最小限の工具によって優れたステアリングナックルを生産
既存のインサートに対応する最適化された多機能工具により、最小限の工具でステアリングナックルの生産を容易に改善できます。ステアリングナックルにはホイールハブやスピンドルが含まれており、自動車のサスペンションコンポーネントに取り付けられています。これらのコンポーネントは球状可鍛鋳鉄、鍛造鋼、アルミニウム合金で製造されており、フロントサスペンションの安全性にとって重要であるため、高品質の加工仕上げ、高精度な曲率径、完璧な機械加工の平面性精度が要求されます。
新しい自動車ブランドや最新技術が導入されるにつれ、地上走行車両の製造企業は材料容量、規制要件、熟練労働者不足などの課題に直面しています。最新の自動車に対する利用者からの要求を満たすステアリングナックルを確実に製造できるように、生産プロセスを自動化し、工具を簡素化する対策を模索しています。同時に、製造企業ではより多くの部品をより速く製造し、部品あたりの製造コストを削減することを期待しています。
ハイブリッド車、電気自動車、水素自動車などへの移行により、多くの自動車部品が刷新されて、生産ラインには新しい部品加工が追加されます。ステアリングナックルは、車両の種類に関係なく、構造部品の一部として残ります。その構造の複雑さと、仕様や形状を厳密に満たす必要性は、繰り返し可能な正確な加工精度を必要とします。
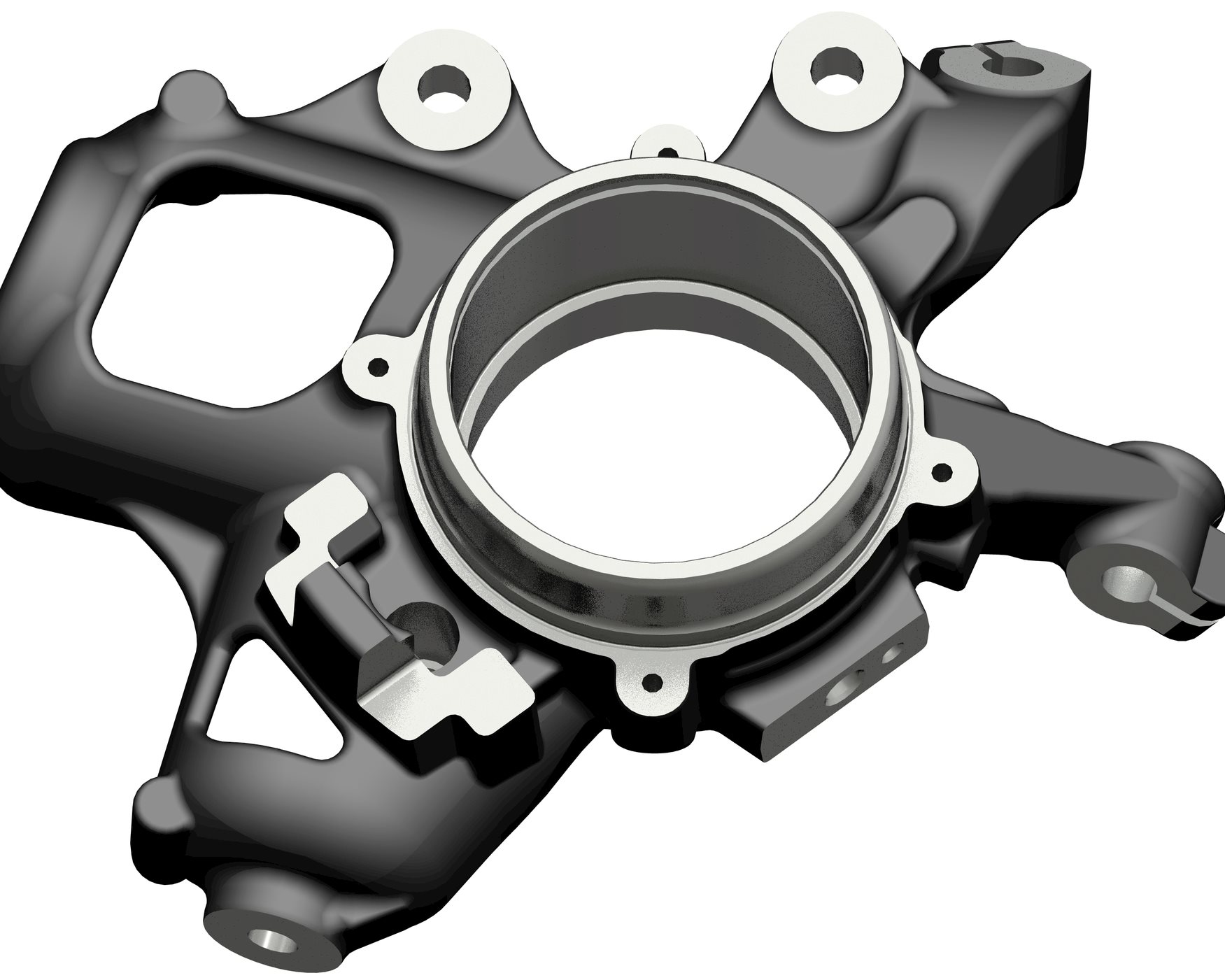
ステアリングナックルの形状デザインは車両モデルごとに根本的に異なりますが、それらはすべて特定の種類の生産プロセスを必要とします。Seco は、これらの生産に必要なフライス、穴あけ、溝入れ、リーミング、仕上げ工具などの完全な選択肢を提供しています。これらには、標準品工具やインサートだけでなく、特殊工具も含まれます。これらはすべて、加工振動を最小限に抑え、加工仕上げ品質を最適化し、切り屑コントロールを適正化し、生産プロセスの安全性を確保して、セットアップを容易にします。
生産を遅らせる大型で大重量の工具を使用せずに、加工部品の高い生産基準を満たすために、Seco は作業を簡素化する汎用的多機能工具を提供しています。さらに、80年以上にわたる実績を持った Seco の加工ソリューションを活用して、経験の浅いオペレータをトレーニングし、生産プロセスのボトルネックを解消させることができます。
大型で大重量の工具が原因となる生産効率の低下を伴わずに、高品質の生産結果を得るために、ステアリングナックル製造企業は、どの加工工程にも汎用的に適用できる多機能工具と特殊なオプションを探しています。Seco は、この特殊な一連の生産プロセス向けに、フライス、穴あけ、溝入れ、リーミング、仕上げツールの完全な選択肢を提供しており、その中には既存のインサートを活用できる工具も含まれます。
