Nástrojové geometrie jsou v obrábění rozhodující
To, z čeho jsou nástroje vyrobené je důležité, ale teprve jejich geometrie určují, čeho lze dosáhnout po stránce aplikační.
Výrobní provoz může mít všechny elementy potřebné k procesu obrábění – stroje vhodných možností, správné upínání nástrojů i obrobků, ... – ale pokud zvolí pro danou aplikaci špatnou geometrii nástroje, nemusí se optimální produkce dílců vůbec podařit. Geometrie nástrojů jsou zásadní, neboť přímo ovlivňují životnost, utváření třísky, stabilitu břitů i charakteristiky obrábění v zóně řezu, což se vše projeví v celkových nákladech na obrábění.
Volba obráběcích nástrojů je primárně založena na materiálu obrobku, jenž je třeba zpracovávat. Avšak vlastnosti obráběného materiálu a konstrukce nástroje musí být v souladu. Musí zde existovat propojení, a to je definováno řeznými parametry, tedy řeznou rychlostí, posuvem a hloubkou řezu. Řezná rychlost je spojnicí mezi materiálem obrobku a řezným materiálem, zatímco hloubky řezu a posuv představují vztah mezi geometrií nástroje a typem aplikace, a do určité míry i obráběným materiálem.
Geometrie nástroje je dána jeho konstrukcí a tvarem, přičemž zahrnuje několik důležitých faktorů.
Jedním ze základních je průběh linie ostří, jeho tvar a rozměry. Čím je ostří delší, tím lze dosáhnout větší hloubky řezu. Délky ostří jsou vyšší u hrubovacích geometrií a naopak kratší u dokončovacích. Dalším aspektem geometrie ostří jsou jeho vlastnosti na mikroskopické úrovni. Ostří mohou být přímá či zakřivená, umístěná v ose nebo skloněná a navíc „silná či tenká“.
Dalšími prvky geometrie jsou úhel čela, špička břitu, plocha hřbetu a přechodový tvar - fazetka (T). Čelní plocha je první ze dvou rovin, vymezených liniemi ostří daného břitu. Je to část nástroje, po níž sklouzává a odchází oddělená tříska, zatímco typ špičky břitu, poloha a nastavení jsou elementy, jež se bezprostředně vztahují k operaci oddělování materiálu – a to v oblasti obráběného povrchu. Plocha hřbetu je geometricky dána druhou rovinou, vymezenou liniemi ostří břitu. Plocha hřbetu slouží dvěma účelům: umožňuje průnik břitu nástroje do materiálu obrobku a poskytuje potřebnou stabilitu jeho ostří.
Mezi plochami čela a hřbetu definujeme přechodový tvar, tedy fazetku. Správná geometrie fazetky může být, zejména v případě nástrojů s PCBN či keramickými břity, rozdílem mezi úspěchem a selháním. Při použití břitových destiček z těchto materiálů v kombinaci s nevhodnou geometrií fazetky může dojít ke zničení nástroje během několika vteřin.
V průběhu samotného obrábění se navíc projevují tři další faktory související s geometrií nástroje. Jsou to jmenovitá, skutečná a efektivní geometrie.
Jmenovitou geometrií rozumíme sjednocenou čelní geometrii nástroje (s rovnou plochou) ve vztahu k poloze jeho ostří. Tato poloha může být negativní, neutrální nebo pozitivní.
- Pozitivní geometrie jsou doporučeny pro obráběné materiály s vyšší tažností a adhezivitou, tedy tendencí k nalepování, a také operace vyžadující nižší posuvy a hloubky řezu (tedy dokončování) za příznivých podmínek obrábění.
- Negativní geometrie jsou výhodné pro materiály s vyšší tvrdostí a abrazivitou, způsobujícími zvýšené síly a otěr, a dále operace s vyššími posuvy a hloubkami řezu (tedy hrubování) za nepříznivých podmínek.
- Neutrální geometrie se využívají v případech, kdy je třeba přesně přenést tvar ostří na obráběný povrch, tedy například při závitování, profilování, kopírování a dalších obdobných operacích.
