8 Advantages of High Feed Milling with Indexable Inserts
Discover the top 8 advantages of high feed milling with indexable inserts for efficiency, speed, and cost control. Learn more now.High feed milling (HFM) with indexable inserts offers manufacturers a powerful advantage in pursuing greater efficiency, speed, and cost control.
High feed milling is particularly effective for roughing large parts and machining tough materials like superalloys and hardened steels—common applications where traditional techniques fall short.
Discover how to outpace the competition with our latest high feed whitepaper.
Download your free copy here.
Inline Content - Gridded Links
Tags: 'wp_high_feed_campaign'
Max links: 1
From superior material removal rates, extended tool life, and reduced machining costs, choosing high feed mills with indexable cutters could be your ticket to gaining that all-important competitive edge.
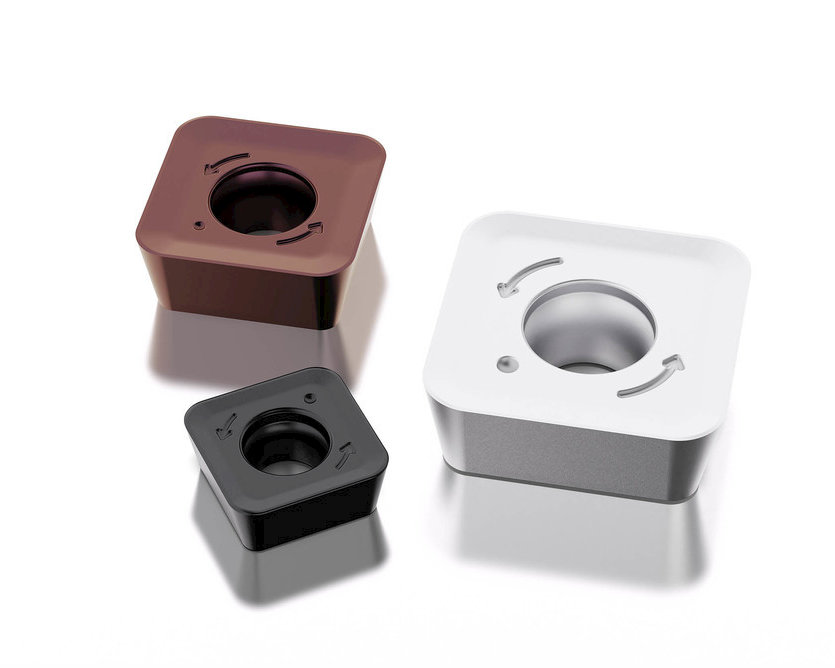
Here are our top eight advantages for you to consider.
- Go Faster: HFM removes material at unprecedented speeds by combining shallow cuts with high feed rates. The chip thinning effect allows for aggressive feeds without compromising tool life.
- Save Energy, Slash Costs: HFM optimizes machining efficiency, cutting power consumption and minimizing tool wear. Fewer secondary operations mean lower expenses, while coolant management further reduces costs.
- Shiny Surfaces: Thicker chips carry heat away from the tool, preserving tool life and improving surface finishes. While HFM generates heat, effective heat evacuation ensures performance. A finishing pass may be needed for the best results.
- Need for Speed: By utilizing high feed rates per tooth and shallow cuts, HFM maximizes material removal while reducing cycle times, making machining faster and more efficient.
- Replace and Go: Indexable inserts allow quick, easy replacement, minimizing downtime. Multi-edge designs provide a cost-effective alternative to solid carbide tools, lowering per-cutting-edge costs.
- Unrivaled Versatility: HFM adapts to various materials, such as steel, stainless steel, aluminum, and titanium. It excels in face milling, helical interpolation, pocketing, ramping, and plunging, making it a versatile choice.
- Maintain Control: Axial cutting forces improve stability, reducing deflection and chatter for precise machining. This ensures higher accuracy and consistency, even in long-reach applications.
