Seco'nun uzmanları delik işleme ile ilgili sorularınızı yanıtlıyor
Uygulamanız için doğru matkabı seçmek, sürdürülebilir ve uygun maliyetli delik işleme uygulamaları için çok önemlidir. Matkap geometrisi ve kompozisyonu, kaplamalar veya soğutma sıvısı hakkında sorularınız olsun, Seco uzmanları delik başına maliyetinizi en aza indirecek ihtiyacınız olan cevaplara sahiptir.
İçindekiler
Matkaplar ne tür malzemelerden yapılmıştır ve neleri işleyebilirler?
Bir matkabın bileşimini seçmek, kullanımına bağlı olarak değişecektir. Genel olarak, matkap ucu malzemeleri üç kategoride mevcuttur.
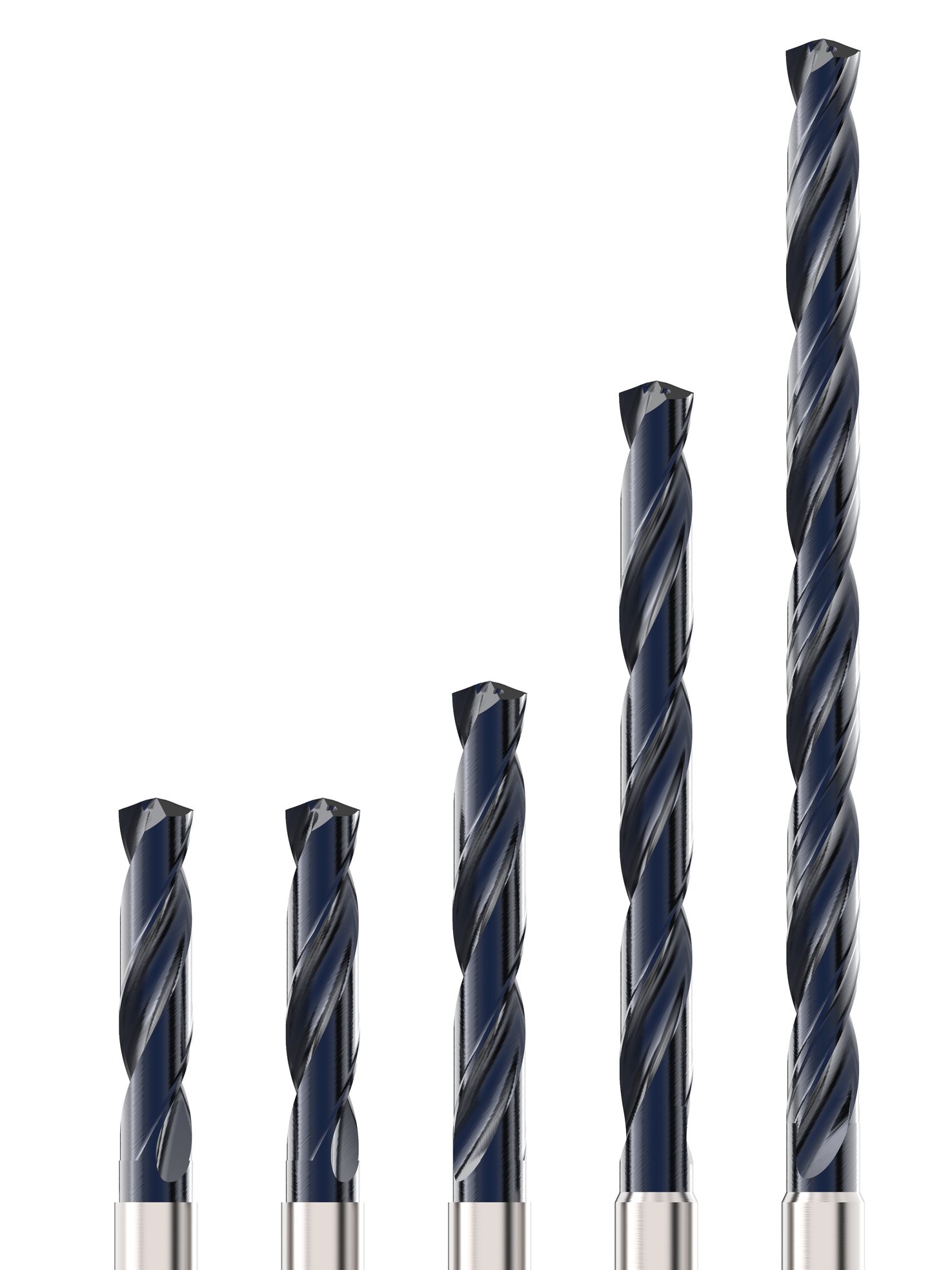
HSS matkaplar yumuşak çelikler ve plastikler için iyi bir seçimdir. Bunlar ekonomik ve birçok delme uygulaması için uyarlanabilir.
