Step by Step Guide: How to Choose the Right Threading Tap
Learn how to select the ideal threading tap for various applications, ensuring precision and efficiency in your machining processesA successful tapping process is crucial in sectors where Seco’s tools are utilized. Choosing the right tap and applying the correct method can significantly impact thread quality, tool life and overall machining efficiency. Here, Radoslaw Zdanowski, Global Product Manager, Tapping at Seco, offers a step-by-step guide, highlighting the key considerations and decisions required to select the right tap and execute the process successfully to ensure optimal results for both standard and complex threading applications.
The two principal types of taps are hand taps, which are used manually with wrenches in a three-step process – rougher, intermediate, and finisher; and machine taps, which produce threads in one pass on machines ranging from drills to CNC centers. Seco focuses on high-performance machine taps made with two groups of steels – conventional steel with a high cobalt content and steels with high cobalt content obtained in the powder metallurgy process. Seco use the conventional option for T32, and the latter for T34.
The chip flow is dependent on the design of the flute. “For through holes, we use spiral point taps, which push chips forward,” says Zdanowski, “Whereas for blind holes, we recommend spiral flutes, which pull chips back. Straight flutes offer higher rigidity, but limited capacity, so are used for materials giving short chips.”
Seco’s T30, T32, and T34 series cover both flute types. The T35H, with its slow spiral for chip control and tool strength, is designed for heat-treated steels and aluminum with high silicon content. The T35K, meanwhile, is used with straight flutes, using internal coolant channels to manage the chip flow. Seco’s T33 forming taps come in TiCN or TiAlN + TiN coatings for different material needs.
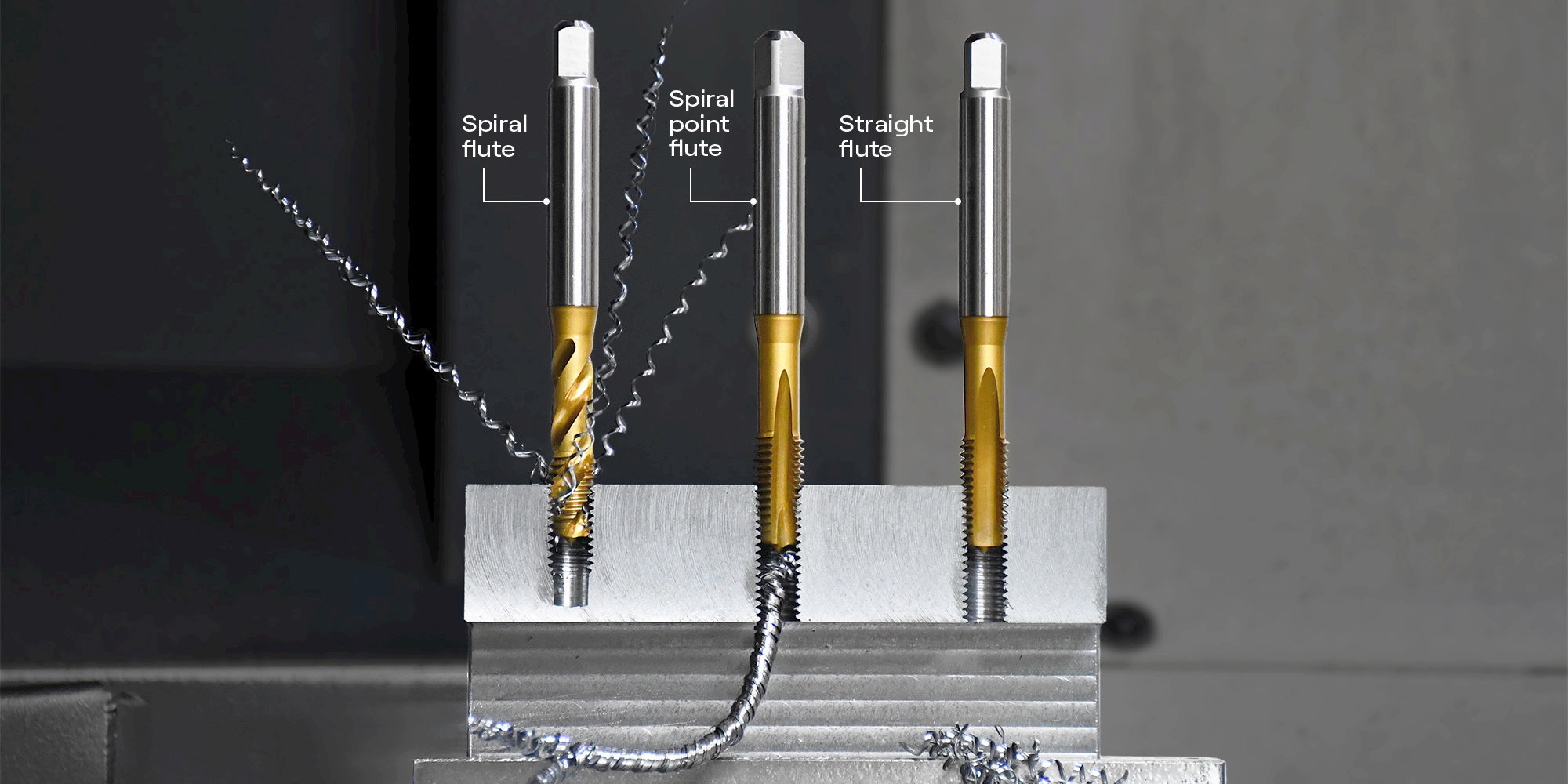
Matching the right tool and methodology to the materials of the job is critical to the success of a tapping job. “The basic rule is getting the right type of flutes,” says Zdanowski. “For long-chipping materials like steel, stainless steel and aluminum, Seco recommends gunpoint for through holes and spiral flutes for blind. For short-chipping materials like cast iron, we tend to recommend straight flute taps.”
High-tensile materials may require a reduced spiral angle that can offer better chip control and a larger core for improved tool strength.
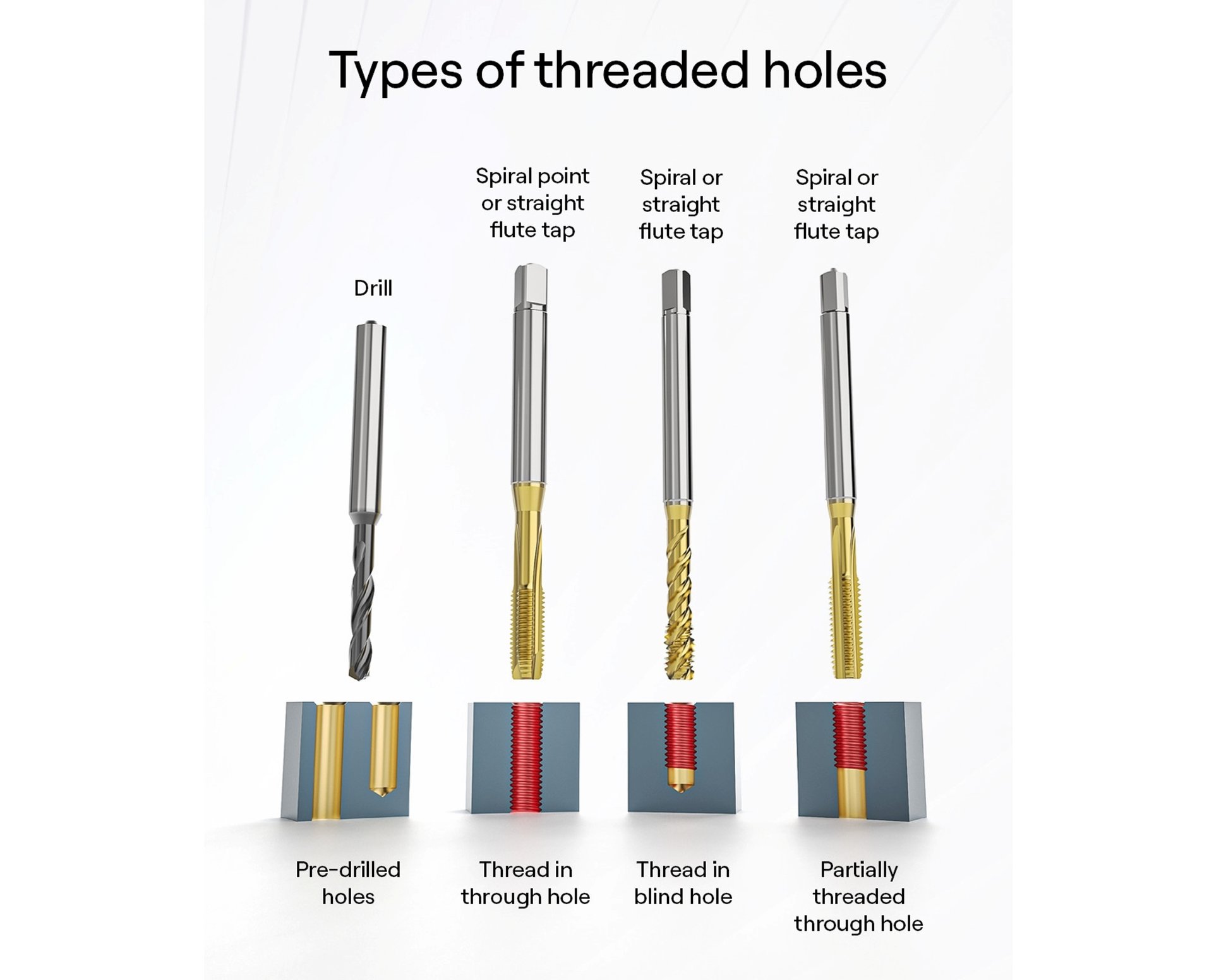
Another aspect to consider is coating. For example, Zdanowski recommends TiCN when working on aluminum and stainless steels, and TiAlN/TiN for more general steels, as seen in Seco’s T33 forming taps.
Cutting taps, like the T34, feature a multilayer coating – a TiAlN layer for temperature resistance, that is topped with tungsten carbide particles surrounded by a carbon layer. The benefit here is that the coating offers lubricity and reduces built-up edge in stainless steel, that, in turn, helps extend tool life.
Tolerances also play a role. “The most common tap class for metric threads is 6H, but for abrasive materials, we raise it, marked as 6HX. The lower tolerance limit accounts for wear, the higher limit, machine runout” says Zdanowski.
