„Már nem csak egy divatszó": Hogyan nyomja rá bélyegét a 3D nyomtatás az orvostudományra
Az additív gyártás már nem divatos szó: ez már bevett gyakorlat. Fedezze fel a 3D nyomtatás mozgatórugóit az orvosi szegmensben.Kevesebb mint egy évtized alatt az additív gyártás (AGy) az orvosi ipari konferenciák forró témájából a gyártósorra került A vezető ortopédiai gyártók ma már évente több százezer csípőprotézis előállításához használják a 3D-s fémnyomtatást, amely lehetővé teszi a korábban lehetetlen bonyolult formák létrehozását.
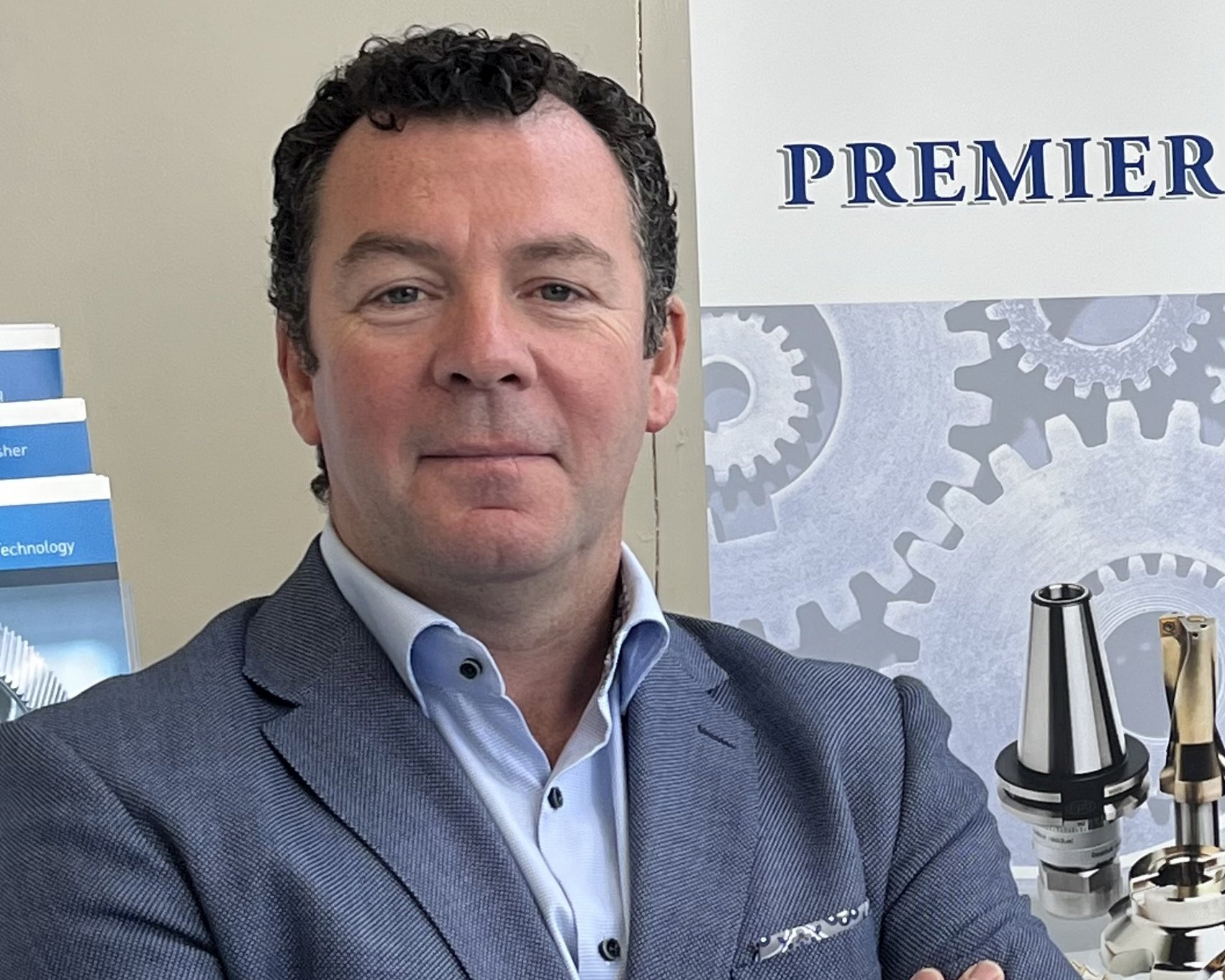
Mások személyre szabott csontpótlást állítanak elő súlyos balesetek vagy csontrák áldozatai számára. Még azok a gyártók is, akik hagyományos technikákat alkalmaznak a tényleges gyártáshoz, az AM-et használják a termékfejlesztés felgyorsítására.
„Tíz évvel ezelőtt beszéltünk erről, öt évvel ezelőtt játszottunk vele, de most már tömeggyártásra használjuk” - mondta Ciaran Dillane, a Premier Machine Tools ügyvezető igazgatója, a Seco leányvállalata, amely az ír orvosi ipar egyik fő beszállítója.