ステアリングナックル製造企業は、最小限の工具で加工振動を排除し、加工仕上げ精度と工具寿命を改善し、生産量を増加することができます。Seco は、最適な工具選定に加えて、80 年以上の機械加工の専門知識の経験と実績も提供しています。Seco は、ステアリングナックル製造企業が生産プロセスのボトルネックを解消し、進化の激しい業界で成功するために従業員のトレーニングの実施を支援します。
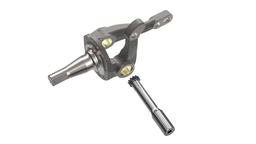
- 仕上げ加工や部品の製品品質を損なう可能性のある切り屑コントロール不良を解消する。
- ステアリングナックルの厳しい品質精度を満たす部品を製造する。
- 機械へのセットアップを簡素化する。
- 穴あけ加工の同心精度を確保する。
- 機械テーブル位置決め固定の際の工具交換を削減する。
- 中仕上げ加工を組み合わせて、工具の加工適用とステアリングナックルの加工サイクルタイムを削減する。
- 加工仕上げ面が損傷するリスクを回避する。
- 良好な切り屑コントロールを維持する。
- 高性能の機械テーブル位置決め固定設備を導入する。
- 切り屑をコントロールするために、穴加工および中仕上げ加工のための適正な切込み深さを維持してください。
- 同心精度を高めるために片側方向からのリーマ加工。
- サーメット材種を適用して工具設計を最適化します。
フェースミル加工
ドリル加工
リーマ加工
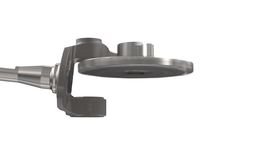
- 加工時の振動を低減する。
- 機械トルクの活用を最適化する。
- 加工面仕上げと工具寿命を改善する。
- 部品の形状複雑さを安定して作業できる治具を製作する。
- 長い工具突き出し部の課題を克服する。
- コントロールされていない加工振動は、部品の加工品質と結果を低下させる。
- 加工時の利用可能な機械トルクを最適に活用する必要がある。
- 不適切なセットアップと工具は加工面仕上げ精度を悪化させて工具寿命を短くする。
- 複雑な形状のステアリングナックル形状設計のため固定が煩雑になる。
- 長い工具のオーバーハングは加工振動の原因となる。
- 大きな刃先ノーズ径を持つ底部コーナー曲率部加工は、仕上げプロセスを複雑困難にする。
- 穴の長さが 80 mmを超えると、テーパ穴の加工が困難になる。
- ステアリングナックル製造のための工具を最適化します。
- ポジ形状の刃先適用によって切削抵抗を低減できます。
- 工具全体重量の軽量化。
- ダンプニングパッド機能 (振動抑制機能) 付きサイドカッタ。
- 粗い刃数ピッチのカッタ。
- プッシュまたはプル加工を適用します。
- 工具軸方向から配置固定されるインサートポケット仕様工具を適用します。
- ドライカットを推奨します。
スクエアショルダ加工
ドリル加工
リーマ加工
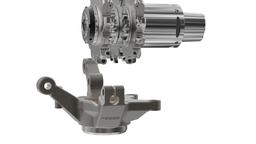
- 部品あたりの生産コストと生産時間低減する。
