レーザーアシスト熱加工:MMC (Metal Matrix Composites) を使用した製造プロセス?
レーザーアシスト熱加工は、金属マトリックス複合材 (MMC) の製品を製造する際の困難な加工課題に対する解決策となるでしょうか?Seco が関与する英国を拠点とするエキサイティングなプロジェクトが、その回答を見つけ出しています。
現在、チタンやアルミニウムシリコンカーバイドなどの金属マトリックス複合材(MMC)は、従来の金属に欠けていた軽さと強度の理想的な特性の組み合わせを可能にする材料として開発されました。航空機産業と自動車産業は、燃料消費量を削減し、環境維持の持続可能性を高め、コスト制御を管理する製品の製造にこれらの複合材料を検討し始めています。
しかし、金属マトリックス複合材 (MMC) の機械加工は非常に困難です。セラミック粒子や繊維成分などの硬質強化材が含まれていることが多いため、材料が研磨性を有しています。これらには、柔らかいマトリックスに囲まれた硬質材料が含まれているため、均一に機械加工することが難しく、加工面品質が低下します。これほどの価値があるのですが、高性能な素材には向いていません。また、局所的に高熱が発生しやすく、熱による加工歪みや工具劣化に影響を及ぼします。
工具の摩耗率が高く、加工結果も悪いため、従来の工具での製造プロセスでは対応できません。多結晶ダイヤモンド切削インサートは 金属マトリックス複合材 (MMC) に対応できますが、数回の加工パスで摩耗してしまいます。それは高価で良い方法ではありません。
その回答はレーザーアシスト熱加工にあるかもしれません。これは、欧州の THERMACH (熱加工) プロジェクトの支援の下で、Seco、ノッティンガム大学、先端材料企業 TISICS、レーザー開発企業 Optek、Attenborough Medical などが参加する英国を拠点とするエキサイティングな研究プログラムです。