%5-8'lik kobalt ilavesi ile HCSCO matkaplar daha iyi sertlik ve aşınma özellikleri sağlar ve çelik, dökme çelik, titanyum ve diğer sert malzemeleri delmek için uygundur.
Karbür matkaplar keskinliği diğer tüm matkap malzemelerinden daha fazla korur ve seramik, cam, paslanmaz çelik ve dökme demir gibi en sert malzemeler için en iyisidir. Diğer tüm matkap malzemelerinden daha iyi performans gösterirken, karbür matkaplar kırılgan ve daha pahalıdır.
Matkaplar uygulamaya bağlı olarak hemen hemen her boyutta özel olarak yapılabilir. Bununla birlikte, endüstri standartları, en çok matkap üreticileri tarafından üretilen tanımlanmış matkap boyutlarını belirlemiştir.
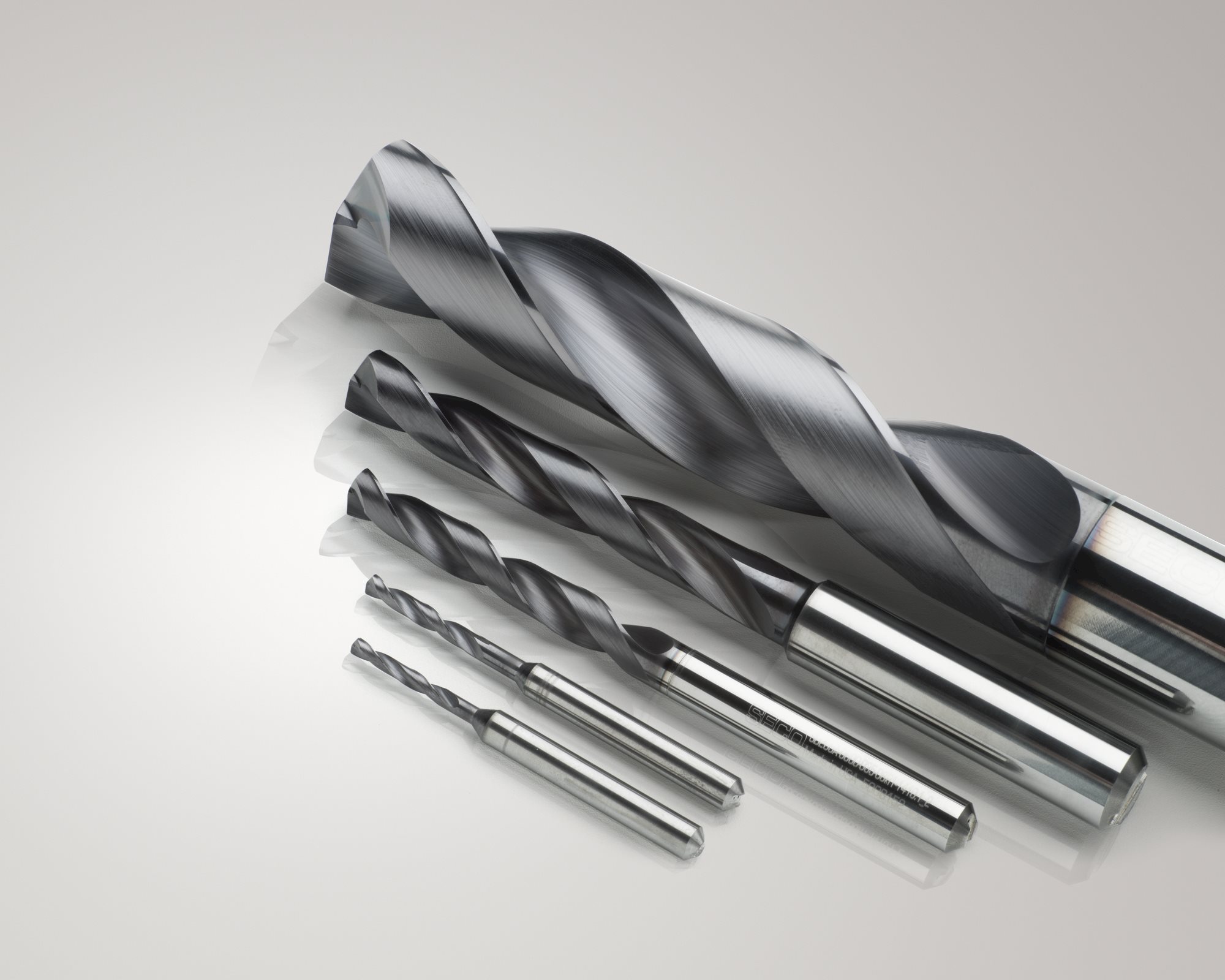
Delme uzunlukları da değişkendir, ancak tanımlanmış tipler vardır:
- İş Uzunluğu – çok çeşitli işler için yapılan, güç ve doğruluğu birleştiren en yaygın genel amaçlı matkap türüdür.
- Mekanik Uzunluğu – bu matkaplar, iş uzunluklarından daha kısa oluklara sahiptir ve daha fazla güç ve sertlik sağlar.
- Vida makinesi uzunluğu – bunlar, sapmayı azaltan daha sertliğe sahip standart matkap uçlarının en kısasıdır.
- Uzatılmış uzunluk – derin delikler açmak için tasarlanmıştır, uzatılmış uzunluktaki matkaplar uzun şaftlar ve yivler içerir.
- Koniklik Uzunluğu – bu matkaplar, boyut açısından işveren ve uzatılmış uzunluk uçları arasında yer alır.
