L'essor des MMC : Avantages, défis et solutions dans l'utilisation des composites à matrice métallique
Dotés d’une exceptionnelle légèreté, les composites à matrice métallique se distinguent néanmoins par une robustesse remarquable. Ils commencent à révolutionner l’industrie, notamment dans les applications aéronautiques et automobiles. Voici quelques avantages et inconvénients de leur utilisation, ainsi que la meilleure façon de les usiner.Dotés d’une exceptionnelle légèreté, les composites à matrice métallique se distinguent néanmoins par une robustesse remarquable. Ils commencent à révolutionner l’industrie, notamment dans les applications aéronautiques et automobiles Voici quelques avantages et inconvénients de leur utilisation, ainsi que la meilleure façon de les usiner.
S'il existe aujourd'hui un graal pour les fabricants de solutions d'ingénierie dans les secteurs de l'aéronautique et de l'automobile, c'est bien la création de produits à la fois légers et durables.
Il s'agit d'une préoccupation majeure pour ces deux secteurs, car ils sont confrontés à la double pression de la durabilité (par le biais de la réglementation et des exigences croissantes des clients) et de la rentabilité.
« Vous devez concevoir un matériau et un composant qui ne soient pas trop lourds, afin de réduire la consommation globale de carburant d'un avion ou d'une voiture, tout en conservant une grande solidité, une bonne résistance à l'usure et une grande durabilité », explique M. Rachid M'Saoubi, expert principal en recherche sur l'usinage chez Seco Tools.
Les MMC sont une classe de matériaux qui permettent d'atteindre l'équilibre difficile entre la réduction du poids et la résilience mécanique. Il s'agit essentiellement d'un amalgame de matériaux plus souples et d'éléments plus durs et renforcés. Parmi les exemples les plus courants, on trouve les alliages d'aluminium plus souples renforcés par des particules de carbure de silicium ou de carbure de silicium titane, qui augmentent leur robustesse.
À l'instar d'un chef cuisinier travaillant sur une recette, les fabricants cherchent à obtenir un mélange délicat qui permette d'améliorer la résistance à l'usure, mécanique et thermique, tout en minimisant le poids, un facteur crucial dans la conception des pièces automobiles et aéronautiques modernes.
Dans l'industrie aéronautique, l'augmentation des températures de fonctionnement et de l'efficacité des moteurs d'avion signifie que les matériaux utilisés doivent résister à des contraintes encore plus fortes », explique Rachid M'Saoubi.
Les composites à matrice métallique d'aluminium tels que le carbure de silicium-aluminium et l'Al-Al2O3 sont utilisés dans l'industrie automobile, où leur excellente résistance à l'usure et leur stabilité thermique les rendent adaptés aux moteurs, aux systèmes de freinage et aux systèmes de suspension.
Le carbure de titane et de silicium est utilisé dans les applications à haute température dans les moteurs. Ces composites à matrice de titane sont renforcés par des particules ou des fibres céramiques. Ils offrent un excellent rapport résistance/poids, ainsi qu'une résistance élevée aux températures extrêmes et à la corrosion, ce qui les rend adaptés à des pièces telles que les aubes de turbine, les revêtements de chambre de combustion et les conduits d'échappement.
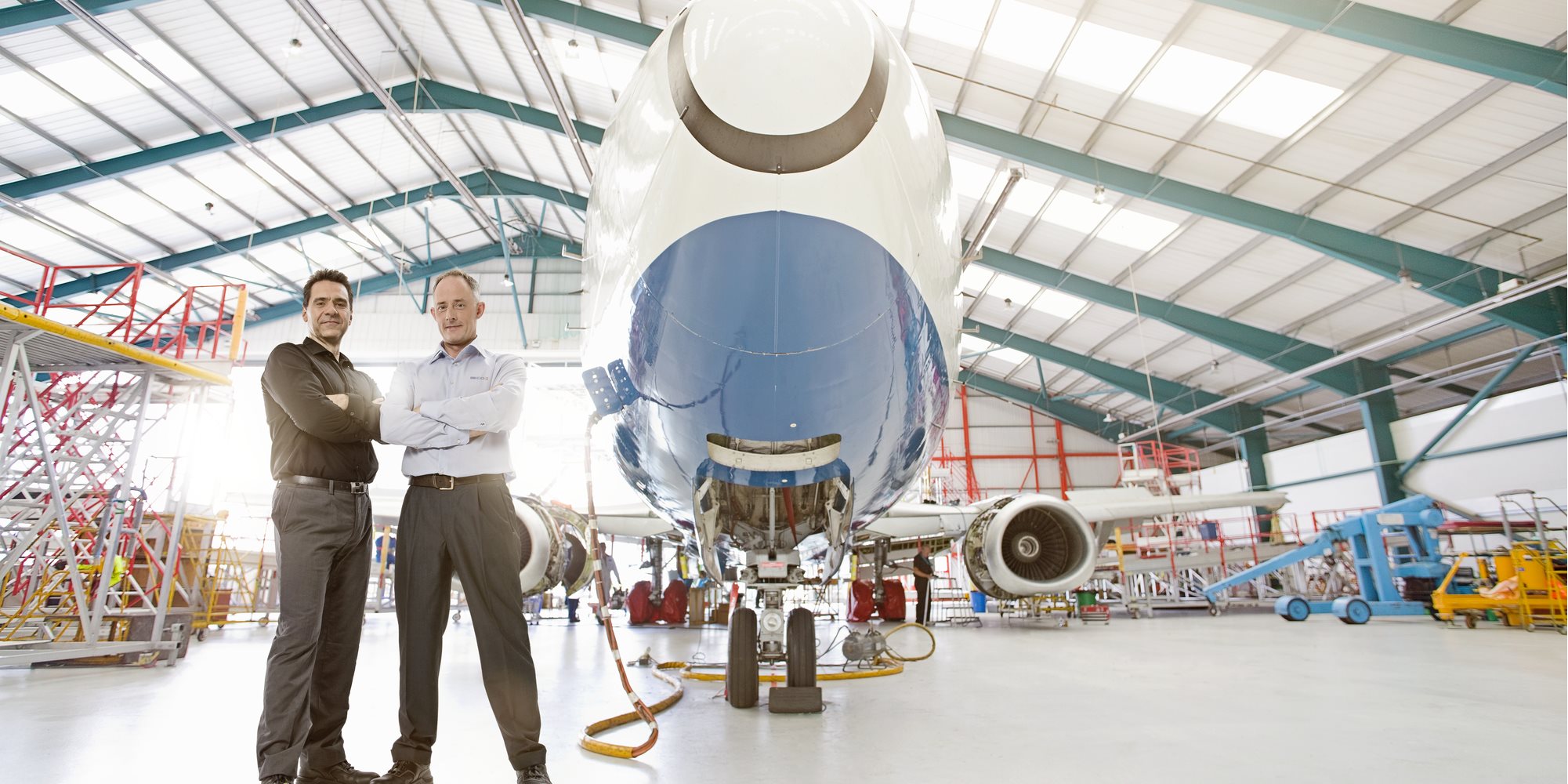
Parmi les autres MMC figurent les composites à base de magnésium, dont la rigidité, la résistance à la corrosion et la solidité conviennent aux panneaux structurels, aux composants de châssis et aux boîtiers de transmission, ainsi que les MMC hybrides et avancés utilisés dans des éléments de carrosserie, les moyeux de roue et les composants du groupe motopropulseur.