THERMACH は、英国、スウェーデン、オーストリア、カナダが参加する研究共同事業組織で、過去 4 年間にわたり、レーザーおよび誘導支援加工技術のさまざまな側面を研究してきました。しかし、特に有望なのはレーザーの研究分野です。
「サーマルマシニングプロセスでは、レーザーが切削工具の前の材料を加熱し、材料を可塑化または溶融させて、切削工具が通過しやすくなります」と、工具と加工プロセスに関する専門知識をプロジェクトに提供してきた Seco の R&D テクニカルリーダーの Mark Walsh は説明します。
Nottingham 大学はこのプロジェクトの研究拠点であり、英国政府の投資機関である INNOVATE UK が資金を拠出しています。准教授の Zhirong Liao 博士と Omkar Mypati は大学チームの主要メンバーです。Nottingham 大学は、航空機産業の大手企業を代表して 10 年以上にわたって金属マトリックス複合材 (MMC) の研究を行っており、Seco とは長年にわたる協力関係を築いています。
「Seco は以前に、ニッケル合金にレーザーアシスト熱加工を採用しており、航空機産業のカスタマーに対しては好結果を収めました」と Zhirong Liao は言います。
「私たちはレーザービームを制御し、同じ温度と分布で焦点を合わせるプロセスを開発しました。これは非常に良好な結果であり、機械加工がより非常に困難な材料にも適用することにしました。」
この研究のきっかけとなったのは、金属複合材を専門とする英国企業 TISICS でした。THERMACH (熱加工) プロジェクトの英国研究部門のプロジェクトマネージャーも務めるマネージングディレクターの Stephen Kyle-Henney がこれに関して語る:
「私たちは、航空機着陸装置など、航空機産業のさまざまな高性能用途向けにチタン複合材を開発してきました。」と彼は言います。