- Good Vibrations: With cutting forces directed toward the spindle, vibration is minimized, enhancing tool stability. This is ideal for long-reach applications and thin-walled components.
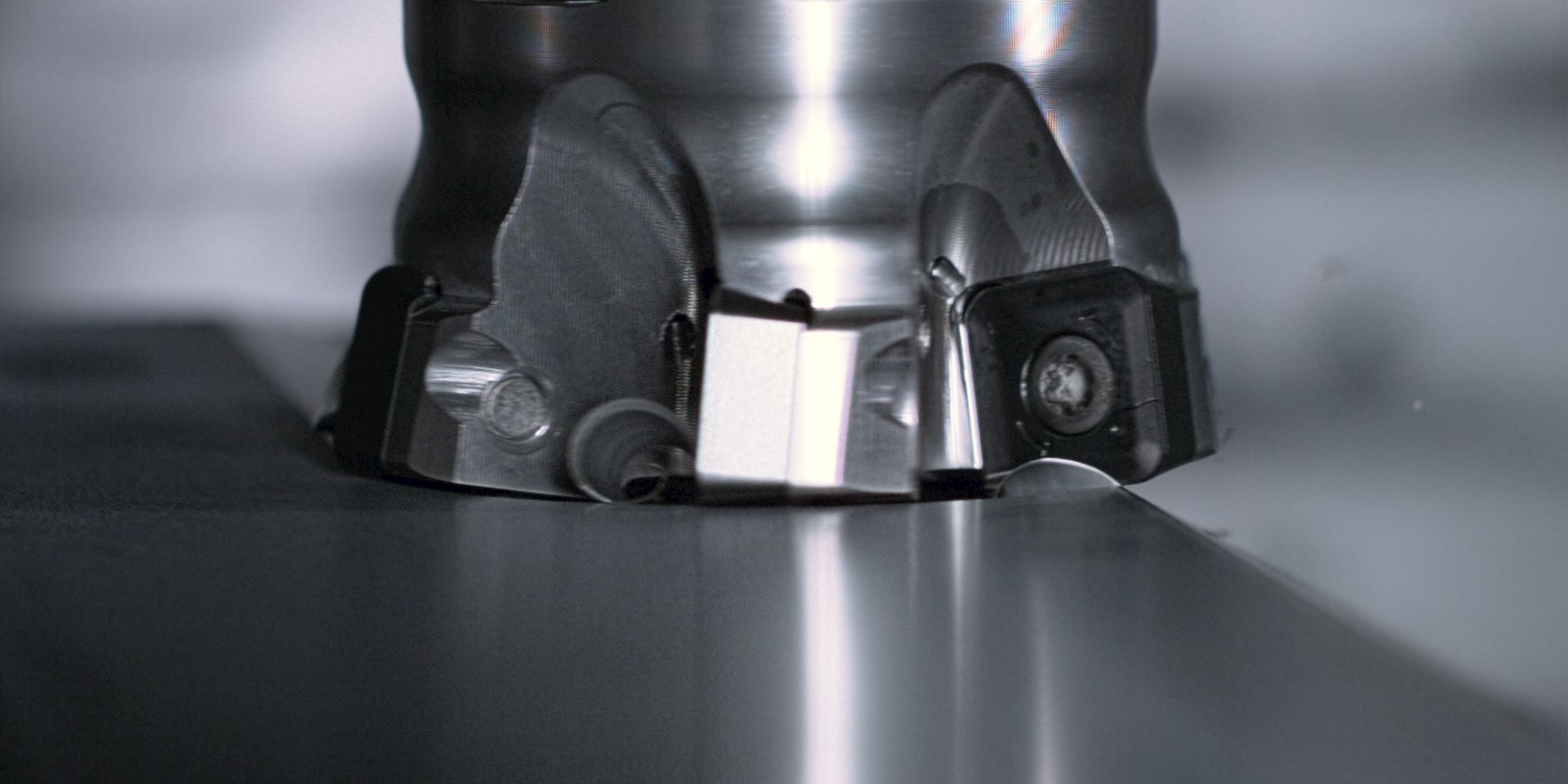
High efficiency milling (HEM) is great, but high feed milling is greater.