Moderní obráběcí nástroje mají skutečnou řeznou geometrii, jenž je kombinací nerovné čelní plochy (geometrie utvařeče třísek), provedení ostří (úpravy ostří) a geometrie fazetky. Pokud však neznáme podmínky obrábění a řezné parametry ke konkrétnímu nástroji, nelze o skutečné geometrii nic říct, neboť se nejedná o daný fakt – záleží totiž na tom, jak je nástroj používán.
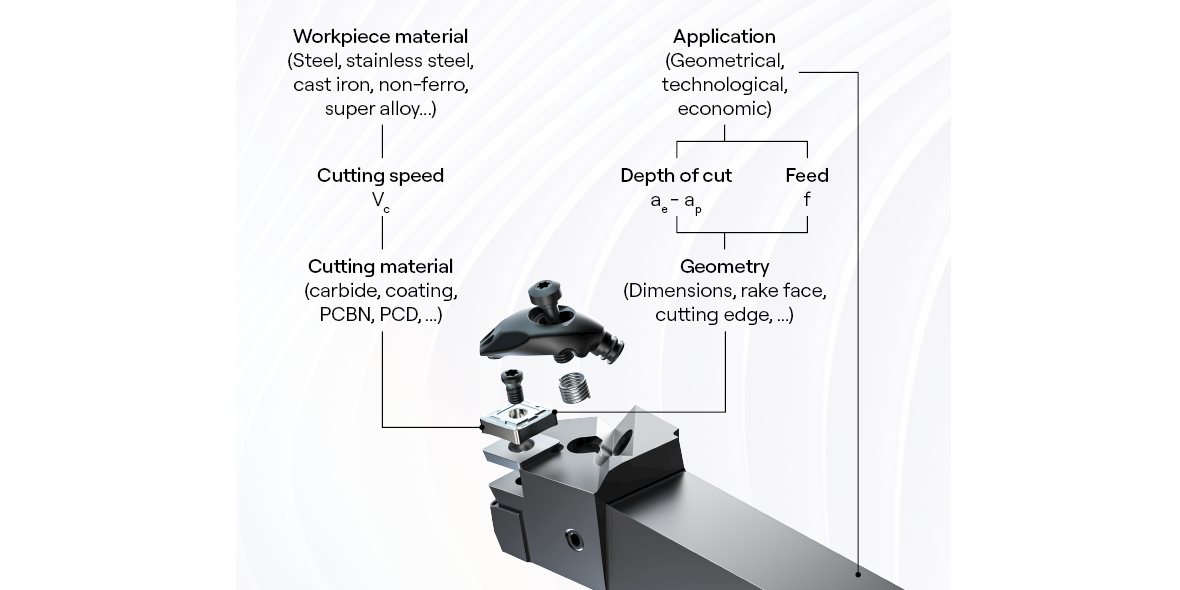
Efektivní geometrie obráběcího nástroje je geometrií „virtuální“, jenž určuje, jak bude břit nástroje fungovat v průběhu procesu obrábění. Toto chování je ovlivněno podmínkami obrábění – těžké obrábění, tvrdé obrábění, mikro obrábění atd. – a také aktuálními řeznými parametry v procesu.
Inline Content - Gridded Links
Tags: 'geometry_factor'
Max links: 1
Nástroj samotný – jeho materiál, konstrukce a tvar – a také poloha jeho ostří, to vše hraje roli v efektivním fungování nástroje. Ani dobrá nástrojová geometrie nepřinese kýžené výsledky, není-li využívána správně, a to samé lze říci správném využití nevhodné geometrie. Je-li geometrie špatná, trpí obráběcí operace již od samého počátku.
Jaký je rozdíl mezi teorií a praxí – geometrie je nahlížena podle toho, jak ostří vypadá, jak je velké, jaký má rádius, typ sražení atd. Co je však stejně, ne-li ještě důležitější, je otázka polohy ostří, tedy jeho aktuální i průběžné orientace vůči řeznému pohybu.
Poloha ostří nástroje plně souvisí s pevností a stabilitou. Pro zajištění správné polohy ostří je třeba znát materiál nástroje, komplexnost (jeden břit, dva břity) i jeho geometrii, neboť na těchto faktorech bude záviset i optimální poloha a upnutí celého nástroje.