「チタンに繊維シリコンカーバイド強化材を使用することで、鋼鉄と同等の硬さでありながらチタンよりもはるかに強靭なチタンを製造することができます。そして、航空機着陸装置の用途では、セラミック繊維の圧縮特性により、鋼材よりも軽量で強度特性もはるかに優れています。
「非常に強くて硬いので素晴らしいのですが、それを最終的な製品の形状するのはとても困難です。繊維が硬すぎて動かすと折れてしまうため、一度製造したものを鍛造などで曲げることはできません。」
Kyle-Henney は、シリコンカーバイドの硬度により、Seco の硬質切削インサートを使用したとしても、材料が切削されているにもかかわらずカッタの先端も切削されるため摩耗率が非常に高くなり、経済的効率性が確保できないと付け加えています。この課題に対する TISICS の最初の対応策は、機械加工が不要になるように繊維を素材に埋め込むことでしたが、それによって製造と修理の柔軟適用性が低下しました。
「Nottingham 大学は、航空機製造企業と協力して機械加工技術に取り組んだり、Secoと協力して機械加工技術に合ったツール技術を開発し、切削速度、加工効率、加工品質を最適化するなど、高度な機械加工技術の素晴らしい歴史と実績を持っています。」と彼は言います。
「私たちからの要求は予想外だったかもしれませんが、開発チームは真摯に応えてくれました。歴史的に、私たちがそれを機械化しようとしたとき、それはあなたが設計された表面ではなく、庭の熊手で機械化しようとしたもののように見える! 現状では実際に機械加工されているように見えます。」
このプロジェクトはまもなく最終段階に達しますが、今後の数年間で加工プロセスが有効可能になるまでにはまだいくつかの対策が必要です。現在、Attenborough Medical の Jensen Aw が注目している研究分野の 1 つは、熱プロファイルのマッピングです。Jensen Aw は、レーザーが材料を加熱する方法と、セラミックファイバーが金属とどのように異なった加熱がされるかを分析しています。セラミックシリコンカーバイド繊維の融点は 3,000 ℃ ですが、チタンは 1,600 ℃ で溶解します。