While HEM relies on small step-overs and deep cuts to boost metal removal rates by 50% or more, high feed milling takes it up a notch with shallow cuts and substantially higher feed rates.
The result? Faster speeds, longer tool life and exceptional performance across roughing operations and challenging materials.
High feed milling with indexable cutters can increase tool life by 60%, and machine energy consumption by 40% compared to conventional milling.
Milling Technique | Material Removal Rate (cm³/min) | Cycle Time Reduction (%) | Tool Life Increase (%) |
Conventional | 50 | 0 | 0 |
High Efficiency | 75 | 30 | 40 |
High Feed | 100 | 50 | 60 |
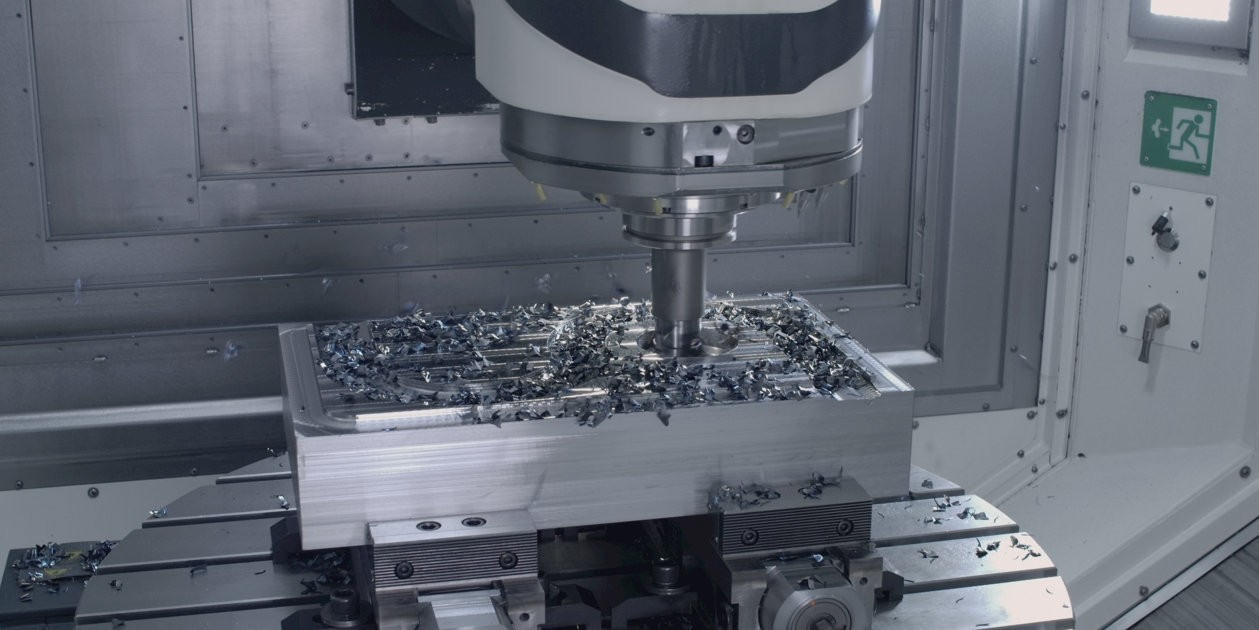
High feed milling with indexable cutters delivers high material removal rates, extended tool life, and cost-efficient performance.
Leveraging the chip thinning effect shortens cycle times, cuts power consumption, and enhances surface finishes. Plus, its versatility suits various applications and materials, while replaceable inserts ensure consistent, cost-effective machining.
In short, high feed milling with indexable cutters is a game-changer for manufacturers seeking efficiency, accuracy, and ultimate machining speed.
Inline Content - Survey
Current code - 5fce8e61489f3034e74adc64