T35K and T35H taps, made for cast iron or heat-treated steels, come with this raised tolerance as standard, so it is possible to stay longer within limits of the thread in the component.
Inline Content - Gridded Links
Tags: 'wp_drills_taps'
Max links: 1
The component designer tends to determine the thread size based on strength calculations, to ensure that the connection can pass the load.
What the tap user can control, however, is tolerance. “Some threads are produced before additional operations like galvanizing or coating which change the dimensions of a thread,” says Zdanowski. “In such cases, we need to make some back calculations.”
Standard taps, like those in Seco’s T32 range, come in basic 6H tolerance or “oversized 6G,” which is suitable for coatings or looser fits. The pitch diameter of an internal thread before treatment will be four times larger than the coating thickness, so proper calculations are essential. If a customer is in any doubt they can ask for a special solution, Zdanowski adds.
The most common are connection threads, like metric, UN or BSW, have the same role – the creation of connection and resistance to self-disconnection. The main difference between them is the measurement unit.
The next group is pipe threads: G, NPT, Rp and Rc. These are used for hydraulics, to achieve tightness with or without additional sealing.
The third group is threads for power screws, such as Trapezoidal/ACME. They are characterized by their high efficiency which helps to transfer load.
Finally, EG/STI threads are used for wire inserts. These have larger diameters compared to regular metric or UN threads to enable the fitting of a wire insert. This improves thread strength in soft materials and are also used the for reparation of a damaged thread.
