Équilibrer les facteurs clés pour l'usinage de l'acier inoxydable
L'acier inoxydable est dur et résiste à la chaleur et à la corrosion. Pour l'usiner, il faut équilibrer les propriétés et les géométries de l'outil avec des paramètres de coupe agressifs.Les aciers inoxydables sont des matériaux polyvalents qui allient robustesse et résistance à la chaleur et à la corrosion. Ces propriétés structurelles exceptionnelles rendent l'usinage plus difficile. Les ateliers ont besoin d'un équilibre minutieux entre les propriétés et les géométries des outils coupants et des paramètres de coupe agressifs pour obtenir un usinage productif dans ce type d'aciers. Avec la bonne configuration et les bons réglages, le tournage des aciers inoxydables devient moins complexe et plus intéressant.

Les aciers inoxydables se répartissent en cinq familles : ferritique, martensitique, austénitique, duplex et à durcissement par précipitation. Les propriétés et les applications uniques de chacune d'entre elles posent des problématiques d'usinage différentes.
En savoir plus sur le groupe matières
Les alliages d'aciers inoxydables standard sont ferritiques ou martensitiques. Les alliages ferritiques contiennent 10%-12% de chrome et ne peuvent pas être durcis. Les alliages martensitiques contiennent davantage de chrome et de carbone, ainsi que du manganèse et du silicium, et sont durcis par traitement thermique. Aujourd'hui, les alliages inoxydables ferritiques et martensitiques sont utilisés dans les articles ménagers tels que les outils de cuisine ou de jardinage. Ils ne sont plus le premier choix pour les environnements industriels. Les alliages d'aciers inoxydables ont évolué pour offrir une meilleure résistance mécanique et à la corrosion.
Pour renforcer cette résistance, les métallurgistes ont ajouté du nickel pour créer des alliages de fer/chrome/nickel, ou des aciers inoxydables austénitiques. Ces alliages sont couramment utilisés dans la pétrochimie, pour répondre aux exigences d'hygiène de l'industrie alimentaire et dans la fabrication de machines destinées à des environnements difficiles.
L'augmentation des performances s'accompagne de défis de production plus importants. Les alliages d'aciers inoxydables ferritiques et martensitiques ne sont pas beaucoup plus difficiles à usiner que les aciers ordinaires, car leur résistance à la corrosion est une propriété chimique. Toutefois, ces mêmes éléments qui augmentent la dureté, la ténacité, la résistance à la déformation et les propriétés thermiques des aciers inoxydables austénitiques réduisent également leur usinabilité.
Jusqu'à récemment, les opérateurs pensaient que la résistance des alliages austénitiques nécessitait des efforts de coupe plus importants, des outils à géométrie négative plus robustes et des paramètres de coupe réduits. Cette approche n'a pas été couronnée de succès. Elle se traduit par une durée de vie d'outil réduite, des copeaux longs, des bavures fréquentes, une irrégularité de surface et des vibrations indésirables.
L'acier inoxydable austénitique ne nécessite pas des efforts de coupe mécaniques beaucoup plus importants que les aciers traditionnels. Le principal défi des aciers inoxydables austénitiques réside dans leurs propriétés thermiques, qui nécessitent plus d'énergie pour l'usinage.
Mais la coupe des métaux est essentiellement un processus de déformation, et les aciers inoxydables austénitiques durcissent au cours de celui-ci. Les aciers inoxydables austénitiques combinent une faible conductivité thermique et une résistance élevée à la déformation, de sorte que leur usinage génère une chaleur excessive. Il est essentiel d'évacuer celle-ci de la zone de coupe. Contrairement aux copeaux d'acier ordinaire, les copeaux en acier inoxydable austénitique ne peuvent pas absorber et évacuer beaucoup de chaleur. Celle-ci reste au niveau de la zone de coupe, réduisant la durée de vie de l'outil.