Matkap geometrisi, matkabın çeşitli açıları ve yönleri arasındaki karmaşık ilişkidir. Matkabın uzunluğu ve deliği, kesici kenarlarının yapılandırması, oluk profili ve nokta açısı, performansı, doğruluğu ve takım ömrünü etkiler.
Bu ilişkileri uygulama, üretim hedefleri ve iş parçasıyla optimize etmek, verimli ve uygun maliyetli delme için çok önemlidir.
Göz önünde bulundurulması gereken delme geometrisi bileşenleri şunlardır:
- Nokta açısı – Matkap ucunun başında bulunan nokta açısı, dolaşmayı, merkezleme kolaylığını, ısı iletimini ve talaş akışını belirler.
- Ana kesici kenarlar – Keski kenarı ile bağlanan kesici kenarlar gerçek delme işlemini gerçekleştirir.
- Keski kenarı – Matkap ucunun ortasında bulunan keski kenarı uzunluğu, matkabın keskinliğini belirler.
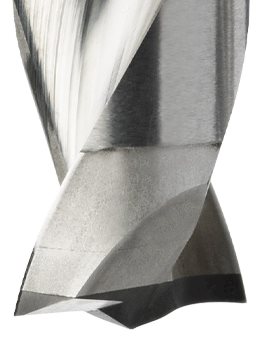
- Kanal profili – talaş tahliyesini ve soğutma sıvısı akışını kolaylaştırır.
- Kılavuz Topraklar – delme deliğinden geçerken matkabı yönlendirin.
Bir matkabın tırmığı veya sarmal açısı, matkabın ön kenarı ve ekseni arasındaki açıdır. Tırmık açıları genellikle 18 ile 45 derece arasında bulunur ve 30 derece tipik değerdir. Daha yüksek tırmık açıları sıkıca yuvarlanmış talaşlar oluşturur. Daha düşük tırmık açıları, daha gevşek yuvarlanan talaşlar oluşturma eğilimindedir. Tırmık açıları kesme sıcaklığını ve takım ömrünü de etkiler.