「均一に加熱したくないものを均一に加熱しようとしているのです」と Kyle-Henney は言う。「それを可能にするモデリングマッピングは非常にエキサイティングな挑戦です。これは素晴らしい仕事です」
レーザーを固定位置ではなくロボットで動かすことも可能で、これによって複雑な形状の加工が可能になります。ここでは、Optek のレーザー技術とロボット工学に関する専門知識が重要な役割を果たしています。
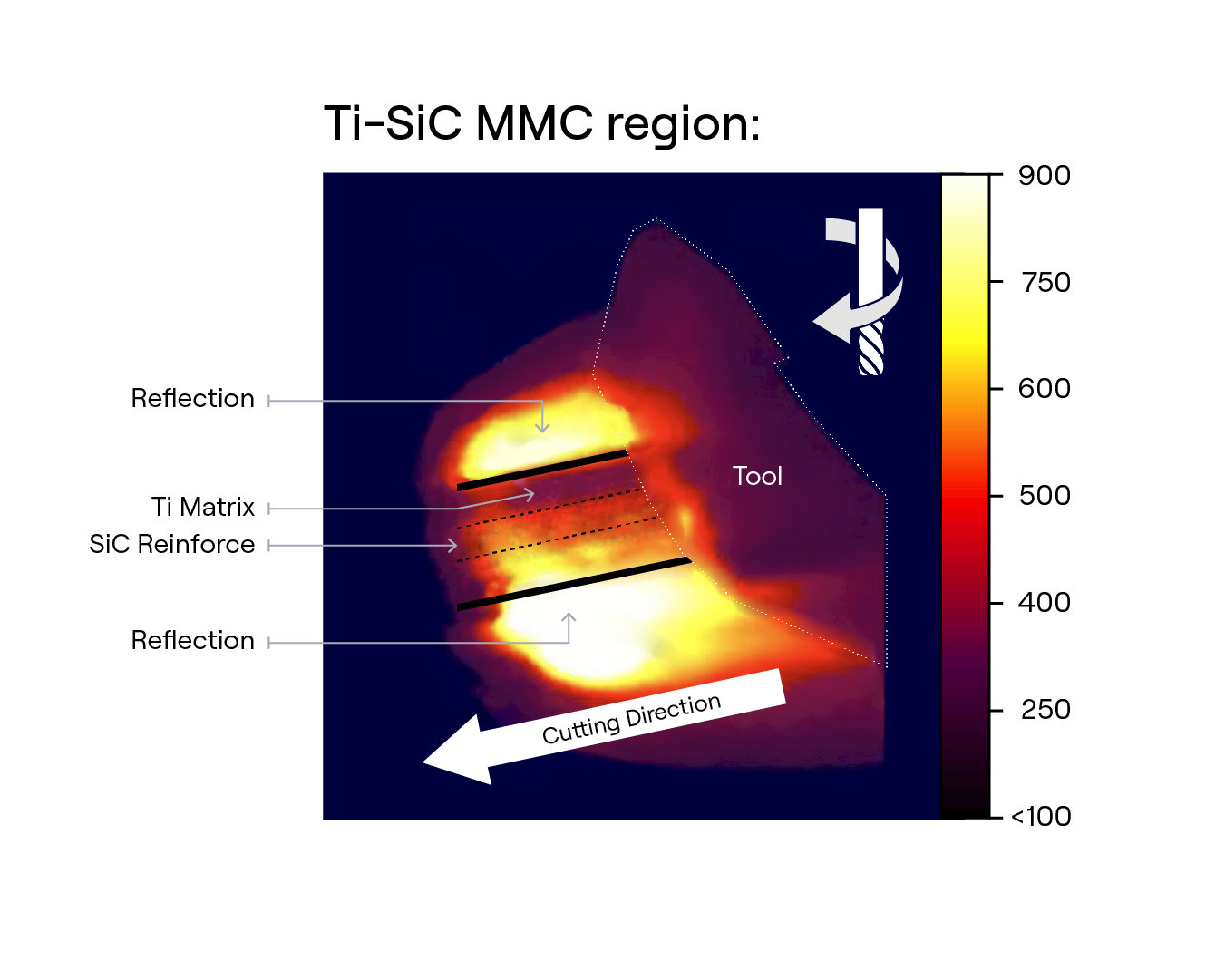
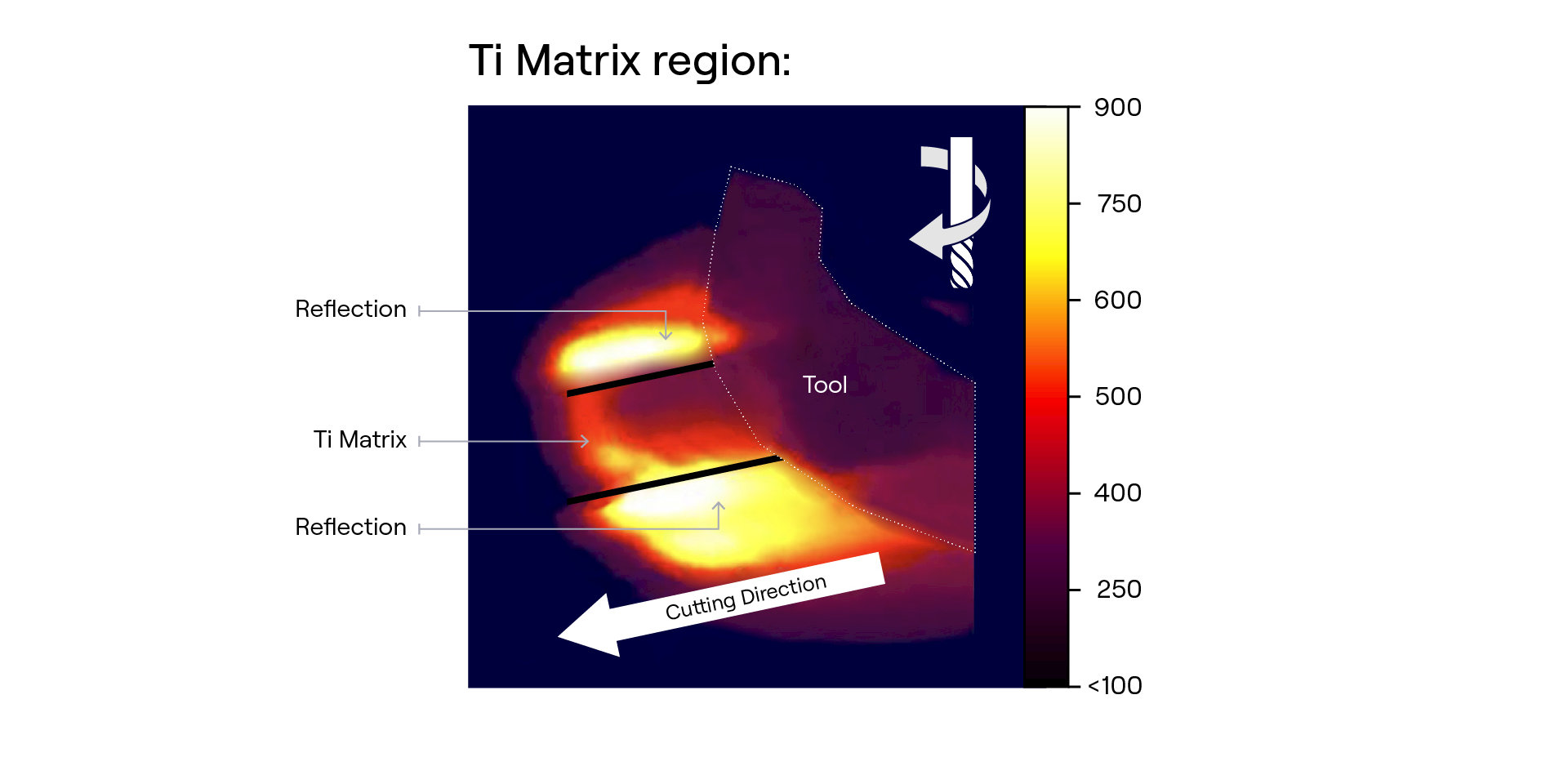
このような研究プログラムには具体的な利益が必要です。そして今回のケースでは、Nottingham 大学を拠点とするプロジェクトは確かに収益要件を満たしていると Kyle-Henney は語ります。
「航空機の着陸装置に使用している材料は、鋼材の半分の重量です。この部品だけで年間 6万トンの CO2 排出量が削減されると計算されます。これは、航空機の着陸装置だけでも世界中の航空機全体で 900 万キロトンの重量軽量化に相当します。これをさまざまな部分に適用すると、環境維持の持続可能性の面で多大なメリットが得られます。ジェットエンジン、航空機構造、着陸装置を軽量化できれば、燃料効率に関して多大なメリットがあります。」
同氏はさらに、「航空機の運用レベルでは、従来の素材に比べてわずかなコスト差は燃料節約によって12~18 か月で回収でき、その後の 20 年間にわたって航空会社は燃料コストを節約し続けることになるだろう」と付け加えた。
機械加工プロセス自体も従来の機械加工に比べて効率化され、不要工程が大幅に減ります。
「航空機の着陸装置の強度は鍛造によるものです。これは長さ 1.5 メートル、幅最大 300 ミリメートルのチタンです。しかし、その 90 パーセントは機械加工されて削り取られ、切り屑になってしまいます。1キロあたり 60 ポンドかかるので、800 キロ以上廃棄するとなるとすべて不要になります。