Les fabricants d'outils conçoivent les substrats en carbure de manière à ce qu'ils puissent résister à la chaleur générée lors de l'usinage de l'acier inoxydable. La qualité de l'arête vive est aussi importante que la composition du substrat. Un outil plus acéré coupe l'acier inoxydable plutôt que de le déformer, ce qui réduit la génération de chaleur.
Même si la mauvaise conductivité thermique de l'acier inoxydable limite l'absorption de la chaleur par les copeaux, des débits copeaux plus importants évacuent davantage de chaleur. Pour évacuer efficacement la chaleur de la zone de coupe, il faut utiliser les profondeurs de coupe et les avances les plus importantes possibles afin de concentrer au maximum la chaleur au niveau des copeaux. Des profondeurs de coupe plus importantes réduisent également le nombre de passes nécessaires à la réalisation d'une pièce. L'acier inoxydable austénitique a tendance à se durcir lorsqu'il est usiné, de sorte qu'un nombre réduit de passes minimise les risques de détérioration.
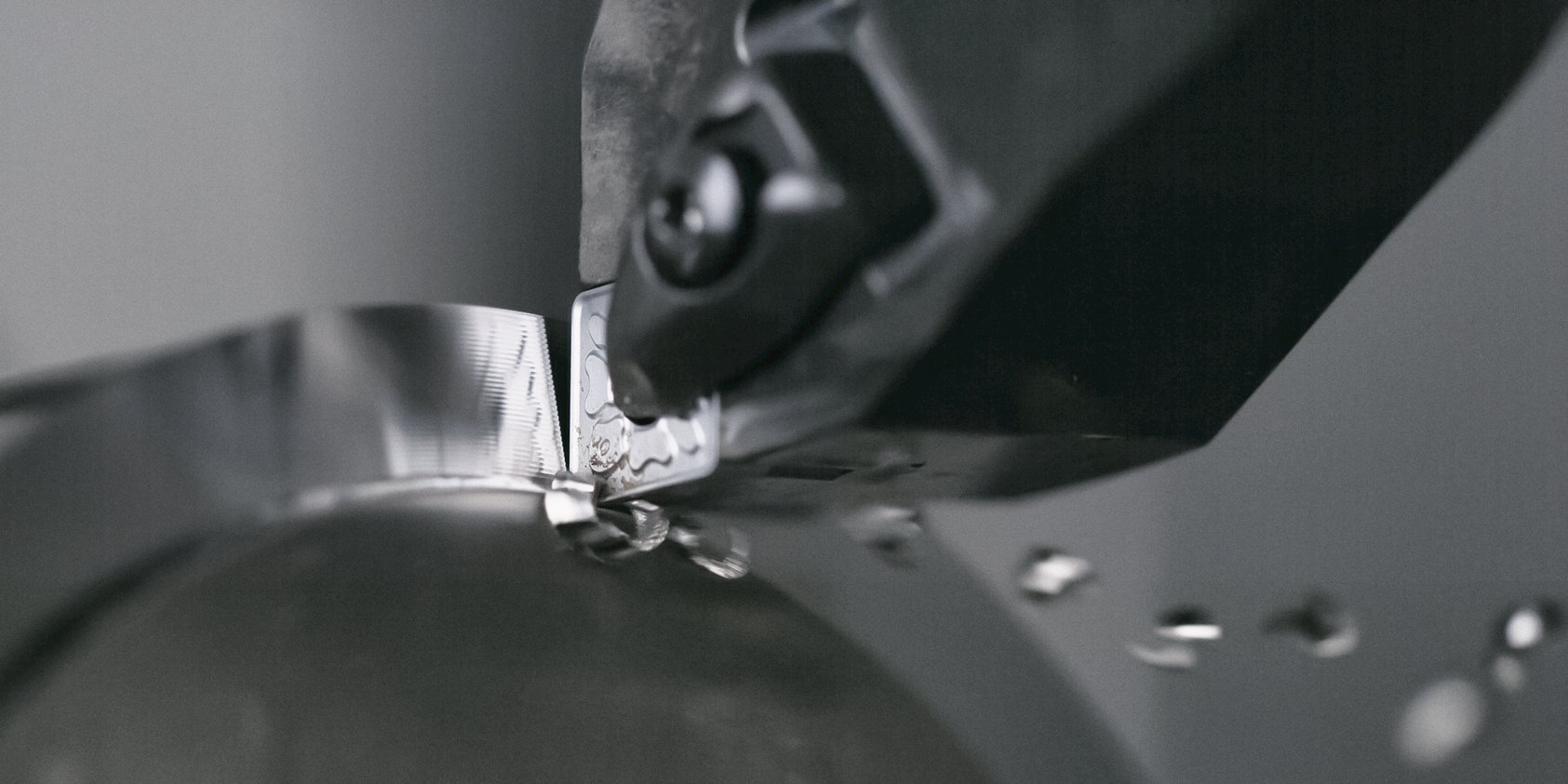
Ces méthodes d'usinage agressives ont des limites pratiques. Par exemple, les exigences en matière d'état de surface limitent les avances maximales. La puissance de la machine-outil, ainsi que la rigidité de l'outil coupant et de la pièce, limitent également les paramètres d'usinage.
Il est presque toujours essentiel à la réussite de l'usinage des alliages austénitiques en acier inoxydable. Utiliser une émulsion huile/eau de haute qualité contenant au moins 8 ou 9 % d'huile. En revanche, les opérations d'usinage courantes n'utilisent que 3 ou 4 % d'huile. Une pression plus élevée dans la zone de coupe améliore également les performances de l'arrosage. Les systèmes de distribution haute pression spécifiques tels que Seco Jetstream Tooling® sont encore plus efficaces.