Büyük tırmık açıları genellikle daha yumuşak malzemeler delerken kullanılırken, daha küçük ve daha kısa talaşlar üreten sert malzemeler delerken daha küçük açılar kullanılır.
Din 1836 sarmal açıları üç grupla ele alır:
- Tip N – Demir dışı metaller ve dökme demir gibi normal sertliğe sahip malzemeler için normal sarmal. N tipi sarmallar daha yumuşak malzemeler için uygun değildir.
- H Tipi – Çelik, sert plastikler ve laminatlar gibi kırılgan malzemeler için daha uzun çizilmiş sarmallar.
- Tip W – yumuşak plastiklerde ve metallerde uzun, kıvırcık taüreten sıkıca spiral sarmal.
Bir matkabın kesici kenarları keski kenarı ile bağlanır ve gerçek delme işleminden sorumludur. Uzun kesici kenarlar delme işleminde daha iyi performans sağlar.
Kılavuzumuz/teknik raporumuz ile doğru Matkabı bulun Delik açma da dahil olmak üzere metal kesme uygulamalarının amacı, takım ve işletme maliyetlerini düşük tutmak ve yüksek çıktı elde etmektir . Birçok üretici, frezeleme ve tornalama için kullandıkları takımları dikkatli bir şekilde değerlendirirken, delik açma takımlarının seçimini eşit derecede kritik bir karar olarak ele almayabilir, ancak öyledir.. İpuçları ve püf noktaları her zaman memnuniyetle karşılanır. Buradan daha fazla bilgi edinin |
Hangi matkap kaplamaları mevcuttur ve belirli bir uygulama için hangileri en iyisidir?
Matkaplar için her biri belirli avantajlara sahip ve belirli uygulamalar için diğerlerinden daha uygun olan çeşitli kaplamalar mevcuttur. Çoğu takım seçimi sorusunda olduğu gibi, en iyi cevap öncelikle işlem ve iş parçası tarafından yönlendirilir. Delme kaplamaları ayrıca takım ömrünü uzatarak delik başına toplam maliyeti azaltır.
Kaplamalar genellikle fiziksel buhar biriktirme (PVD) adı verilen bir işlemle kesici kenarları delmek için uygulanır. PVD, daha sonra kaplanan nesne üzerinde biriken bir malzeme buharı üretmek için ısıtma veya püskürtme gibi fiziksel bir işlem kullanır.
En yaygın matkap kaplamaları şunlardır:
- Kalay veya titanyum nitrür, genel amaçlı delme için iki ve hatta dört kat takım ömrü gösterdiği gösterilen titanyum ve nitrojenden oluşur.
- TiAIN veya titanyum alüminyum nitrür, alet ömrünü 10 kata kadar uzatabilir ve mükemmel ısı ve oksidasyon direnci sunar. Orta ve yüksek kesme hızlarında alaşımlı ve paslanmaz çelikler için uygundur.
- TiCN veya titanyum karbonitrür, çok yüksek sertlik ve aşınma direnci sağlar ve takım ömrünü kaplanmamış aletlerin beş katına kadar uzatabilir. En iyi bronz ve bakır alaşımlarının yanı sıra alüminyum bronz ve nikel alaşımları üzerinde çalışır.
- Altın veya alüminyum titanyum nitrür , çok sert veya aşındırıcı iş parçaları delme sırasında yüksek sıcaklık uygulamaları için üstün sertlik sunar.
Bununla birlikte, kaplamalı matkapların birincil dezavantajı, bazen yeniden şekillendirilememesidir.
Ne tür soğutma sıvıları mevcuttur ve bunları nasıl kullanmalıyım?
Delme işlemi sırasında soğutma sıvısı ve yağlama, özellikle alaşımlı veya paslanmaz çelikler gibi zorlu iş parçalarında takım ömrünü, talaş tahliyesini ve delik kalitesini önemli ölçüde artırır. Delme işlemlerinde ısı azaltma daha da önemlidir, çünkü enerjinin çoğu ısıya dönüşür. Birden çok alan marjına sahip matkaplarda, delik yüzeyi ile takım arasında daha fazla temas vardır ve bu da ısı kontrolünü daha da önemli hale getirir.