„Nem hiszem, hogy ez már csak egy divatos szó: ez a szokásos gyakorlat.”
Az orvostechnikai iparban a 3D fémnyomtatáshoz használt fő technika a lézerporágy-olvasztás (Laser Powder Bed Fusion, LPBF), ahol a fémpor mindössze mikron vastagságú rétegeit egy ágyon a növekvő alkatrészre ecsetelik, majd lézerrel összeolvasztják.
A 3D-s fémnyomtatás az ortopédiai ipar standard módszerévé válik az olyan ízületi pótalkatrészek, mint a csípő, a térd és a váll, vagy a koponyasérülések helyreállítására szolgáló hálók gyártására, mivel lehetővé teszi a hagyományos kovácsolással vagy marással lehetetlen összetett szivacs- vagy rácsszerkezetek előállítását.
A rácsot ott helyezik el, ahol a titán találkozik a csonttal, amely aztán utat talál magának a rácson keresztül, és megáll a növekedésben, amikor kemény felülethez ér. Ez a „becsontosodási” technika jobb kötést hoz létre a csont és az alkatrész között, mint a korábbi „csontbecsontosodási” technika, és megszünteti a csontcement szükségességét, csökkentve a fertőzés kockázatát.
„Minden ortopédiai gyártónak megvan ennek a technológiának a saját változata, és ez az elmúlt öt évben hatalmas méreteket öltött” - mondta Dillane.
A legtöbb esetben titánport használnak, amely a csonthoz hasonló rugalmassággal rendelkezik, és a krómtól vagy a vasat is tartalmazó ötvözetektől eltérően teljesen biokompatibilis. A Seco tulajdonosa, a Sandvik több mint 2000 fémport kínál, amelyek közül egyre több - jelenleg közel 50 - az additív gyártáshoz tartozik.
Az additív gyártást a gerincimplantátumok esetében is kezdik alkalmazni, ahol a 3D-s fémnyomtatással előállított titán helyettesíti a polimert a gerinccsigolyák esetében. Speciális sebészeti műszerek készítésére használják, amelyeket egy adott betegre vagy műtétre szabnak.
„Úgy gondolom, hogy a fogászat sokkal gyorsabban változik: kisebb alkatrészekből áll, amelyek tűréshatárai nem olyan kritikusak” - magyarázta Andrew Fielding, a Seco globális üzletfejlesztési menedzsere (Medical). „A piac 50-60 százalékát fogja elérni a következő néhány évben.”
Ingemar Bite, a Seco Additive Manufacturing részlegének K+F menedzsere szerint ezekben az esetekben az alkatrészeket a nyomtatás után kell megmunkálni, mind a pontos végső formájuk elérése, mind a megfelelő felületi minőség elérése érdekében.
"Közvetlenül a folyamat után van egy természetes porozitással teli felületünk, ezért minden olyan felületet meg kell munkálni, amely vagy nagy húzófeszültségnek van kitéve, vagy geometriai tűrésekkel vagy felületi minőséggel rendelkezik" - magyarázta.
Ez azt jelenti, hogy az alkatrész alakját már a számítógépes tervezési szakaszban is a megmunkálást szem előtt tartva kell megtervezni, amihez a gyártók igénybe vehetik a Seco szakértői segítségét.
A svédországi Stockholmtól 175 km-re északnyugatra, Fagerstában található Seco létesítményében, Bite csapata azóta kutatja az additív technológiát, hogy a Seco 2018-ban megvásárolta első LPBF-gépét.
„Eddig fejlesztés alatt állt, értékeléssel és helyszíni tesztekkel, mind az ügyfeleinknél, mind a vállalaton belül. Most úgy érezzük, hogy a folyamat annyira stabil, és elég tudásunk van ahhoz, hogy ezzel a technológiával elinduljunk az ügyfelek felé” - mondta Bite.
A vállalat korábban már dolgozott az AGy-sal, de a Sandvikenben lévő Additive Manufacturing Centerrel együttműködve elkészítette első AGy termékét, a hűtőrögzítőt.
Ez a rögzítő, amely 2017 óta áll az ügyfelek rendelkezésére, egy íves csatornán keresztül képes a hűtőfolyadékot a vágóél egy adott részéhez irányítani, ami a hagyományos megmunkálású szerszámoknál lehetetlen.
Az év elején a Seco mind az AGy végzését, mind a K+F-et áthelyezte az év elején az igényeinek megfelelően újjáépített létesítménybe.
„Ez nagy előny számunkra, ahogy én látom: még mindig sokat kell tanulnunk és értékelnünk az AGy terén, és az, hogy a K+F és a gyártás közel dolgozik egymáshoz egy fedél alatt, sok előnnyel jár.” Bite azt mondta. "Ez nagyobb rugalmasságot biztosít a berendezésekkel és jobb ellenőrzést biztosít a folyamat felett."
A Seco célja, hogy a hagyományos megmunkáláshoz egyedi szerszámokat állítson elő az AGy segítségével, különösen ott, ahol az ügyfélnek olyan jobb megoldásra van szüksége, amely csak ezzel a módszerrel érhető el.