Si les MMC promettent une nouvelle ère d'excellence dans le domaine des matériaux, leur usinage pose des problèmes spécifiques. D'une certaine manière, leurs forces renferment aussi leurs faiblesses.
Parce qu'ils sont légers par nature, ils ont tendance à se déformer pendant l'usinage », explique Monsieur M'Saoubi.
Les problèmes de distorsion, particulièrement fréquents dans les structures à parois minces, exigent une attention toute particulière lors des phases d'usinage et de traitement thermique.
« Il est indispensable de disposer d'un système de fixation précis et d'un outillage spécifique pour pouvoir les usiner avec succès sans qu'ils ne se déforment ou ne se courbent », ajoute-t-il.
En outre, la forme proche des cotes finales de la plupart des MMC exige à l'opérateur d'être très précis. Moins il y a de matière, et plus la marge d'erreur lors de la mise en forme est réduite par rapport au bloc de matière première. « En règle générale, un matériau proche de sa forme finale est léger, ce qui lui confère une faible élasticité et le rend particulièrement sujet à la déformation », explique Rachid M'Saoubi.
« Moins il y a de matière à retirer, plus il est crucial de prêter attention à la géométrie de l'outil, en particulier à sa micro-géométrie, qui joue un rôle déterminant. »
Le choix des plaquettes appropriées est particulièrement crucial lors de l'usinage des MMC. La préférence va généralement aux matériaux qui présentent une résistance élevée à l'usure abrasive, tels que le carbure cémenté à grain fin ou les outils en diamant polycristallin, car ils maintiennent une arête vive afin de réduire le phénomène d'arête rapportée.
Cependant, l'émergence de composites à matrice métallique (MMC) de compositions inédites, comme les alliages de titane renforcés par des fibres longues, impose au technicien d'adopter une approche plus nuancée.
« Les matériaux à fibres longues peuvent présenter des propriétés spécifiques selon l’orientation, comme l'anisotropie, où les comportements varient en fonction de la direction, les fibres ne s'alignant que dans certaines orientations », explique Rachid M’Saoubi.
« Dans les matériaux composites, c’est assez souvent le cas. Par exemple, le polymère renforcé de fibres de carbone contient des fibres disposées selon des orientations spécifiques. Cela signifie qu'il faut modifier l'orientation afin d'obtenir de bonnes propriétés mécaniques dans plusieurs directions. »
Selon Monsieur M'Saoubi, les particules fines posent moins de problèmes dans les MMC (avec une fraction volumique allant de 5 à 40 %). Mais comprendre leur taille et leur répartition dans le matériau devient essentiel pour obtenir les meilleurs résultats en usinage.
En tant que pionnier de la technologie des outils coupants, Seco Tools innove continuellement en matière de stratégies de coupe et adopte des approches d'usinage flexibles, tout en collaborant avec des partenaires de l'industrie et du monde universitaire qui s'intéressent de près à des enjeux tels que les MMC.
Découvrez l'innovation du projet Thermac : L'usinage laser pour matériaux composites
Nous devons nous pencher non seulement sur les défis posés par ces matériaux nouveaux et émergents, mais aussi sur les possibilités offertes par le développement des machines-outils », déclare Rachid M'Saoubi.
« Les machines-outils sont conçues pour optimiser l'utilisation des solutions d'outillage, et dans ce contexte, les stratégies de coupe sont cruciales lors de l'usinage de ces matériaux, en raison des défis liés à leur légèreté et à leur forme proche de la cote finale.
C'est un domaine qui évolue constamment, avec de nouveaux défis d'usinage, mais M. Rachid M'Saoubi estime que ces MMC plus légers et plus résistants ont un grand potentiel.
« Ils offrent des performances, une efficacité et une durabilité accrues », explique-t-il.
Inline Content - Survey
Current code - 5fce8e61489f3034e74adc64