Birkaç farklı tipte soğutma sıvısı mevcuttur ve seçim uygulamaya bağlıdır. Bunların arasında şunlar vardır:
- Düz kesme yağları – temiz yağlar olarak da bilinen kesme yağları, broş, dokunma ve derin delik delmede kullanılan% 100 petrol veya mineral yağdır. Özellikle süper alaşımlar ve paslanmaz çelik delmek için uygundurlar.
- Suda çözünür kesme yağı – temiz yağların yağından yoksun olmasına rağmen, çözünür yağ daha çok yönlüdür ve çok çeşitli hafif ila orta menzilli uygulamalarda kullanılabilir.
- Sentetik ve yarı sentetik sıvılar – orta ve ağır uygulamalarda yüksek hızlı delme için soğutma ve yağlama sağlar.
İçten soğutma sıvısı delme için her zaman önerilir ve süper alaşımlar ve paslanmaz çelik gibi zorlu çalışma malzemeleri için en iyi seçenektir. Etkili içten soğutma için, soğutma araçlarında soğutma sıvısını doğrudan kesme bölgesine yönlendiren soğutma kanalları bulunur.
Dıştan soğutma sıvısı kullanılıyorsa soğutma sıvısı akışının kesme alanına ulaşırken matkaba mümkün olduğunca paralel şekilde yönlendirilmesini sağlamak önemlidir. Kabul edilebilir talaş tahliyesi için harici soğutma sıvısı kullanarak önerilen maksimum delme derinliği 3 kat çaptan fazla olmamalı ve dahili soğutma sıvısı kullanan işlemlere kıyasla kesme hızını %20 azaltmalıdır.
Yaygın delik işleme sorunları ve çözümleri nelerdir?
Ortaya çıkan herhangi bir sayıda sorun olsa da, en çok ilgili olan matkap kırılmasıdır. Kırılan takımların zaman ve para pahasına değiştirilmesi gerekir, ancak hurdaya çıkarılan parçalar ve atık riskini de artırırlar.
Matkap kırılmasının bazı nedenleri şunlardır:
- Uygun olmayan hız – büyük çaplı matkaplar, küçük çaplı matkaplara göre daha düşük hızlarda çalışır. Çok hızlı veya çok yavaş delme, matkapların bağlanmasına ve kırılmasına neden olabilir. İş parçasının sertliği delme hızını da belirler. Doğru hız için üretici tablolarına başvurun.
- Kör bir deliğin dibinde aşırı basınç – yetersiz çıkarma nedeniyle kör bir deliğin dibinde talaş birikmesi kırılmaya neden olabilir. Alt kısma yaklaşırken basıncı azaltın.
- Tıkanmış kanallar – Kanallar talaşlarla tıkandığında, düzgün bir şekilde tahliye edilmezler ve bu da ucun deliğe sıkışmasına ve kırılmasına neden olur. Daha geniş ağızlı bir matkap seçin ve/veya matkabı düzenli aralıklarla çekin.
- Uygulama için uygun olmayan delme noktası – iş parçasının sertliğine bağlı olarak farklı nokta açıları gerekir. Uygulamanız için doğru nokta açısı için üretim tablolarına başvurun.
- Aşırı ilerleme hızı – önerilen ilerleme hızlarının aşılması, kesme kenarlarını ve delme noktasını parçalayarak bölünmeye veya kırılmaya neden olur. Delme basıncını azaltmak için ilerleme hızını azaltın.
Verimli delme, delik başına maliyeti en aza indirmeyi gerektirir. Çok hızlı aşınan matkaplar, takımları değiştirmek için arıza süresi gerektirir ve bu da delik başına maliyeti artırır. Takımların çok sık değiştirilmesini önlemek için:
- Kesme noktasına ulaştığından emin olmak için soğutma suyunu kontrol edin.
- Hız ve ilerleme parametrelerini inceleyin.
- İş için doğru takımı kullanın – özel uygulamanız için uygun matkap ve nokta geometrisi fark yaratabilir.