Břit je spojen s tělesem nástroje a těleso dále se samotným obráběcím strojem. Všechna spojení musí být přesná, pevná a stabilní. I když má nástroj správnou geometrii a správné jsou i polohy jeho ostří vůči nástrojovému upínači, může přílišné házení upínače způsobit selhání celého procesu obrábění.
Každý prvek nástrojové geometrie slouží danému účelu, ať už se jedná o životnost, utváření třísky či stabilitu. Tyto prvky zahrnují i tvar a velikost břitové destičky; délku ostří; hlavní a vedlejší břit; polohu a geometrii špičky; linii ostří; polohu čelní a hřbetní plochy; úhel nastavení ostří, geometrii čela i mikrogeometrii ostří.
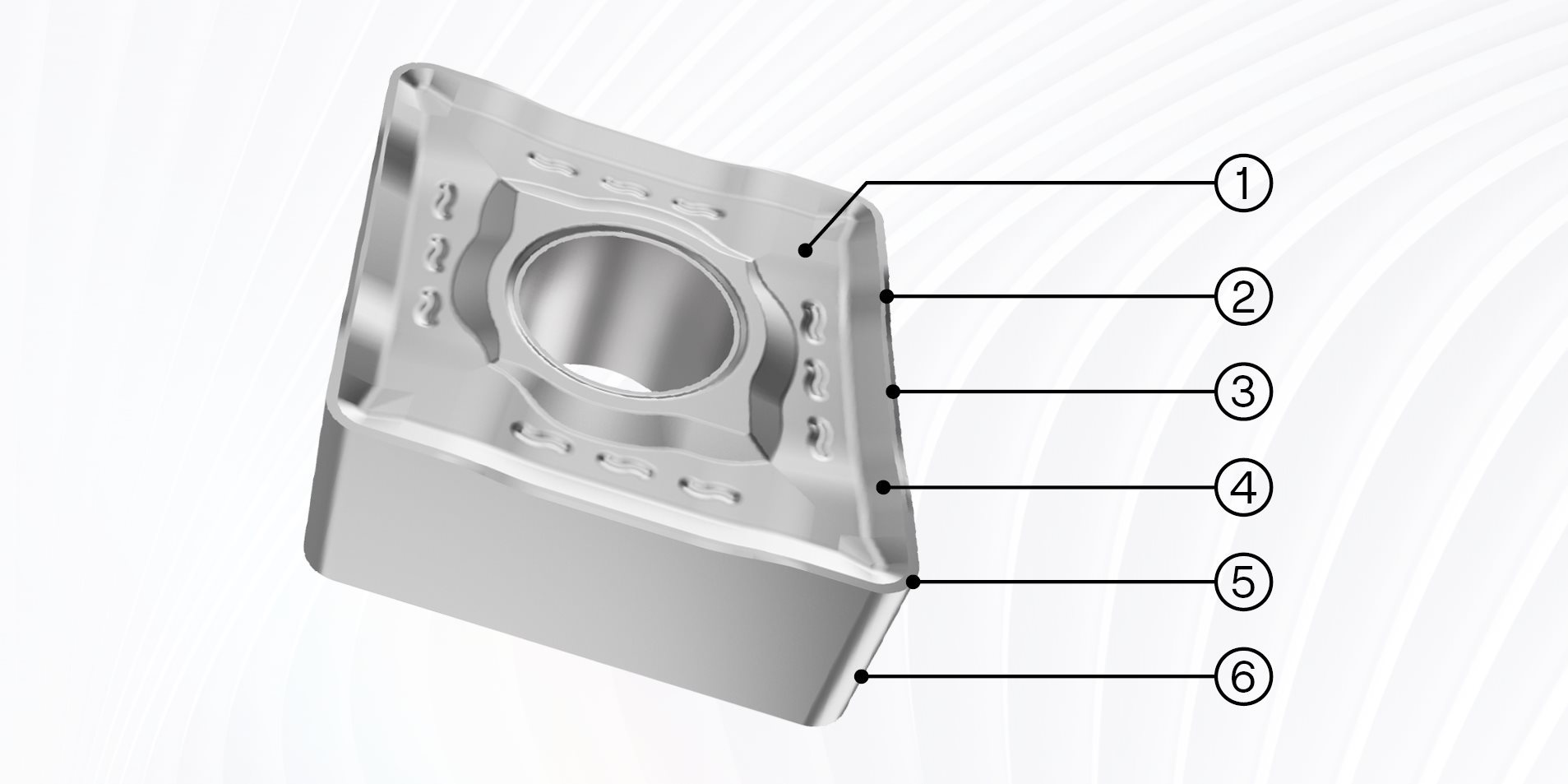
- Celkový tvar a rozměry nosiče břitu
- Typ a poloha linie ostří
- Geometrie řezné hrany
- Poloha plochy čela
- Typ a geometrie špičky břitu
- Geometrie polohy hřbetní plochy
- Celkový tvar destičky je určen plochou čela, plochou hřbetu a špičkou břitu a má velký vliv na pevnost nástroje. Čím větší je vrcholový úhel břitu, tím větší je i celková odolnost nástroje vůči odlomení.