Un revêtement dur appliqué sur la surface de l'outil renforce sa résistance thermique et prolonge sa durée de vie lors de l'usinage à des températures élevées. Les revêtements épais qui isolent le substrat de la chaleur n'adhèrent pas bien aux géométries très vives. Les fabricants d'outils coupants doivent donc concevoir des revêtements minces offrant une bonne barrière thermique. Certains alliages austénitiques d'acier inoxydable contiennent des inclusions dures abrasives. Un revêtement dur qui augmente la résistance à l'abrasion de l'outil coupant peut accroître sa durée de vie.
Les aciers inoxydables austénitiques sont très ductiles et ont tendance à coller à l'outil. L'usure par adhérence se produit lorsque la matière usinée adhère à l'outil et s'y accumule. Ces adhérences peuvent arracher des parties de l'arête de coupe, ce qui génère un mauvais état de surface et une défaillance de l'outil. Les revêtements peuvent offrir un pouvoir de lubrification qui empêche l'usure par adhérence. Des vitesses de coupe plus élevées permettent également de minimiser l'usure liée à l'adhérence.
L'usure par entaille est une forme extrême et très localisée d'usure par frottement qui résulte de l'écrouissage pendant l'usinage. Les différentes profondeurs de coupe répartissent les zones d'usure sur l'arête. Associée à des revêtements appropriés, cette stratégie permet d'atténuer l'usure par entaille des aciers inoxydables austénitiques.
Les fabricants d'outils équilibrent les propriétés de l'outil pour obtenir des performances optimales dans des matières spécifiques à la pièce à usiner. La recherche sur les nuances en carbure vise à équilibrer la dureté et la ténacité. Cela permet d'obtenir un outil suffisamment dur pour résister à la déformation, mais pas au point de se briser. De même, la géométrie des arêtes de coupe vives n'est pas aussi résistante que celle des arêtes rondes. Les fabricants d'outils s'efforcent de créer des outils qui équilibrent acuité et résistance.