Yontulmuş kesici kenarlar kaliteli bir delik açmaz. Kesici kenardaki talaşlar şunlardan kaynaklanabilir:
- Aşırı aşınma/gevşek mandren.
- Aşırı/uygun olmayan hızlar ve ilerlemeler.
- Kesme sıvısının kullanılmaması veya yetersiz kullanımı.
Kırılamayan talaşlar uzun ve gergin hale gelir ve bunları takımdan çıkarmak için iş kesintileri gerektirir. Talaşları kontrol altında tutmak için:
- İlerleme oranını artırın
- Keskin olduğundan emin olmak için matkabı inceleyin.
- Farklı bir matnoktası geometrisine geçmeyi düşünün.
Bazı yaygın delik işleme ipuçları ve püf noktaları nelerdir?
Uygun maliyetli, sürdürülebilir delik işlemleri için bu genel yönergeleri izleyin.
Daha kısa matkap uçları, matkabın delme işlemi sırasında başlangıç noktasından dolaşma veya sapma yeteneğini azaltır. Sonuç olarak, daha kısa matkap uçları daha fazla doğruluk sağlar. Daha sert olduklarından, kırılma olasılıkları daha düşüktür ve sınırlı alanlarda kullanımı daha kolaydır.
Kendiliğinden ortalanan matkap geometrisi, hassas ve doğru delik yerleşimi sağlayarak ek hizalama takımları veya aşırı ayarlama ihtiyacını ortadan kaldırır. Matkap, başlangıç noktası içinde otomatik olarak merkezlenir ve deliğin parça gereksinimlerine mükemmel şekilde konumlandırılmasını sağlar. Kendiliğinden ortalanan matkaplar zaman kazandırır, kurulumları kolaylaştırır ve delik başına maliyeti azaltır.
İstenmeyen hareket veya sapmaları en aza indirmek için güvenli delme ve delme işlemi boyunca konumu korumak için tasarlanmış matkapları kullanın. Kararlılık, özellikle hassasiyetin çok önemli olduğu hassas ve karmaşık parçalar üzerinde çalışırken doğru ve tutarlı sonuçlar elde etmek için kritik öneme sahiptir.
Sorunsuz delme ve üretkenliği en üst düzeye çıkarmak için verimli talaş tahliyesi ve talaş birikmesini önleme çok önemlidir. Doğru talaş tahliyesi arıza süresini azaltır, delme performansını artırır ve işleme sürecinde genel üretkenliği artırır.
Derin delik delme ve 16 XD'yi aşan uzun matkaplar için pilot matkap gerekli olacaktır. İlk önce bir pilot delik açmak, malzemenin bir kısmını iş parçasından çıkarır ve son deliği üretmek için gereken kuvveti azaltır. Pilot delikler delik salgısını azaltır ve maksimum doğruluk sağlar.
Açılı bir yüzeye delme işlemi yapıyorsanız, interpolasyon yöntemiyle katı bir uç freze kullanarak düz bir tezgah kullanın. Frezeleme mümkün değilse matkap tam kesime ulaşana kadar delme beslemesini %50 azaltın. Birden fazla arazi marjına sahip bir matkap kullanın ve çıkış sırasında besleme oranını %30 ila %50 azaltın.
Çapraz delikler açmak için geçişten önce beslemeyi %50 3 mm azaltın ve geçiş deliğinden geçtikten sonra 3 mm'ye kadar düşük besleme oranını koruyun. Mümkünse, yönlendirmeyi iyileştirmek için birden fazla kara marjı delme kullanın.
