¿Cuáles son los consejos y trucos más comunes en materia de taladrado?
Siga estas directrices generales para un taladrado rentable y sostenible.
Las brocas más cortas disminuyen la capacidad de desviación de la broca de su punto de partida durante el proceso de taladrado. Como resultado, las brocas más cortas proporcionan una mayor precisión. Debido a que son más robustas, es menos probable que se rompan y son más fáciles de usar en áreas localizadas.
Una geometría con autocentraje de la broca permite una colocación precisa de los agujeros, eliminando la necesidad de herramientas de alineación adicionales o de un ajuste excesivo. La broca se centra automáticamente dentro del punto de partida, asegurando que el agujero esté perfectamente posicionado según los requisitos de la pieza. Las brocas autocentrables ahorran tiempo, simplifican los ajustes y reducen el coste por agujero.
Utilice brocas diseñadas para priorizar el taladrado seguro y mantener la posición durante todo el proceso de taladrado para minimizar movimientos o desviaciones no deseados. La estabilidad es fundamental para lograr resultados precisos y consistentes, especialmente cuando se trabaja en piezas delicadas y complejas donde la precisión es primordial.
La evacuación eficiente de virutas y la prevención de la acumulación de virutas son esenciales para un taladrado suave y maximizar la productividad. La evacuación adecuada de la viruta reduce los tiempos muertos, mejora el rendimiento de taladrado y promueve la productividad general en el proceso de mecanizado.
Para el taladrado de agujeros profundos, con brocas largas por encima de los 16xD, será necesario una broca piloto. Taladrar primero un agujero previos eliminará parte del material de la pieza de trabajo y reducirá la fuerza necesaria para mecanizar el agujero final. Los agujeros guía reducen el descentramiento del agujero y garantizan la máxima precisión.
Si va a taladra en una superficie en ángulo, se recomienda mecanizar en plano utilizando una fresa de metal duro mediante el método de interpolación. Si existe un agujero pretaladrado, reduzca el avance en un 50 % hasta que la broca haya alcanzado el acceso del diámetro completo al agujero. Utilice una broca con múltiples guias de contacto y reduzca el avance entre un 30 y un 50 % durante la salida.
Para taladrar agujeros pasantes, reduzca el avance en un 50 % hasta 3 mm antes del cruce y mantenga esa bajo avance hasta 3 mm después de pasar el agujero pasante. Si es posible, utilice una broca múltiples guias de contacto para mejorar la guía.
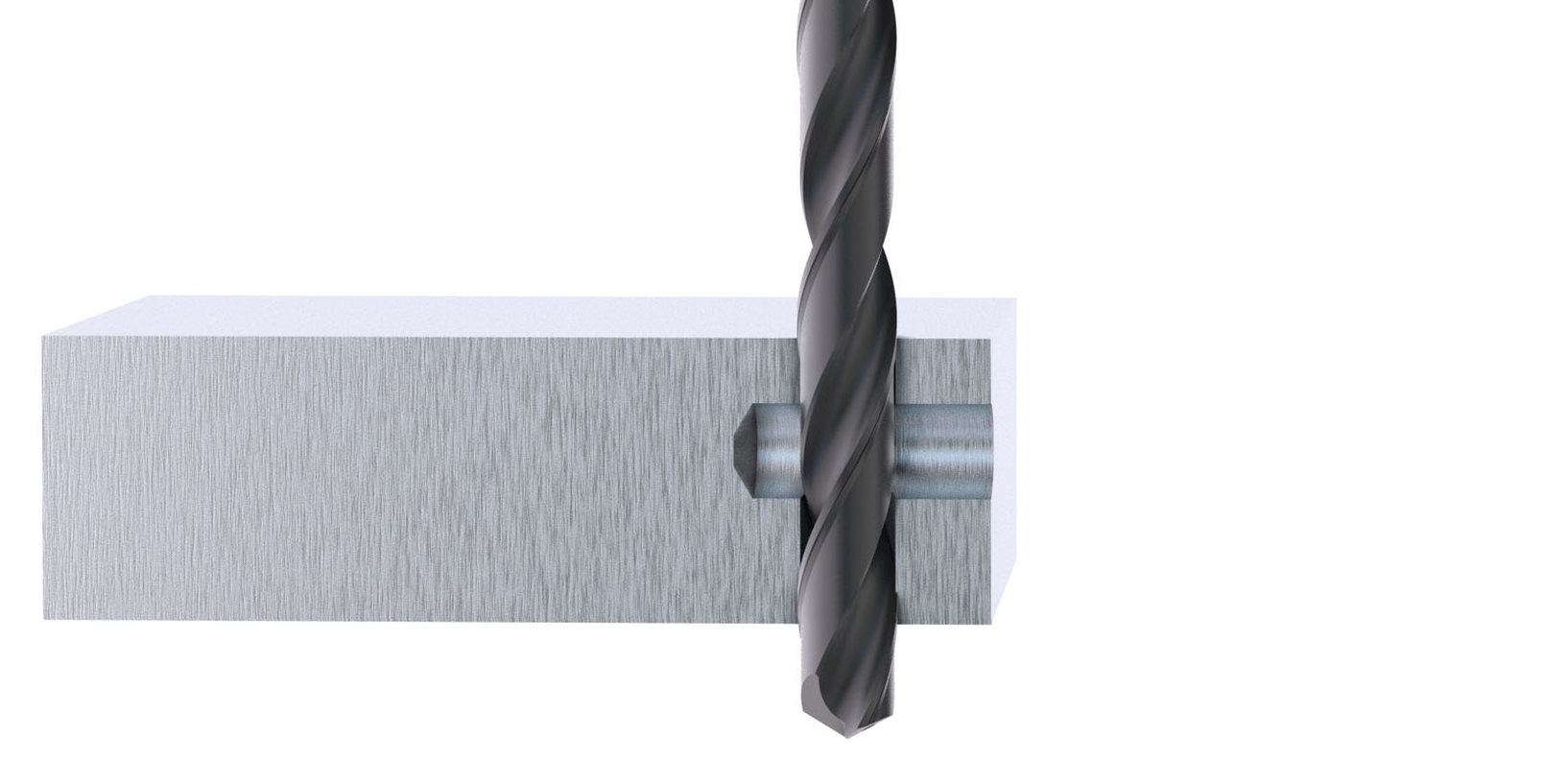
Los materiales apilados se pueden taladrar eficazmente siempre y cuando las piezas de trabajo estén sujetas de forma segura para que no haya espacios de aire entre ellas. Los espacios de aire tienen un efecto perjudicial en la evacuación de las virutas y pueden causar daños a la broca.