- Délka ostří určuje maximální hloubku řezu, kterou může nástroj zvládnout.
- Hlavní ostří nástroje provádí samotné odebírání materiálu. Toto ostří končí u špičky a jeho pokračování za špičkou se nazývá vedlejší ostří – zvané též hladicí ploška nebo wiper. Vedlejší ostří je společně s geometrií špičky a hodnotami posuvu odpovědné za kvalitu obrobení povrchu součásti.
- Pevnost špičky břitu umožňuje využívat vyšší řezné parametry. Pevnější špičky znamenají i vyšší hloubky řezu a posuvy.
- Linie ostří a poloha čelní i hřbetní plochy určují vlastní polohu ostří nástroje. Zde hovoříme o úhlu sklonu ostří (nebo úhlu šroubovice) a popisujeme tím, jak je úhel nastavení ostří orientován vůči směru pohybu nástroje. Tento prvek geometrie se využívá k ovlivnění utváření třísky – pro spolehlivost procesu – a řezných sil – pro životnost nástroje.
- Úhel nastavení ostří také definuje, v jaké poloze se břit nástroje nachází. Úhel nastavení ostří symbolizuje polohu ostří ve vztahu ke směru posuvu daného nástroje.
- Geometrie čelní plochy ovlivňuje, jak jsou třísky utvářeny a odváděny. Z tohoto pohledu rozlišujeme ostré, střední a pevné geometrie, které pak určují jejich aplikace. Jemná či ostrá geometrie je určena pro dokončování, střední geometrie pro běžné operace a pevná geometrie zase pro operace hrubování.
- Mikrogeometrie ostří je rozsahem velmi malá a v průběhu obrábění se v důsledku opotřebovávání břitů nástroje mění.
Chování řezné geometrie závisí na řezných podmínkách, za nichž je nástroj nasazen. Od jednoho souboru podmínek ke druhému se může chování i výkonnost nástroje měnit, i když geometrie samotná zůstává stálá. V rámci těchto řezných podmínek užíváme řezné geometrie neutrální, řezné geometrie pozitivní a řezné geometrie negativní.
Neutrální řezná geometrie znamená, že efektivní úhel čela je nulový a úhel mezi směrem řezu a čelem břitu je 90 stupňů. Mezi tím, jakou pevnost má daný nástroj a skutečností, jaké namáhání vzniká v průběhu samotného řezného procesu musí být rovnováha.
Pozitivní řeznou geometrií rozumíme stav, kdy je úhel mezi směrem pohybu a čelem nástroje větší než 90 stupňů, a úhel čela je tedy pozitivní. V důsledku je namáhání působící na břit nástroje nižší, ale právě tak se snižuje i schopnost nástroje toto namáhání snášet. Pozitivní řez je výhodný pro snazší obráběcí operace nebo v situacích, kdy je namáhání v průběhu operace nižší, třeba v důsledku malých hloubek řezu a nižších posuvů.
Negativní řezný proces nastává za situace, kdy je úhel mezi směrem řezu a čelem nástroje menší než 90 stupňů. Tento přístup se aplikuje v případech, kdy se očekává vyšší úroveň namáhání břitů nástroje.