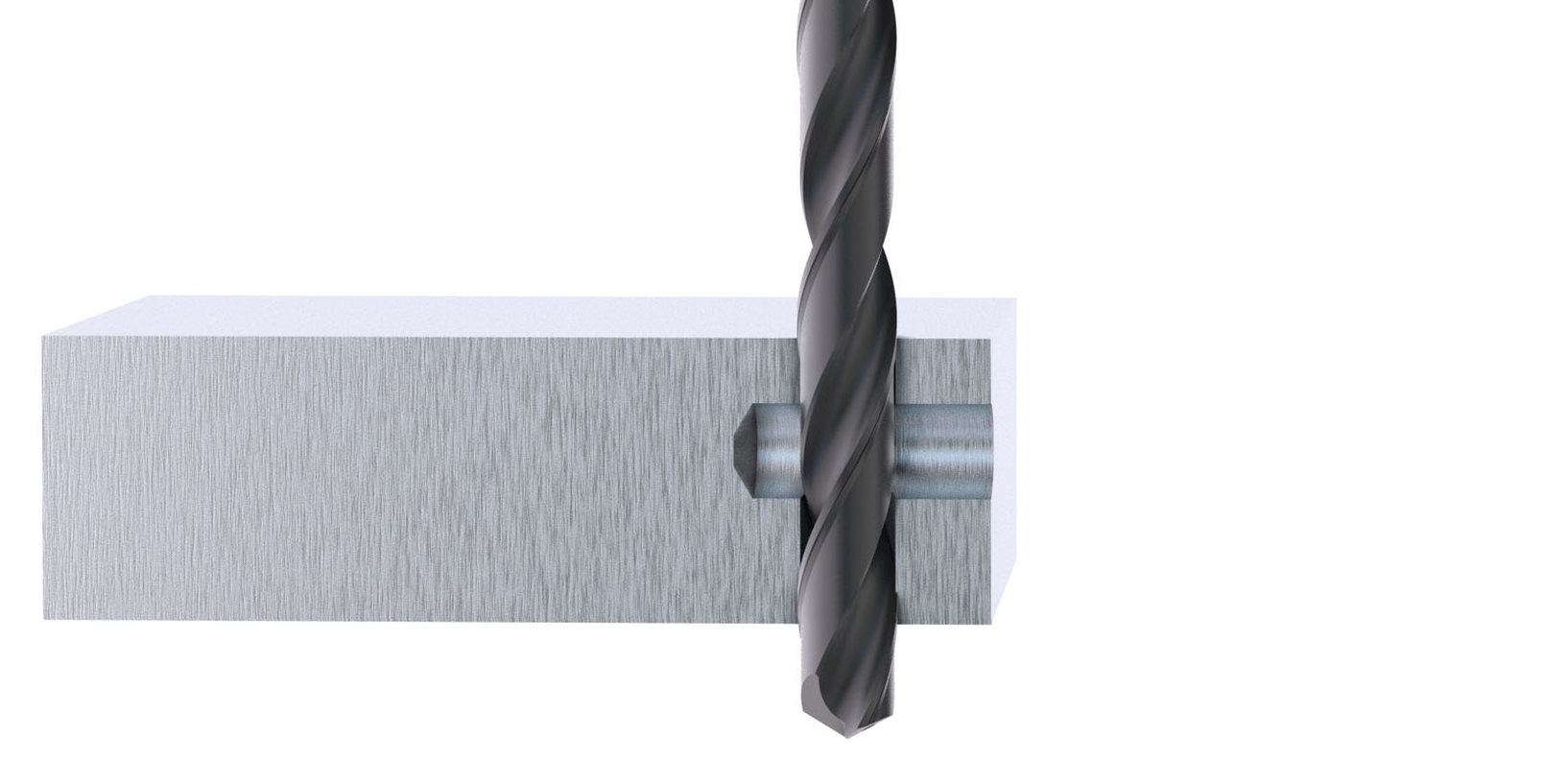
Yığılmış malzemeler, iş parçaları güvenli bir şekilde kenetlendiği sürece etkili bir şekilde delinebilir, böylece aralarında hava boşluğu olmaz. Hava boşlukları talaş tahliyesi üzerinde zararlı bir etkiye sahiptir ve matkap hasarına neden olur.