- ステアリングナックルの加工品質精度を確保する。
- 工具交換をできるだけ少なくする。
- 過度の消費電力を削減する。
- 加工振動によるリスクが増大することをコントロールする。
- 生産効率性と生産コストのバランスを適正化し最大限の収益性を確保する。
- ステアリングナックルの加工品質に必要な加工面仕上げ精度を確保する。
- 多用途多機能な工具設計により、工具収納マガジン内の工具数と交換頻度が減少します。
- 複数個所の同時切削による過度の電力消費を避けるために、サイドカッタの外周刃のコンタクトバランスをとる。
- 機能的な保持の検討により、加工振動を低減するように治具を設計します。
外周側カッタ
外周側インサート
内周側カッタ
内周側インサート
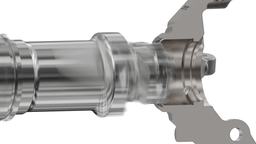
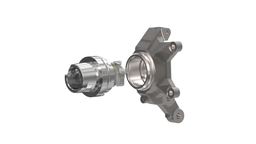

- 部品の寸法精度と品質精度に関する厳しい仕様に適合する。
- ステアリングナックル製造における熟練労働者が必要になる。
- 加工サイクル時間の短縮する。
- 工具交換を最小限に抑え、ステアリングナックル製造のサイクルタイムを短縮する。
- 自動化を実施して、最小限の介入で低コストで大量のステアリングナックル製造を実現する。
- 寸法精度に必要なプロセス安定性を維持確保する。
- 熟練オペレータが工具を設定または調整が必要になる。
- 汎用多機能工具や複合加工を実現するために、大型で大重量の工具を使用しない。
- 加工振動を最小限に抑え、加工面仕上げを高精度化する。
- トランスミッション径とベアリング径の間の同心精度を維持する。
- 汎用性のある多機能段付きボーリングホルダ特殊工具による粗加工、中仕上げ加工、面取り工程などを導入します。
- 溝加工工具には両面 ISO/ANSIインサートを適用します。
溝加工工具
特殊形状設計された一体型仕様の粗/中仕上げ工具
特殊設計されたリーマ工具
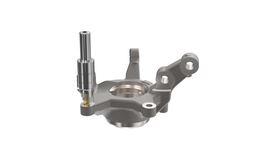
- 加工プロセスを複合化させて工具交換頻度を最小限に抑える。
- ステアリングナックル製造時に部品の保持固定安定性を維持する。
- 突き出しの長い工具の使用は回避する。
- 正面フライス加工、面取り加工、穴あけ加工を組み合わせて、工具交換を最小限に抑える。
- ツールマガジン内の必要な工具数を削減する。
- 部品を直接保持固定することなく、治具と部品のセットアップを簡易化させる。
- 長突き出しの長い工具の加工制限を克服する。
- 複数プロセス対応の工具設計により、工具交換頻度が低減して生産効率性が向上します。
- 部品の加工品質や費用対効果を犠牲にすることなく、ステアリングナックルの製造サイクルタイムを大幅に短縮できます。
ポジ形状の刃先設計のドリルと座繰り工具の組み合わせを加工に適用する。