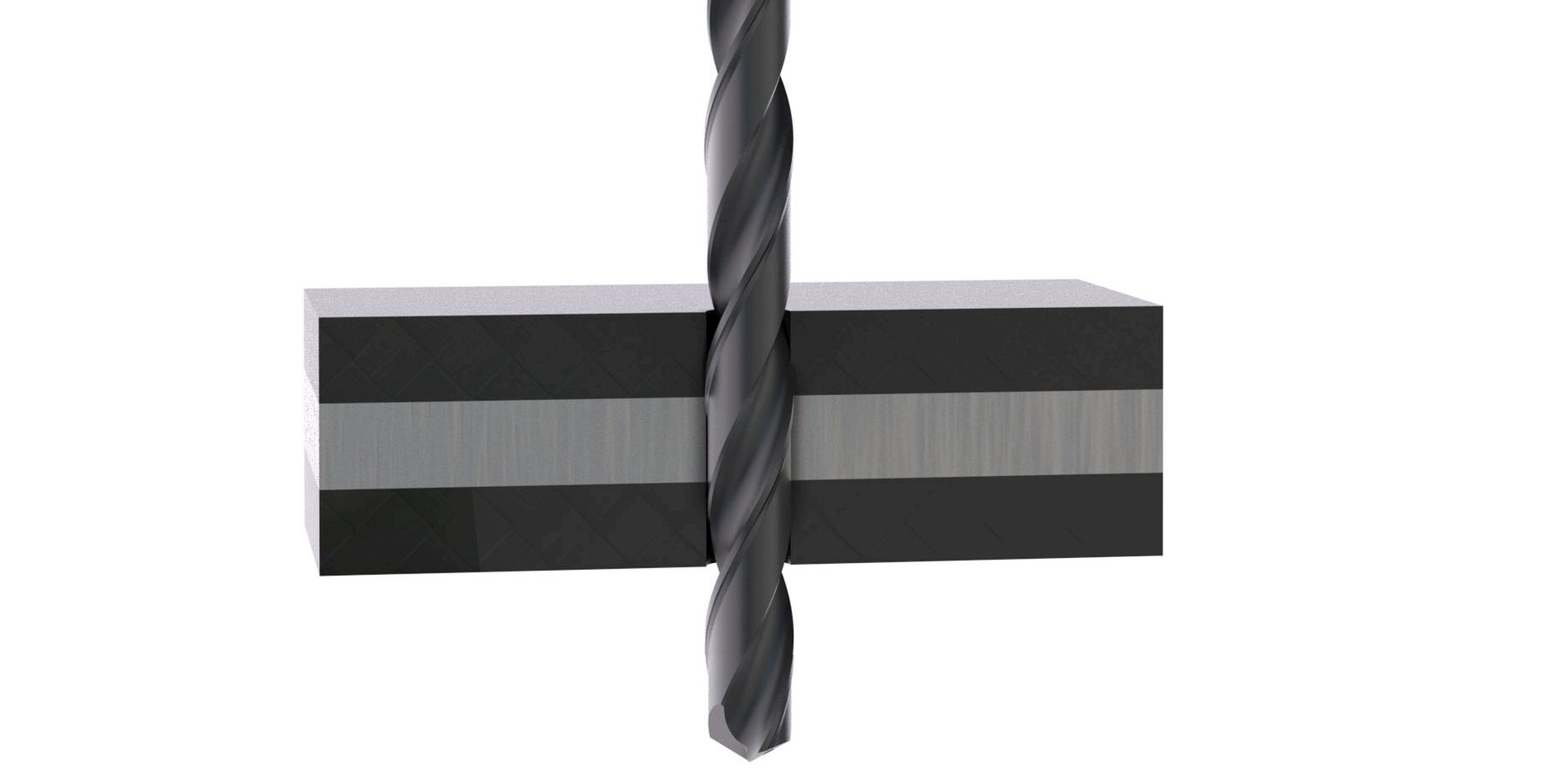
Elegir la mejor herramienta para una aplicación determinada implica considerar un mayor número de aspectos. Además de las geometrías de broca universales versátiles y adaptables a las cambiantes aplicaciones y necesidades de un proceso de producción, la selección de una broca con las características, dimensiones, recubrimientos y características de corte adecuadas afectará directamente a su rendimiento.
Para un proceso de taladrado sostenible con el coste por agujero más eficiente, contacte con un experto de Seco quien le ayudará a encontrar la herramienta adecuada para su trabajo o realice una Consulta.