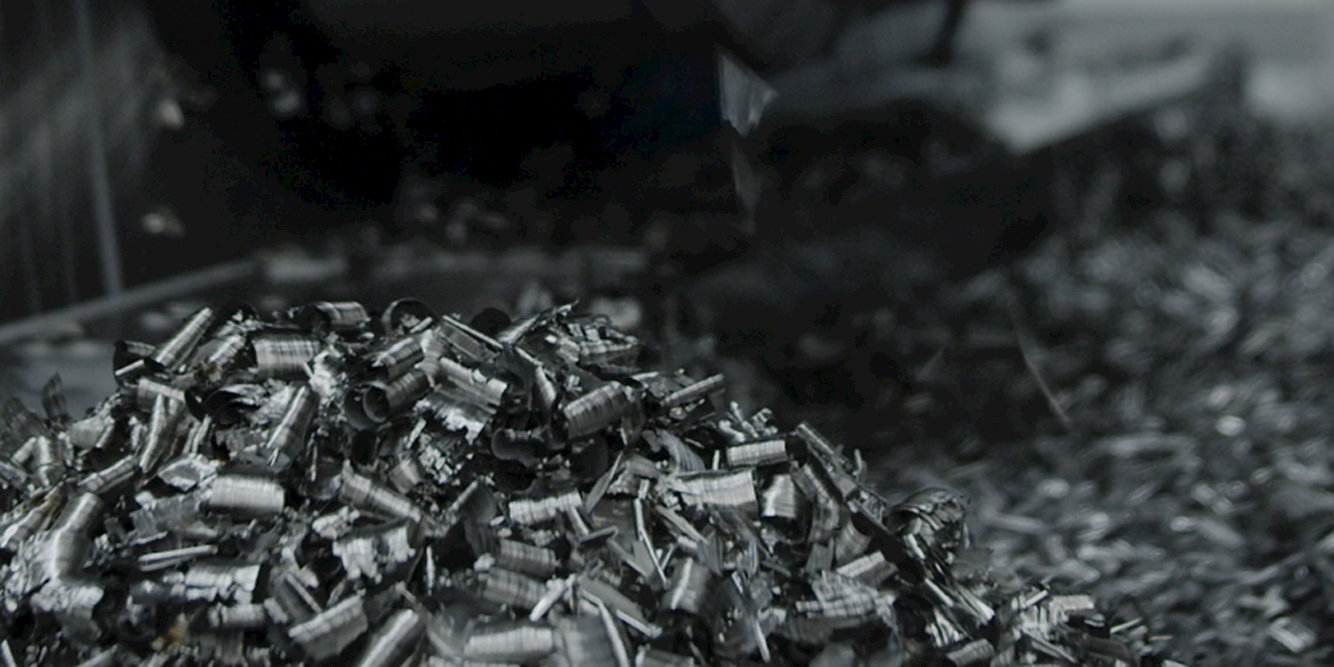
「当社の場合、処理コストが高く、セラミック繊維もコストを追加しますが、廃棄されるのは 20 ~ 50 キロだけなので、損失がそれほど大きくならないことでそのコストを相殺できます。むしろ、10~20%が不要になるだけです。」
この材料の他の潜在的な用途としては、エネルギー分野の蒸気タービンや医療産業( Attenborough は医療機器用のセラミック継手を製造しています)などがあります。
Mark Walsh は、Seco がこのプロジェクトに参加できたことを大変嬉しく思っていると語っています。「環境維持の持続可能性は、 Seco の中核的な価値観の 1 つであり、たとえ機械加工の削減が必要になったとしても、エネルギーを節約し、切り屑の無駄を削減するソリューションに貢献したいと考えています。工具寿命を最大化する」
「そして」と Stephen Kyle-Henney は付け加え、「これらの高性能材料の最終用途があり、その用途と経済性が実証され、生産と製造コストの効率が確立されれば、それをマーケットに拡大することができます。」
「今後、生産量が増えるにつれて、材料はより標準化され、機械加工も同様に標準化されるでしょう。これには大きな可能性があります。」
このプロジェクトで使用された製品について詳しく知りたい場合は、こちらをご覧ください:
インサート
F40M (コーティングインサート)
CBN200 (PCBN)
PCD20 (PCD)
PCD05 (PCD)
テストは、HSK-A63 スピンドルを備えた Hermle C32 工作機械プラットフォーム で実施されました。
Inline Content - Survey
Current code - 5fce8e61489f3034e74adc64