- Base on drawing and application needs
For precise connections, choose 4H (metric); for looser fit or coatings, use 6G
- Determine thread size and tolerance
- Check material suitability (e.g., T32, T35P, T35H)
- Refer to Seco’s catalog or website for recommended tools, geometries and coatings
- Blind holes – spiral flutes (pulls chips up)
- Through holes – gunpoint (pushes chips forward)
- If space behind is limited, pull chips back, even in through holes
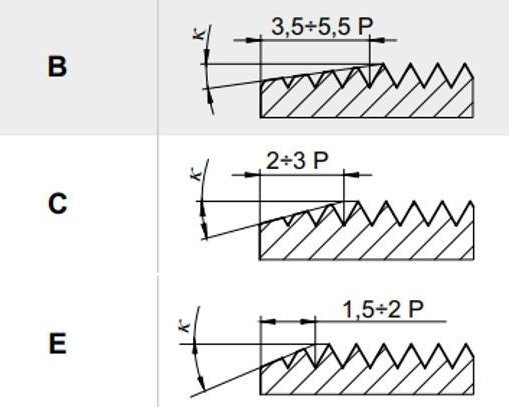
- For blind holes chamfer C (2–3 threads) offers longer tool life, while chamfer E (1.5–2 threads) allows threading closer to the bottom, but it wears faster. When space is limited, chamfer E is used to minimize the unusable thread length despite its reduced durability
- Location of thread may require an extra-long shank (e.g. for stepped holes)
- Use reduced shank taps for tight access or reinforced shanks for top surface access
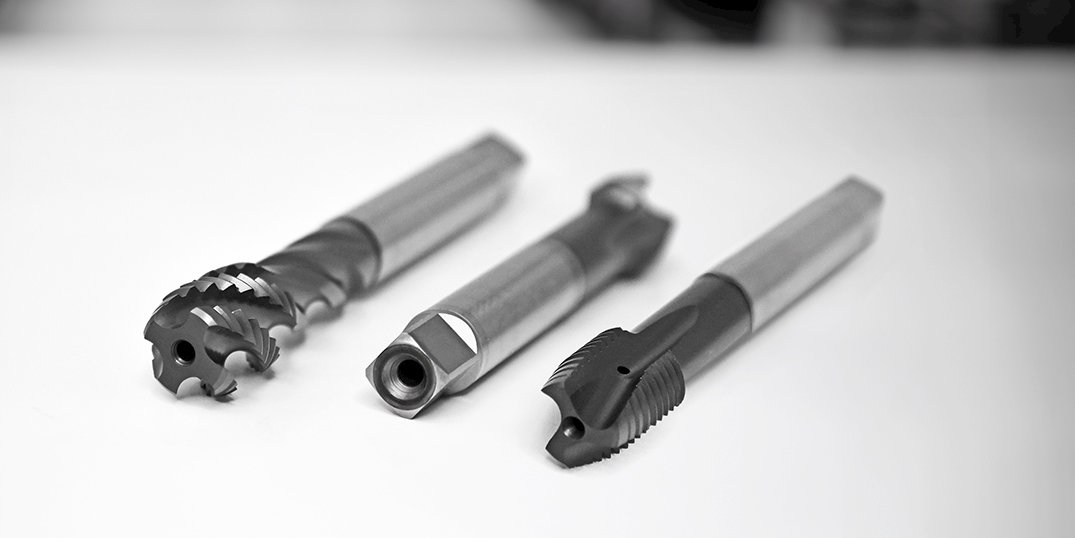
- Use Seco’s “Suggest” (based on component details)
- Alternatively, use “My Pages” on Seco website to filter tools by flute type, chamfer, tolerance, etc.
Making mistakes in the choice of tools and methodology employed can have grave consequences for job accuracy, efficiency and tool life. One common error is to use short chamfer E unnecessarily, shortening tool life, when there’s enough space for a longer chamfer. Another is not checking chip space. “Collars or walls disturbing chip flow may require different flute geometries or reduced spiral angles, like the T35H, which can help break chips and makes evacuation easier,” says Zdanowski.
Using axial coolant channels for through holes is another common mistake. Here, the coolant escapes, consequently causing “dry machining.”
Selecting the wrong tapping cycle on CNC machines can also cause failures. If mixed, taps can break because the feed and spindle rotation are not synchronized.
Coolant nozzle positioning is a critical consideration, too, especially in horizontal machining where gravity makes reaching the cutting zone more difficult.
Assuming lower cutting speeds are safer is another common misconception according to Zdanowski. “In tapping, increasing cutting speed often helps throw chips out. Some CNCs even support slower speed for cutting, and faster for retracting, to improve chip evacuation while maintaining safety.
And one final point he makes is that users sometimes overlook manufacturer recommendations. This can lead to them applying taps in unsuitable materials, resulting in a less perfect job and other unnecessary consequences.
In conclusion, while no set-up is totally mistake-proof, by choosing the right tool for the job, following best practices and applying each step of advice carefully, machinists can rule out most eventualities. The result is a more precise operation, better overall precision and improved tool life. In the kind of sectors in which Seco tooling excels, these small margins can make all the difference.
Inline Content - Gridded Links
Tags: 'thread tapping'
Max links: 1
Inline Content - Survey
Current code - 5fce8e61489f3034e74adc64