I když je to, z čeho jsou nástroje vyrobené důležité, teprve jejich geometrie určují, čeho s nimi lze dosáhnout po stránce aplikační. Pro určení dobře fungujícího obráběcího nástroje jsou důležité dvě věci: jednak aby byly v rovnováze materiál nástroje a obrobku, přičemž vyrovnávacím faktorem je řezná rychlost.
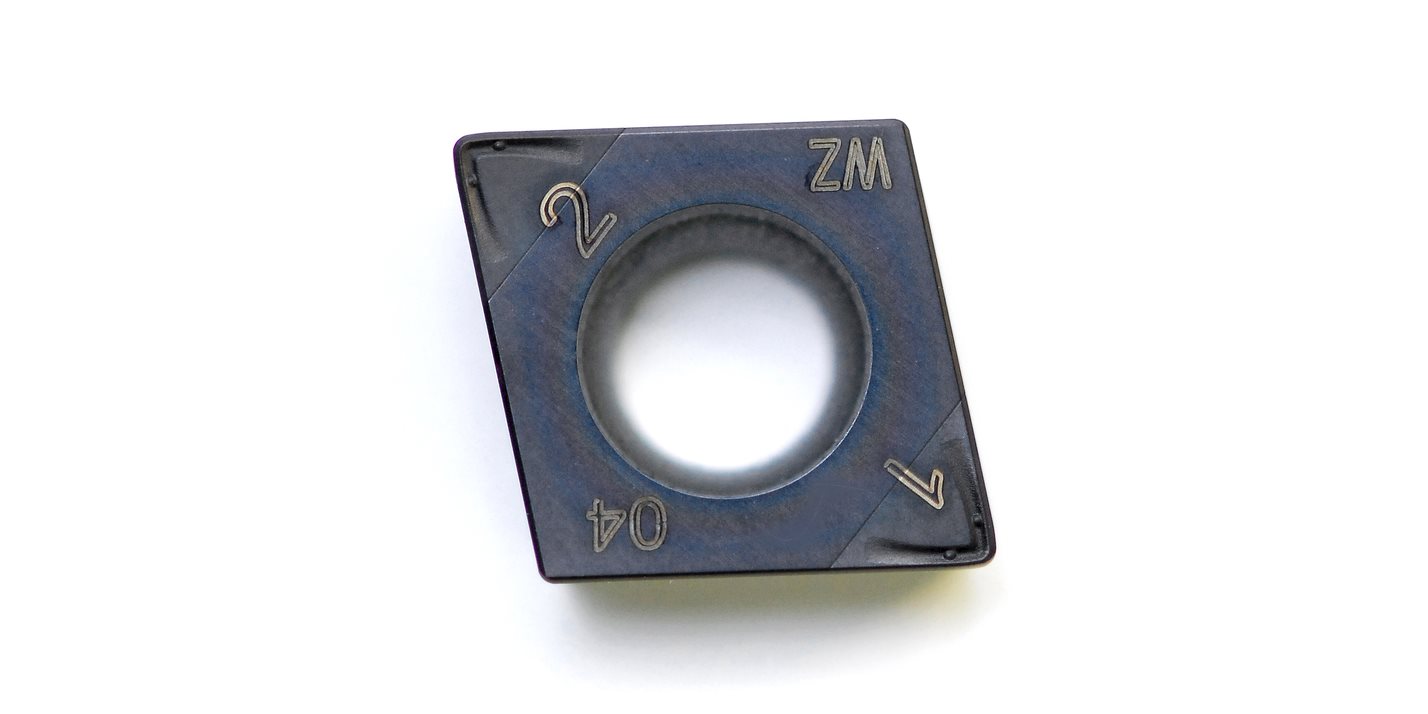
Druhou záležitostí jsou typ aplikace a řezná geometrie, jež musí být v rovnováze také. Právě kvůli posledně zmíněné skutečnosti je nezbytné mít správné znalosti o řezných geometriích i o tom, jakým způsobem je využít při optimalizaci procesů obrábění.
Inline Content - Survey
Current code - 5fce8e61489f3034e74adc64