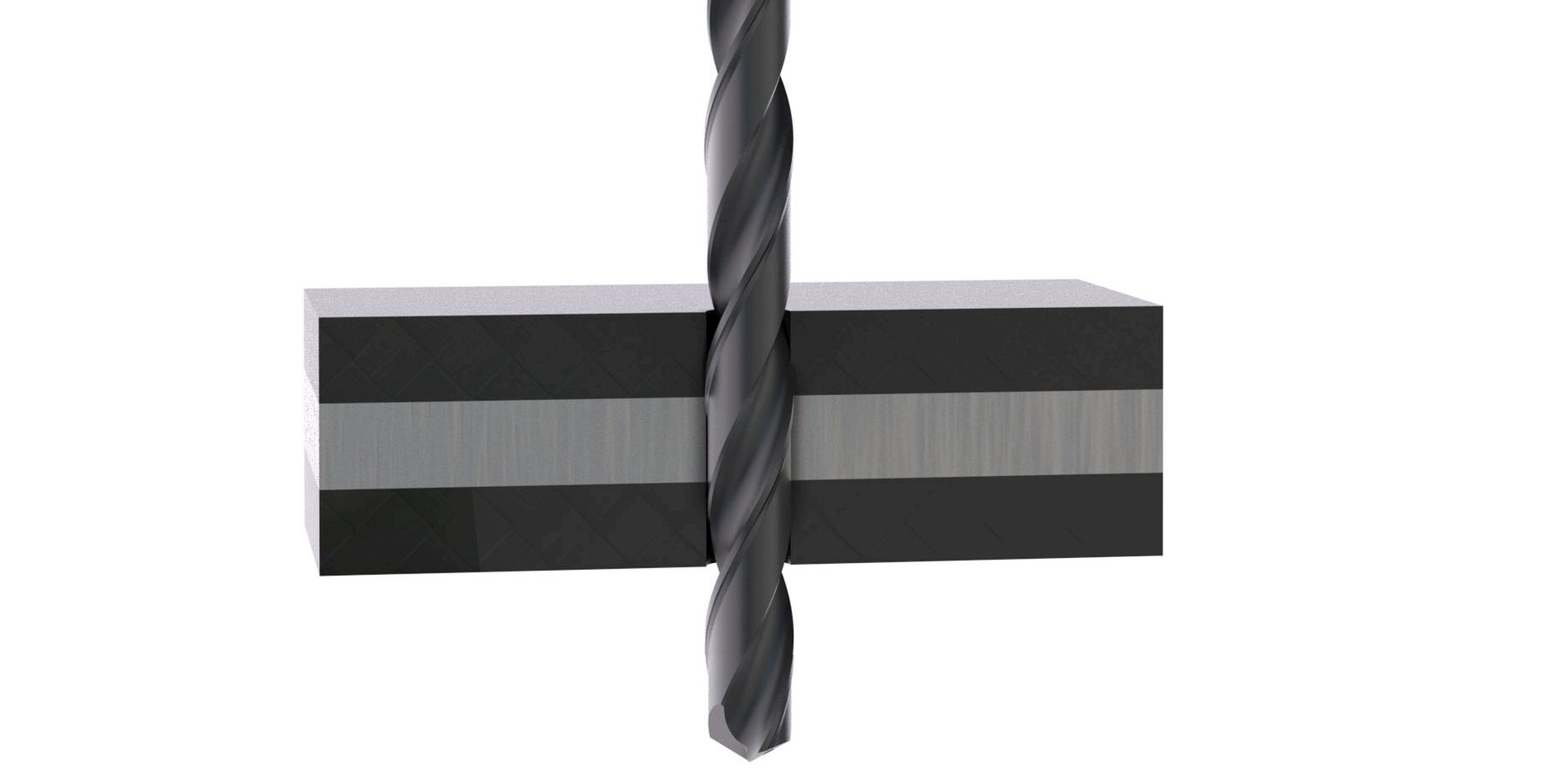
Belirli bir uygulama için en iyi takımı seçmek, çok çeşitli hususları içerir. Çok yönlü ve değişen uygulamalara ve üretim ihtiyaçlarına uyarlanabilir evrensel matkap geometrilerinin yanı sıra, doğru özelliklere, boyutlara, kaplamalara ve kesme özelliklerine sahip bir matkap seçmek performansınızı doğrudan etkileyecektir.
Delik başına en verimli maliyetle sürdürülebilir delme için, işiniz için doğru takımı bulmak üzere bir Seco uzmanıyla iletişime geçin veya Suggest'i deneyin.