Les fabricants d'outils revoient leurs directives d'application au cours du développement de l'outil. La plupart des recommandations de paramètres d'usinage sont basées sur la ténacité et la dureté des aciers traditionnels. es recommandations ne tiennent pas compte des facteurs thermiques liés à l'usinage des aciers inoxydables austénitiques et d'autres alliages à hautes performances. En collaboration avec des chercheurs universitaires, les fabricants d'outils ont commencé à revoir leurs procédures d'essai à la lumière des caractéristiques thermiques de ces matériaux.
Les nouvelles lignes directrices pour les essais reflètent le développement de nouveaux matériaux de référence. Les normes d'usinabilité traditionnelles s'appuient sur un alliage d'acier et sur les charges mécaniques produites lors de son usinage. Aujourd'hui, les fabricants d'outils ont établi une matière de référence distincte pour les aciers inoxydables austénitiques, avec des valeurs de base appropriées pour les vitesses, les avances et les profondeurs de coupe. Pour obtenir une productivité optimale dans des matériaux présentant diverses caractéristiques d'usinage, les fabricants d'outils appliquent des facteurs d'équilibrage ou d'étalonnage par rapport à cette matière de référence.
De nombreux outils coupants offrent des performances très acceptables dans divers matériaux, dans de nombreuses conditions de coupe et avec de multiples paramètres d'usinage. Ces outils peuvent offrir une productivité raisonnable et économique ainsi que des pièces de qualité pour des travaux ponctuels.
Toutefois, pour obtenir une productivité et une fiabilité maximales dans des matières spécifiques, les fabricants d'outils manipulent et équilibrent en permanence une grande variété d'éléments constitutifs de ces derniers. Les éléments de base d'un outil sont le substrat, le revêtement et la géométrie. Chacun est important. Dans les meilleurs outils, ils fonctionnent comme un système pour produire des résultats qui dépassent la somme de leurs parties.
Certaines parties d'un outil, y compris leur géométrie, jouent un rôle actif. La géométrie peut modifier la production et l'évacuation de chaleur, la formation des copeaux et l'état de surface réalisable. À l'inverse, les substrats et les revêtements jouent un rôle passif. Ils sont conçus pour équilibrer la dureté et la ténacité, supporter des températures élevées et résister à l'usure chimique, à l'adhérence et à l'abrasion.
Les plaquettes de tournage traditionnelles M3 et M5 de Seco offrent des exemples de base de différences de géométrie susceptibles de modifier les performances. Les deux présentent des géométries d'arêtes de coupe négatives (angle de dépouille de 0˚) et des zones en T entre l'arête de coupe et la face de dépouille de l'outil. La géométrie polyvalente M3 de moyenne ébauche offre une bonne durée de vie de l'outil et un bon brise-copeaux dans une large gamme de matières usinées. Les géométries M5 sont adaptées aux applications d'ébauche exigeantes et à forte avance. Elles combinent une grande résistance des arêtes avec des efforts de coupe relativement réduits.
Malgré leur polyvalence, les géométries M3 et M5 sont robustes mais ne sont pas totalement vives. Dans l'acier inoxydable austénitique, elles génèrent une chaleur considérable par déformation. En revanche, les géométries Seco MF4 et MF5 présentent des géométries positives et vives. Leurs listels en T positifs plus étroits aident à maintenir l'acuité tout en fournissant un support derrière une arête vive. Ces géométries ouvertes et à coupe douce facilitent les opérations de finition dans les aciers et aciers inoxydables. La géométrie MF5 est particulièrement efficace dans les applications à forte avance.
Pour obtenir les bons résultats, les opérateurs ont besoin d'outils adaptés aux matières qu'ils utilisent. Pour des matériaux complexes et exigeants comme les aciers inoxydables austénitiques, cela implique d'utiliser les outils et les méthodes d'usinage adéquats pour compenser le comportement propre aux métaux. Les nouvelles conceptions d'outils offrent une réponse optimale au défi que représentent les matériaux polyvalents mais difficiles à usiner.