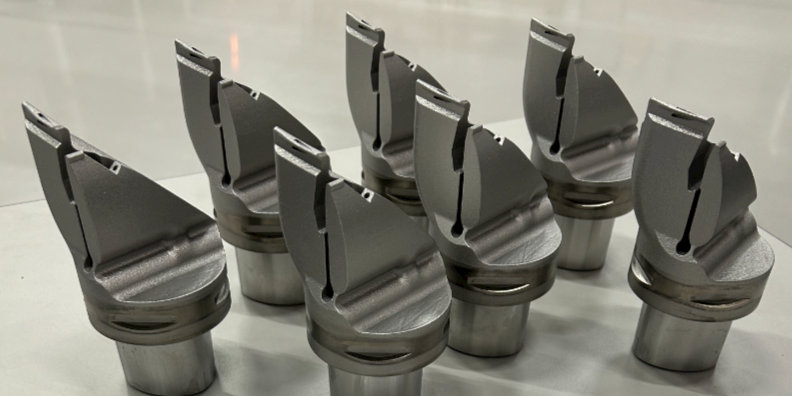
A vállalat olyan hibrid szerszámokat is fejleszt, amelyeknél a szerszám elülső részét, amely egyedi zsebet, funkciót vagy hűtőfolyadék-kivezetést tartalmaz, 3D-nyomtatással közvetlenül egy hagyományos megmunkálású hátsó részre nyomtatják.
Ez lehetővé teszi a Seco számára, hogy lapkákat és/vagy más szerszámokat használjon igen nagy kihívást jelentő alkalmazásokban, hozzáférést biztosítva egy funkcióhoz vagy lehetővé téve olyan anyagok megmunkálását, amelyek egyébként nagyon nehezen lennének megmunkálhatók.
Az AGy szerszámoknak más előnyei is vannak. Az esetek többségében a teljes tömeg akár 20 százaléka is eltávolítható anélkül, hogy ez befolyásolná a szerszám teljesítményét. A 3D-nyomtatás egy hagyományos módon megmunkált hátsó résznek csökkentheti a gyártási idejét.
A kisebb súly szintén javíthatja a szerszám teljesítményét, különösen olyan esetekben, amikor a szerszám hosszú túlnyúlásokkal rendelkezik, ahol a kisebb súlyú szerszám növelheti a rúd passzív dinamikus csillapításának hatását.
Míg egyes gyártók sorozatgyártásra használják a technikát, az akkor válik igazán hasznossá, amikor testreszabásra van szükség, amikor az implantátumokat, protéziseket és műtéti segédeszközöket páciensspecifikus anatómiai adatok alapján tervezik.
Dillane arra számít, hogy ez lesz az általános gyakorlat a súlyos balesetek vagy csontrák áldozatainak szánt alkatrészek gyártásánál. „A kórházban csinálnak egy CT-vizsgálatot rólad, megértik, hogy milyen állapotban van a csontod, majd ezt elküldik az egyik ortopédiai gyártónak egy felvétel formájában. Egy éjszaka alatt visszafejtik, majd 3D nyomtatóra teszik, és 24 órán belül kinyomtatják. És valószínűleg 36-48 óra múlva már ki is sétálhat a kórházból.” Ez a gyors átfutási idő, amelyhez a betegek a fogászati implantátumok beültetésekor hozzászoktak, csökkenti azt az időt, amelyet a betegeknek a kórházban kell várniuk a protézisekre.
Más iparágakbana rövid átfutási idő felgyorsíthatja a termékfejlesztést. A Seco nemrégiben segített egy globális ortopédiai gyártónak, hogy az első tervektől mindössze hat hét alatt eljusson egy teljesen megmunkált combcsont komponensig. Bár a végleges alkatrészt hagyományos módon kovácsolják és marják, a prototípusok elkészítéséhez használt additív gyártás több mint felére csökkentette a fejlesztési időt.
Az elkövetkező évtizedben az additív gyártás minden bizonnyal megelőzi a hagyományos technikákat az ortopédiai és a fogászati szegmensben, mivel egyre gyakoribbá válnak az egyedi páciensekre szabott, testre szabott alkatrészek, és egyre rövidebbé válnak az átfutási idők. A technika valószínűleg új, összetettebb mechanikai alkatrészeket is lehetővé tesz, például gerincketreceket és mesterséges térdeket a gyermekek számára, amelyek növekedni tudnak, és a chipek beágyazása is könnyebbé válik. Végül pedig olyan új gépek jelennek meg, amelyek képesek váltakozni az additív gyártás és a hagyományos marási technikák között.
„Már nem beszélünk a megmunkálásról. Az alkatrészek kialakításáról beszélünk” – magyarázta Dillane. „Mert számunkra az additív gyártás és a szubtraktív gyártás a csípőnél fogva kapcsolódik össze.”
Szeretne többet megtudni az additív gyártás előnyeiről és kihívásairól az orvosi szegmensben?
További válaszokat a legújabb e-könyvünkben talál!
Inline Content - Survey
Current code - 5fce8e61489f3034e74adc64